Il est facile de se contenter de solutions de média d'écran qui nécessitent des temps d'arrêt pour le nettoyage et le remplacement. Améliorez votre débit, réduisez les temps d'arrêt et augmentez votre production grâce à la surface ouverte maximale et à la facilité d'utilisation des panneaux Maxi de Polydeck.
Dans un secteur qui remonte à des dizaines de milliers d'années, il est facile de se reposer sur ses lauriers lorsqu'on considère les facteurs de réussite et l'efficacité de ses opérations. Cependant, il est tout à fait possible de concevoir une opération efficace et avancée avec le bon média de criblage. La gamme Polydeck Maxi Les solutions de criblage à panneaux augmentent le débit et l'efficacité de la production d'une opération d'innombrables façons.
Le débit est, en termes simples, une mesure de la production et du succès. En termes de traitement des matériaux, cela signifie que votre média de criblage fait son travail. Un média de criblage efficace s'adapte à vos machines là où elles se trouvent, facilite le nettoyage et le remplacement, et assure un criblage maximal des matériaux avec le moins de temps d'arrêt possible. Pour de nombreuses opérations, l'efficacité est essentielle, en particulier lorsque les ressources sont limitées. S'arrêter pour dégager les bouchons et s'occuper d'une faible surface ouverte n'est tout simplement pas une option lorsque l'efficacité et la durabilité sont requises sur le site.
Si le support de l'écran ne fonctionne pas comme il le devrait, des arrêts coûteux en résultent, obligeant les travailleurs à passer des heures à déboucher les écrans et à les remettre en état pour qu'ils puissent reprendre la production. Client Polydeck Agrégats Dufferin Butler PitDufferin, situé à Cambridge, en Ontario, connaissait d'importants temps d'arrêt dus à l'encrassement. Avec une attention constante sur leurs objectifs d'efficacité et de production, Dufferin n'a pas perdu son temps à chercher une meilleure solution de média de tamisage. Après que l'équipe de Polydeck ait effectué une analyse de la performance des tamis sur place et présenté ses solutions avec la garantie que Dufferin atteindrait le débit désiré en faisant le changement, le choix a été simple.

Maxi Les bordures fines des panneaux sont spécialement conçues pour le débit, avec des angles en relief pour faciliter le criblage. Une fois les panneaux posés sur les cribles de nos clients, ils ont permis d'obtenir un nombre maximum d'ouvertures par mètre carré. En plus d'offrir des taux de rendement supérieurs, les polyuréthanes spécialement formulés des panneaux Maxi, combinés à la géométrie des panneaux, ont permis aux panneaux de fléchir et de conserver une durée de vie prolongée. Cette conception innovante, associée au processus de moulage par injection de Polydeck, a permis d'obtenir une surface ouverte précise et cohérente, ce qui s'est traduit par une augmentation de l'efficacité globale de Butler Pit.
Maxi Les panneaux Maxi offrent également un avantage par rapport au tissu métallique si l'on considère la résistance à l'abrasion du média synthétique et la facilité d'utilisation. Les opérations se tournent souvent vers le tissu métallique lorsque les exigences de production sont élevées, mais les panneaux Maxi offrent un avantage significatif en termes de coûts lorsque l'on tient compte des temps d'arrêt nécessaires pour remplacer le tissu métallique. La modularité des panneaux Maxi et les fermetures à pression rendent les changements et les échanges faciles et rapides. Moins de temps d'arrêt signifie plus d'heures productives sur le site. Plus de production signifie plus de rendement pour votre site. En bref, l'ajout des panneaux Maxi de Polydeck à vos opérations signifie que vous obtiendrez plus de votre site que jamais auparavant.
La clé du succès avec les écrans réside dans la technologie d'aujourd'hui et dans l'efficacité du système Polydeck. Maxi Les panneaux Maxi de Polydeck ont permis de réduire les temps d'arrêt et d'augmenter la production. Comme on peut le voir sur le site de notre client, les panneaux Maxi de Polydeck ont permis de réduire les temps d'arrêt et d'augmenter la production, deux éléments très importants pour le succès de toute opération.
Êtes-vous prêt à accroître le succès de votre opération ?
Lorsque vous éliminez les goulots d'étranglement du haut de la chaîne, vous augmentez la capacité de production et mettez davantage de produits vendables sur le terrain. Découvrez comment Polydeck a permis d'atteindre un niveau d'efficacité supérieur de manière rentable.
Si vous exploitez une usine d'agrégats, vous savez que l'industrie de la construction est un élément essentiel de l'économie. efficacité Le rendement de vos cribles à pont supérieur est essentiel pour les performances globales de votre exploitation. Il s'agit d'une formule simple : Lorsque vous éliminez les goulots d'étranglement au niveau du pont supérieur, vous augmentez la capacité de production et mettez davantage de produits vendables sur le terrain. Mais comment les opérateurs peuvent-ils atteindre ce niveau d'efficacité de manière rentable ?
La réponse de Polydeck à cette question est une équation de média d'écran qui combine des panneaux d'écran modulaires en fils soudés avec panneaux de médias synthétiques. Chaque type de panneau modulaire est placé stratégiquement sur le pont supérieur pour offrir une surface ouverte maximale et une durée de vie supérieure. Pour les opérateurs, le résultat est un débit plus élevé et une réduction des temps d'arrêt pour la maintenance = plus de profit et moins de dépenses.
Partenaire Polydeck, Ressources d'Alleytonest un producteur de granulats et de béton prêt à l'emploi dont le siège social est situé à Houston, au Texas. Ses activités comprennent 11 sites de CMR et huit sites de traitement des granulats, et il fournit à ses clients des services de transport de matériaux, de livraison de béton prêt à l'emploi, de pompage de béton, ainsi que de sable stabilisé et de boue.
Brandon Genzer (directeur de l'usine Vox d'Alleyton à Garwood, TX, à l'époque) était confronté à des dépôts grossiers sur le site ainsi qu'à des difficultés pour évacuer le pont supérieur de leur crible secondaire humide à finition inclinée, qui était équipé d'un média en polyuréthane.
"Le crible est alimenté par un matériau de 2-1/2 pouces de moins", explique-t-il, "Nous avions beaucoup d'entraînement de matériau de 1-1/2 pouces, ce qui créait des charges de recirculation inutiles qui retournaient au concasseur."
Il s'agissait d'un énorme problème pour l'entreprise, car les charges de recirculation augmentent considérablement l'usure du concasseur et les coûts d'exploitation par tonne. Les marges bénéficiaires de l'installation étaient sapées par le fait que le produit fini était renvoyé vers le concasseur au lieu d'être stocké dans le stock de produits vendables.

Pour éliminer ce problème coûteux de report, Genzer a consulté le responsable de Polydeck pour la région du sud du Texas à l'époque, Kent Ropp. "Je travaille en étroite collaboration avec chaque producteur de ma région pour analyser son application et créer des configurations de panneaux d'écran modulaires qui offrent les spécifications souhaitées."
Ropp a travaillé avec Genzer pour spécifier les nouveaux médias en effectuant plusieurs heures de fonctionnement pour chaque échantillon de matériau. "Nous avons branché différents médias pour ajuster notre module de finesse (FM) à nos besoins", se souvient M. Genzer.
Ropp a finalement recommandé une combinaison des produits haute performance de Polydeck. Pour une plus grande surface ouverte et un plus grand débit, les produits de Polydeck ont été choisis. METALDEX™ Des panneaux modulaires en acier ont été installés à l'extrémité de décharge du crible de 6 x 16 pieds de l'installation. Pour absorber l'impact sur l'extrémité d'alimentation de l'écran, RUBBERDEX Des panneaux en caoutchouc synthétique ont été installés pour maximiser la durée de vie du pont supérieur. Les ponts intermédiaires et inférieurs ont été équipés de panneaux de POLYDEX panneaux-écrans modulaires en polyuréthane.

Le METALDEX™ offrent une surface ouverte égale ou supérieure à celle des toiles métalliques traditionnelles ayant la même ouverture et le même diamètre de fil. En plus d'une plus grande surface ouverte, la modularité des panneaux permet aux opérations de les appliquer à l'extrémité d'alimentation ou, plus important encore, à l'extrémité de décharge où une surface ouverte accrue est essentielle pour éliminer les charges de recirculation.
Les tests effectués par Ropp à l'usine de Vox ont déterminé que l'ajout de panneaux Metaldex à l'extrémité de décharge a augmenté les performances du crible à 55,9% de surface ouverte par rapport aux 33,4% obtenus avec les anciens panneaux en caoutchouc synthétique.

"Nous obtenons également une bonne durée de vie des panneaux", rapporte M. Genzer. "Même en cas d'horaires prolongés de 12 à 16 heures, le premier jeu a duré plus de quatre mois. Lorsque nous prolongeons les horaires, nous vérifions les écrans à la fin de chaque poste. Si nécessaire, l'équipe peut changer les panneaux en quelques minutes, et nous sommes de nouveau opérationnels."
Selon M. Ropp, la clé de la durée de vie supérieure de METALDEX est la suivante : "Il est composé d'acier AR 500 Brinell résistant à l'abrasion, ce qui prolonge la durée de vie dans la plupart des applications par rapport à celle des toiles métalliques standard. Le fil soudé offre simplement un degré de performance plus élevé en termes de solidité et de résistance à la corrosion."
Un autre bonus pour l'usine Vox est que METALDEX™ Les panneaux frottent mieux le matériau, éliminant la teneur en argile. "Nous obtenons maintenant le meilleur des deux mondes : une roche plus propre et un débit plus élevé", explique M. Genzer, ajoutant que l'usine produit en moyenne 550 tonnes par heure, une augmentation significative depuis que le circuit de criblage a été mis au point. Depuis, Alleyton a mis en place un système METALDEX™ dans une autre exploitation pour aider à briser et à éliminer l'argile contenue dans leur matériau.
La flexibilité du traitement étant importante pour l'installation de Vox, qui produit principalement des matériaux de 1,5 pouce de diamètre, de 3,8 pouces de diamètre et du sable à béton, la modularité des panneaux de criblage permet de changer facilement les panneaux ou d'affiner les configurations pour s'adapter aux différents flux de matériaux ou aux exigences de traitement. Les bords de chaque panneau en fil métallique soudé de 1 pi x 2 pi sont également recouverts de polyuréthane, ce qui les rend beaucoup plus faciles à manipuler que les grandes sections de toile métallique.
"METALDEX™ est une autre conception de panneau de criblage révolutionnaire de Polydeck qui améliore la gamme de solutions de criblage et aide nos clients à atteindre leurs objectifs de production", déclare Ropp. "Il offre la durée de vie prolongée de l'acier résistant à l'abrasion avec la surface ouverte du tissu métallique, et l'ingénierie modulaire permet une manipulation facile et une fixation simple au système de cadre à longerons de Polydeck."
L'élimination des goulots d'étranglement du criblage est essentielle pour maximiser le rendement du criblage du pont supérieur, ce qui est, à son tour, essentiel pour une performance optimale de l'usine. À l'usine de Vox d'Alleyton Resources, la combinaison innovante de Polydeck de fils soudés et de panneaux de médias synthétiques était la formule précise pour résoudre leurs problèmes de criblage.
Le NOUVEAU METALDEX de Polydeck™ VR

En 2020, Polydeck a lancé une nouvelle offre de produits, METALDEX.™ VR. La nouvelle solution de tamisage modulaire de Polydeck s'intègre à notre PIPETOP™ système de limons. Parfait pour les applications d'encollage à sec nécessitant une surface ouverte et une efficacité accrues, METALDEX™ Le VR est idéalement installé sur l'extrémité de décharge, où il offre une plus longue durée de vie et un meilleur débit, et son motif unique en forme de diamant élimine le blocage et les bouchons.
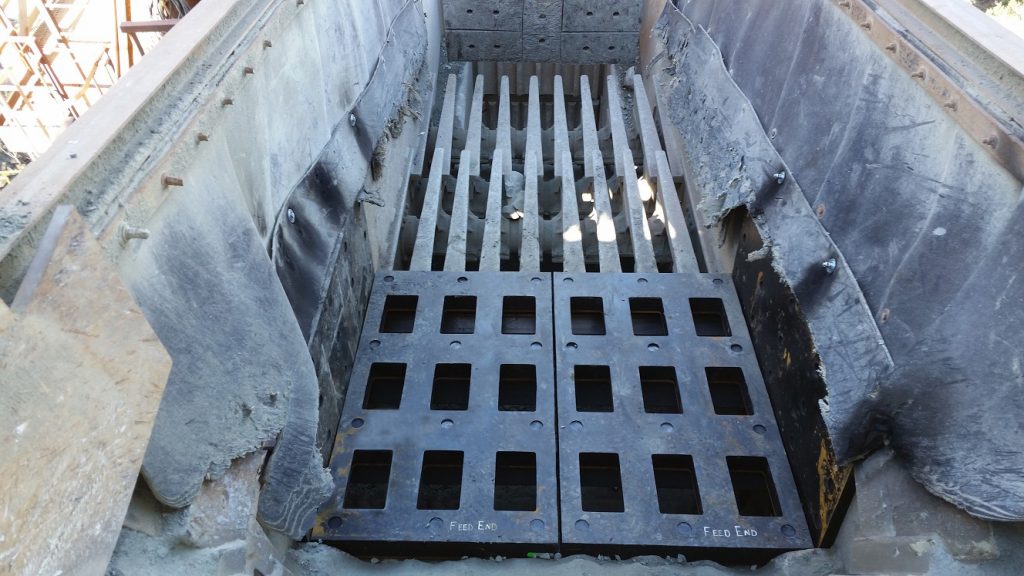
Un scalpage efficace est essentiel aux performances optimales des circuits de concassage primaire et secondaire. Pour augmenter l'efficacité du scalpage, l'exploitation Hanson a installé ARMADEX des sections de caoutchouc personnalisé à la deuxième étape - avec la troisième étape qui suivra bientôt.
Tout simplement, la capacité de production et la durée de vie de l'usure augmentent lorsque les fines sont éliminées de l'alimentation de la mâchoire primaire, lorsque les surépaisseurs sont alimentées à la mâchoire et lorsque les matériaux dont la taille est inférieure aux réglages du concasseur à mâchoires passent à travers les barres grizzly pour un broyage et un calibrage supplémentaires.
Toutefois, dans les applications extrêmement abrasives, à fort impact et à forte usure, il peut être difficile d'obtenir une efficacité optimale du scalpage.
Problème-Solution
Afin de réduire les coûts d'exploitation par tonne tout en répondant à la demande du marché en agrégats de haute qualité pour l'asphalte et le béton, la carrière Clayton de Lehigh Hanson en Californie a cherché à éliminer tous les goulets d'étranglement existants ou potentiels dans son usine. Desservant la région de la baie de San Francisco, la carrière Clayton est l'un des 200 sites de production de granulats et terminaux de distribution appartenant à Hanson, qui produit des granulats, de l'asphalte, du béton prêt à l'emploi et d'autres matériaux de construction dans toute l'Amérique du Nord.
"Notre fosse est une carrière de roche dure à forage et dynamitage qui a démarré en 1956", explique Marc McNeil, directeur de l'usine de la carrière Clayton. "Depuis la fin des années 1990, nous sommes progressivement passés de la production de roches de base à la pierre concassée et au sable manufacturé, et notre usine vieillissante nécessitait quelques mises à niveau, de l'alimentation initiale à la finition du produit."
Marc McNeil, directeur de l'usine de Lehigh Hansonde Clayton Quarry, supervise les mises à niveau actuelles de l'usine, de l'alimentation initiale à la finition du produit.
Les améliorations ont commencé par la résolution des problèmes de scalpage et de calibrage. L'application de scalpage de roches à fort impact de la carrière Clayton impliquait une usure extrême, ainsi que des coûts de maintenance et de main-d'œuvre excessifs pour remplacer et réparer les barres de grizzly usées.
En fin de compte, la carrière Clayton a choisi une solution de scalpage personnalisée conçue et fabriquée par Polydeck. ARMADEX est un produit de criblage en caoutchouc personnalisé qui a été appliqué en sections boulonnées à la première marche (5 pieds) de l'alimentateur vibrant à grizzly de l'usine.
"Depuis l'installation d'ARMADEX, nous avons considérablement réduit les temps d'arrêt pour la maintenance et les coûts d'usure, à tel point que nous avons fini par appliquer ARMADEX à la deuxième étape du grizzly, et que des plans d'installation sur la troisième étape sont actuellement en cours ", déclare McNeil.
Les défis du scalping à fort impact
La carrière de Clayton exploite une roche de diabase qui est transportée jusqu'à l'installation de concassage primaire et chargée dans une trémie de 150 tonnes.
Pour réduire les temps d'arrêt pour la maintenance et les coûts d'usure, un produit de criblage en caoutchouc personnalisé, ARMADEXa été appliqué en sections boulonnées à la première marche du grizzly.
Un alimentateur à plateau prend le matériau de 24 pouces de diamètre dans la trémie et l'achemine vers le grizzly vibrant. Le grizzly est fortement impacté, car le matériau tombe de 3 mètres avant de heurter les barres du grizzly. L'impact sur le support en acier génère un bruit considérable et provoque une usure excessive de l'extrémité d'alimentation du grizzly.
En outre, l'alimentation fine provenant de la fosse provoquait souvent le pontage de la première série de barres grizzly.
"Les barres sont boulonnées à une barre de support, mais avec le pontage et l'usure excessive, les barres commençaient à bouger et à s'ouvrir, laissant passer des roches plus grosses", explique McNeil. "Lorsque cette roche surdimensionnée passe dans le circuit secondaire, le concasseur à cône devient moins efficace."
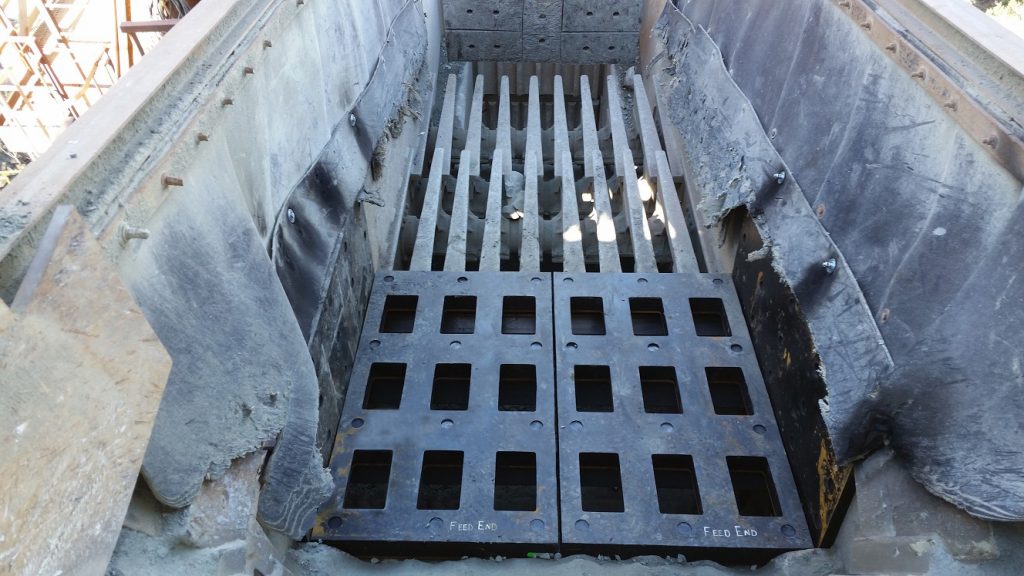
Plus important encore, les temps d'arrêt pour la maintenance et les coûts de main-d'œuvre supplémentaires entraient en jeu. Le déplacement des barres de grizzly a nécessité jusqu'à 20 heures de soudure par semaine pour les fixer en place, explique McNeil.
"Pour des raisons de sécurité, travailler sur un grizzly nécessite d'être harnaché", ajoute-t-il. "Donc, si un travailleur soude régulièrement des barres, cela devient assez difficile. Nous avons essayé de remplacer l'ensemble des barres et cela a été très coûteux. Il devait y avoir un autre moyen."
Solutions de scalping personnalisées
Dans toute son usine de finition, sur les cribles humides et secs, la carrière Clayton utilise des panneaux modulaires en polyuréthane synthétique et en caoutchouc Polydeck.
La carrière Clayton utilise des panneaux de criblage modulaires en polyuréthane synthétique et en caoutchouc dans toute son usine de finition, sur des cribles humides et secs.
"Nous avons obtenu de bons résultats avec leurs produits de tamisage et nous avons donc demandé aux ingénieurs d'application de Polydeck d'évaluer notre circuit de scalpage pour voir ce qui pouvait être fait", explique M. McNeil. "Ils ont proposé d'utiliser ARMADEXNous avons décidé de l'essayer sur la première marche du grizzly. Nous avons décidé de l'essayer sur la première marche du grizzly - et nous avons constaté des avantages immédiats en termes de réduction des temps d'arrêt pour la maintenance et des coûts d'usure."
Comme le souligne Peter Babinski de Polydeck, les producteurs d'agrégats veulent un temps de fonctionnement maximal, une maintenance minimale, une durée de vie accrue et une réduction du bruit, en particulier dans les applications d'alimentation par grizzly abrasif. Les producteurs se tournent souvent vers les solutions de médias synthétiques pour obtenir ces avantages, dit-il.
Comme l'explique M. Babinski, le support d'écran en caoutchouc ARMADEX utilise la technologie de moulage par injection à haute pression, une méthode de fabrication Polydeck qui produit une pression dix fois supérieure à celle normalement utilisée pour produire du caoutchouc moulé par compression.
"La combinaison de cette technologie avec notre composé de caoutchouc gommeux de première qualité et notre support de plaque d'acier HSLA produit une force sans précédent dans un produit de média qui offre une durée de vie beaucoup plus longue et des coûts inférieurs par tonne ", déclare M. Babinski, qui sert Polydeck en tant que directeur du territoire des agrégats de la côte ouest et des États des montagnes.
"Avec les barres de grizzly, les exploitations ne peuvent pas les ajuster à moins de les changer complètement ou de les souder pour modifier les ouvertures", explique Babinski. "Les sections boulonnées ARMADEX nous donnent la flexibilité d'accéder à des ouvertures plus petites ou plus grandes pour affiner les performances dans une application donnée."
Pour installer les sections ARMADEX sur le grizzly d'alimentation de la carrière Clayton, Polydeck a conçu un cadre personnalisé qui se boulonne aux panneaux latéraux du grizzly. Les sections ARMADEX sont facilement boulonnées sur ce cadre.
"Le remplacement s'est fait en un tournemain, avec très peu de temps d'arrêt, grâce à l'attention portée par Polydeck aux détails de la personnalisation de notre application ", explique M. McNeil.
Efficacité du Scalping et du Sizing
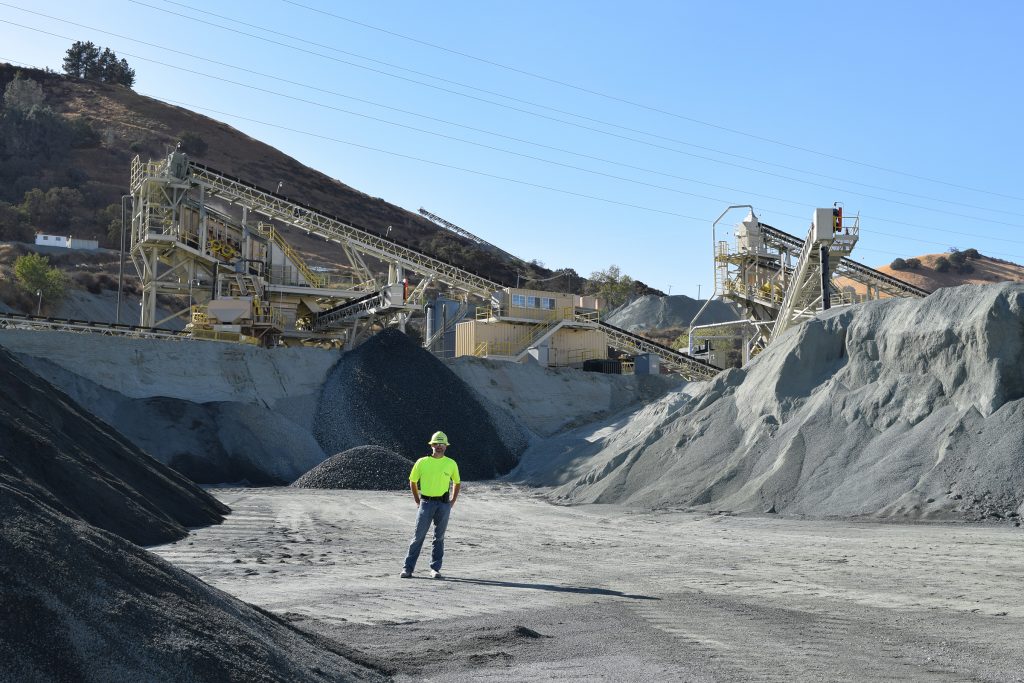
Selon McNeil, l'opération a considérablement amélioré l'efficacité du scalpage et du calibrage au jour le jour en utilisant ARMADEX sections de médias. En empêchant le matériau surdimensionné de passer dans le concasseur à cône, l'opération a permis d'améliorer les performances de concassage tout en réduisant les temps d'arrêt.
"Nous avons considérablement réduit les coûts de maintenance, car nous n'avons pas eu à remplacer une section ARMADEX depuis leur installation, et elles ne nécessitent pas de soudure hebdomadaire ", déclare M. McNeil, ajoutant que les sections de médias sur la première étape du grizzly ont traité un débit de matériaux de près de 3 millions de tonnes sur trois saisons de production.
La carrière de Clayton continue de travailler avec Polydeck afin d'affiner les performances. Le circuit de scalpage utilisera des ouvertures rondes dans les sections ARMADEX utilisées sur la troisième étape de l'alimentateur à grizzly, augmentant ainsi le débit des roches angulaires qui peuvent se coincer dans les ouvertures carrées ou rectangulaires.
En ajustant les circuits de scalpage en haut de la chaîne, ceux qui suivent voient leur usure diminuer, leurs capacités de production s'accroître et leurs produits se vendre plus facilement jusqu'aux stocks.
Écrit par Carol Wasson, rédactrice indépendante expérimentée dans le secteur des agrégats et des équipements de construction.
LafargeHolcimLafargeHolcim, un leader mondial des matériaux et solutions de construction, est un producteur actif dans les segments Ciment, Granulats, Béton prêt à l'emploi et Solutions & Produits des industries qu'il dessert. En tant que société dont l'activité est centrée sur l'utilisation de matériaux naturels, LafargeHolcim est parfaitement consciente de ses responsabilités en matière de durabilité. Récemment, l'équipe dirigeante de l'entreprise a clairement indiqué que le développement durable était un élément clé de sa stratégie commerciale et qu'elle l'évaluait activement sur chaque site dans le cadre de ses rapports annuels. La prise en compte de l'impact de chacune de leurs opérations et de chacun de leurs sites sur l'environnement et la durabilité est essentielle à leur réussite en tant qu'entreprise qui dépend de matériaux naturels.
Woodstock de LafargeHolcimDans le cadre de l'exploitation de sa carrière, la ville d'Ottawa, en Ontario, au Canada, a connu une percée importante en matière de durabilité et de débit ultime de matériaux utilisables grâce à la technologie de pointe de Polydeck. buse de pulvérisation technologie. La carrière de Woodstock était auparavant fortement impliquée dans l'extraction et le traitement du gisement de calcaire, un matériau de construction essentiel. L'exploitation se concentrait historiquement sur le dynamitage, l'extraction, le concassage et le criblage du calcaire. En tant qu'usine d'alimentation d'une cimenterie voisine, la viabilité de l'exploitation de la carrière était évidente. Cependant, lorsque le marché du calcaire a changé, l'exploitation a dû s'adapter aux nouvelles exigences du marché.
L'évolution du marché a entraîné la fourniture d'une plus grande quantité de pierres pour l'asphalte et le béton. En se concentrant sur ces matériaux, l'exploitation a commencé à produire des fines. En fait, l'équipe de la carrière de Woodstock a remarqué qu'elle produisait des montagnes de fines. La culture de l'entreprise ayant évolué pour prendre en compte l'impact de chaque opération et innover en matière de durabilité, l'ampoule a commencé à s'allumer à Woodstock : les fines produites pouvaient être transformées en un matériau propriétaire et utilisable. Si l'objectif final semblait clair, il fallait encore faire preuve d'adaptation et de créativité. C'est là que l'équipe de Polydeck est intervenue pour aider l'usine à définir sa nouvelle approche.
LafargeHolcim savait que les fines retraitées seraient hautement commercialisables, et ils avaient raison. Il est devenu évident que les buses de pulvérisation de Polydeck, conçues pour supporter un lavage intensif, étaient la réponse à l'adaptation des ponts pour créer un produit commercialisable.
Si une buse de pulvérisation semble être un produit simple, le diable se cache vraiment dans les détails. Lorsque la carrière a commencé à chercher une solution de lavage, elle savait qu'elle avait besoin du produit le plus efficace et le plus durable du marché. Idéalement, les buses de pulvérisation devraient avoir la capacité de fournir de l'eau à la bonne pression et à la bonne géométrie pour produire un effet de lavage résultant en une séparation des matériaux et un débit appropriés. C'est exactement ce qu'ont fait les buses de pulvérisation Polydeck, installées sur la machine horizontale Simplicity 8x20 Triple Deck de LafargeHolcim. Lorsqu'une buse de pulvérisation fonctionne correctement, les matériaux indésirables dimensionnés et répartis sont libérés et isolés en tant que matériaux utilisables.
La carrière de Woodstock a commencé à tester un processus de lavage pour extraire les fines à l'aide d'une toile métallique, qui est un produit courant dans une opération de lavage. Cependant, l'entretien et le temps de manipulation du tissu métallique se sont rapidement avérés très inefficaces pour l'exploitation. Le temps passé à changer la toile métallique n'était pas consacré à la production de matériaux vendables.
Après avoir réalisé que le métal tissé était une solution inefficace, LafargeHolcim s'est de nouveau tourné vers Polydeck et a décidé de concevoir une usine pour produire ce matériau exclusif. Polydeck a équipé les trois ponts de LafargeHolcim avec des toiles métalliques. médias synthétiques ainsi que des buses de pulvérisation. Les résultats ont été stupéfiants. S'adaptant à une situation présentant un défi de dégagement extrêmement étroit, les buses de pulvérisation de Polydeck ont non seulement été adaptées, mais elles ont également exécuté le travail avec certitude. Les matériaux qui étaient auparavant des déchets étaient maintenant séparés grâce aux résultats de lavage efficaces produits par la combinaison des buses de pulvérisation Polydeck et du média de tamisage. Les buses de pulvérisation Polydeck sont dotées d'une fonction d'autonettoyage qui a permis d'éliminer un nombre important d'heures de travail, et leur facilité de remplacement et d'entretien a permis à la carrière de Woodstock de ne pas connaître de temps d'arrêt important si une pièce ou une buse devait être ajustée, remplacée ou nettoyée.
LafargeHolcim a appris de première main comment l'adaptation de son opération de lavage avec les buses de pulvérisation Polydeck dans son usine de Woodstock a augmenté son efficacité, son débit et sa durabilité. Un ancien sous-produit aux applications très limitées est transformé en un produit hautement commercialisable dans le respect de spécifications strictes. La maintenance est réduite et simplifiée. Le "money-deck", comme beaucoup l'appellent, est libre de produire des matériaux qui génèrent des bénéfices pour l'entreprise. Lorsque les résultats et la durabilité sont importants, les buses de pulvérisation autonettoyantes, robustes et à haut rendement de Polydeck n'ont pas leur pareil.
Sable et gravier de Vicdom sait très bien que la production et le lavage de granulats sont des opérations difficiles pour les équipements. Cette entreprise familiale de troisième génération produit des pierres, du sable et du gravier depuis plus de 40 ans à Uxbridge, dans l'Ontario (Canada), à 30 minutes de route au nord-est de Toronto.
La direction de Vicdom sait également que les temps d'arrêt inutiles ont un coût élevé. Jusqu'à récemment, l'entreprise rencontrait des problèmes d'usure périodiques sur les tamis métalliques de 5' x 7' de son système de tamisage à deux étages de 5' x 14'. Dillon écrans de lavage. Les tamis étaient utilisés pour produire +5/8" au-dessus du pont supérieur, 9/16"-1/4" au-dessus du pont inférieur, et 1/4" de copeaux à travers le pont inférieur. Bien que les tamis aient eu une durée de vie décente et aient satisfait aux exigences de production lorsqu'ils étaient en service, une fois endommagés, ils ont dû être complètement remplacés.
"Il suffit d'un trou dans la zone d'alimentation pour devoir changer tout le crible, même si 75 % du crible est encore en bon état", explique-t-il. Victor Giordanodirecteur adjoint chez Vicdom, et petit-fils de Vic Giordano, cofondateur de Vicdom. "Un écran $500 était devenu un déchet."
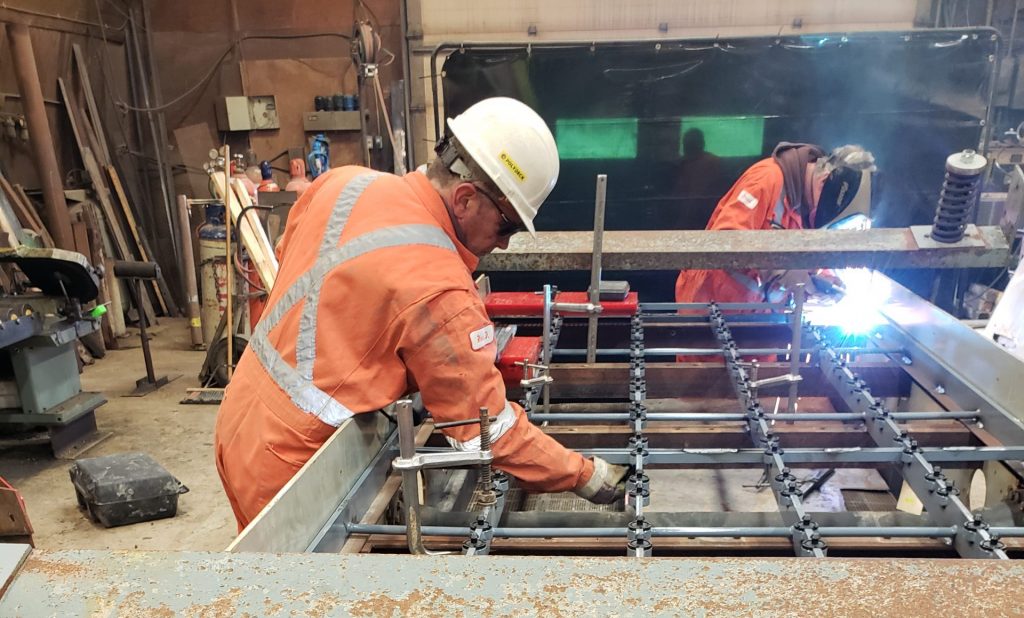
Le coût le plus important découlant du remplacement des écrans était le temps d'arrêt lié au remplacement des supports d'écran de 5' x 7', qui, selon M. Giordano, coûtait à son entreprise entre une et trois heures de temps d'arrêt chaque fois qu'il fallait les remplacer. Ainsi, lorsque Alex CaruanaLorsque M. Giordano, directeur territorial de Polydeck pour le centre du Canada et les provinces de l'Atlantique, a expliqué que l'entreprise pouvait économiser de l'argent et réduire les temps d'arrêt de ses activités en modernisant ses écrans de lavage avec un système modulaire à encliquetage, il a voulu en savoir plus.
"Alex a apporté un diagramme et a bien expliqué ce que nous avions avant avec le treillis métallique et ce que nous pourrions avoir avec Polydeck", dit Giordano. "Le plus gros reproche fait à caoutchouc et polyuréthane est qu'il n'a pas assez de surface ouverte comme le grillage, mais il a montré qu'on ne perdait pas de surface ouverte."
Caruana a montré à Giordano qu'il ne perdrait aucune zone ouverte en utilisant une méthode très simple, mais efficace.
"Ce que je fais généralement pour une usine lorsqu'elle envisage un ou plusieurs ponts est très simple. Je verrouille, je saute sur l'écran ou je prends une photo, et je compte simplement les ouvertures. Je connais la taille des ouvertures, parce que je les ai mesurées, et cela me permet également de tenir compte de toutes les obstructions telles que les barres de poussée, les rails de serrage latéraux, les déviateurs, les boulons et autres choses de ce genre. Cela me permet de montrer au client qu'avec sa toile métallique actuelle, il dispose d'une surface ouverte de 'X', quelle que soit la valeur de 'X'", explique Caruana. "Ensuite, je suis en mesure de leur montrer que dans leur application, en utilisant notre média, leur surface ouverte serait maintenant de "X+", et c'est leur nouveau numéro de surface ouverte."
Dans de nombreux cas, cette comparaison est une véritable révélation pour les producteurs.
"Même avec du tissu métallique, ils n'avaient peut-être pas tous les espace ouvert qu'ils pensaient avoir", explique Caruana. "Imaginez un morceau de grillage devant vous. Il n'est pas obstrué, et sa surface ouverte cataloguée, ou valeur comptable, pourrait être de 65%. Elle semble très attrayante. Mais lorsque vous le mettez en place, il y a des pièces de machine en dessous. Donc, vous n'avez pas vraiment 65%, mais plutôt 48%. Les supports synthétiques ne sont pas les mêmes. Lorsque le média synthétique donne une surface ouverte, c'est le chiffre brut et net. Une fois installé, il a toujours cette surface ouverte. Si quelqu'un vous dit que vous avez 48%, alors c'est le chiffre en place. Donc, si je fais cette comparaison pour des gens comme Victor chez Vicdom, ils ont cette information à leur disposition et ils peuvent faire un choix plus éclairé."
Vicdom a décidé de remplacer l'un de ses ponts de lavage par un système modulaire à enclenchement utilisant des panneaux de polyuréthane Polydeck de 1 pi x 1 pi avec des ouvertures carrées de 1/2 po sur le pont supérieur et des ouvertures d'environ 1/4 po sur le pont inférieur. Giordano a été impressionné par les résultats.
"Cette année, nous avons changé deux panneaux, au total, sur la conversion", dit-il. "Nous aurions normalement changé cinq ou six écrans entiers. Au lieu de cela, nous avons changé deux panneaux qui coûtaient $90 canadiens chacun pour $180 en un an. Les rendements sont bons, la capacité est bonne et les temps d'arrêt sont étonnants".
Vicdom a maintenant équipé les quatre ponts de ses deux tamis de lavage avec le système modulaire d'encastrement de Polydeck en utilisant des panneaux de polyuréthane de 1' x 1'. Le deuxième écran de lavage a des ouvertures de 5/8" sur le pont supérieur et des ouvertures d'environ 1/4" sur le pont inférieur.
La réduction des temps d'arrêt liés au changement de support d'écran n'est pas la seule raison pour laquelle Vicdom apprécie de travailler avec Polydeck. M. Giordano affirme que le niveau de professionnalisme de M. Caruana a été un argument de vente important, car il est toujours disponible pour aider à résoudre les problèmes qui surviennent sur le site.
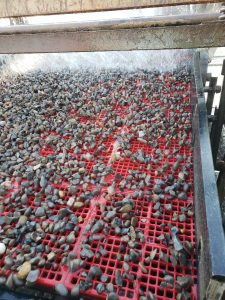
La société a eu un problème de traitement l'année dernière avec la première conversion, et a donc appelé Caruana pour en discuter.
Il m'a demandé : "Vous êtes sûr que vos excentriques vont vers le bas ?". se souvient Giordano.
Giordano a donc vérifié auprès de son équipe de maintenance et il s'est avéré qu'ils avaient effectué des travaux ce jour-là et qu'ils avaient accidentellement recâblé le moteur à l'envers sur l'écran, ce qui faisait que les excentriques tournaient vers le haut.
"Nous avons réparé le câblage, retiré la pierre et le système fonctionnait à nouveau. Grâce à ses connaissances, nous avons pu résoudre ce problème immédiatement", déclare Giordano, ajoutant qu'il apprécie énormément les connaissances techniques que Caruana apporte sur le chantier. "Je ne vois pas un vendeur. Je vois un gars qui a beaucoup d'expérience de la fosse maintenant dans la vente, et cela aide."
Vous envisagez une conversion ?
Polydeck dispose d'une équipe de professionnels et de plus de 40 ans d'expérience pour vous aider à optimiser les performances de votre criblage tout en minimisant les temps d'arrêt.
"Vous perdez de la surface ouverte lorsque vous passez de la toile métallique aux supports synthétiques."
Beaucoup d'exploitants d'installations pensent encore que si l'on passe du tissu métallique à des tamis modulaires en matière synthétique, il faut volonté perdre de la surface ouverte sur votre pont. Cependant, de plus en plus de producteurs essaient les médias synthétiques et constatent qu'ils bénéficient d'un débit et d'un temps de fonctionnement accrus, d'une surface ouverte maximale et d'une durée de vie prolongée, ce qui prouve que cette idée n'est qu'un mythe.
Cas concret
Winter Brothers Material Company est une entreprise familiale de sable et de gravier qui répond aux besoins en agrégats de la région de St. Louis depuis 70 ans. Les deux frères fondateurs, George "Pete" Winter et Robert A. Winter, ont organisé des excursions fluviales dans la région dans les années 1930. Après avoir servi pendant la Seconde Guerre mondiale, ils sont revenus dans la région et ont créé l'entreprise en 1946.
Situé sur la rivière Meramec, un affluent du Mississippi, Winter Brothers exploite un gisement alluvial dont la forme, l'uniformité et la pureté des particules sont uniques. "Notre région a la chance de disposer d'un gravier de qualité constante et d'un sable sans lignite déposés par la nature dans cette vallée fluviale", explique Ryan Winter, membre de l'équipe de direction de Winter Brothers.
Plus de 70 % des produits de l'entreprise sont utilisés dans l'industrie du béton prêt à l'emploi et donnent de bons résultats dans une variété de mélanges de ciment Portland. Les produits sont également destinés aux secteurs de la toiture, de la maçonnerie, de l'asphalte, de l'aménagement paysager, des fosses septiques et des puits d'extraction.
Le défi
Dans l'usine de Hagemann, les principaux circuits de criblage produisent six tailles différentes d'agrégats grossiers ainsi que deux tailles de produits de sable. "Depuis l'ouverture de l'usine, nous avons toujours utilisé des toiles métalliques sur tous les étages de chaque circuit de criblage", explique M. Winter, qui admet que son équipe de direction a longtemps résisté à l'utilisation de médias synthétiques en raison de préoccupations concernant la perte de surface ouverte et la diminution de la capacité de production.
Ce qu'ils n'avaient pas pris en compte, c'était la quantité de surface ouverte qu'ils perdaient en raison du chevillage et de l'aveuglement des matériaux. Les panneaux en toile métallique qu'ils utilisaient étaient annoncés comme ayant une surface ouverte "maximale", mais comme le raconte Winter, "ils s'aveuglaient au cours des deux premières semaines et nous perdions un pourcentage important de notre production".
D'autres problèmes se sont posés en raison des temps d'arrêt dus à la maintenance des tamis pendant les périodes de pointe, lorsque l'usine augmente sa production. Chacun de leurs étages utilisait cinq feuilles de toile métallique de 1,5 m sur 1,5 m, et M. Winter se souvient que cette question était cruciale pour lui.
"Lorsque l'un de ces cribles explosait, nous devions tout arrêter, retirer des travailleurs d'autres tâches, faire venir une grue, remplacer les cribles - tout cela prenait plusieurs heures de la journée de production à chaque fois que cela se produisait". En outre, chaque fois qu'un crible en toile métallique se trouait soudainement, des matériaux surdimensionnés tombaient à travers et contaminaient les stocks de produits.
C'est pourquoi M. Winter, ainsi que le directeur de l'usine Steve Klahs - un vétéran de l'industrie depuis 30 ans - ont commencé à examiner de près les médias synthétiques, car ils voulaient mieux comprendre les avantages et les inconvénients du changement. Heureusement, ils ont appelé Polydeck pour obtenir des conseils.
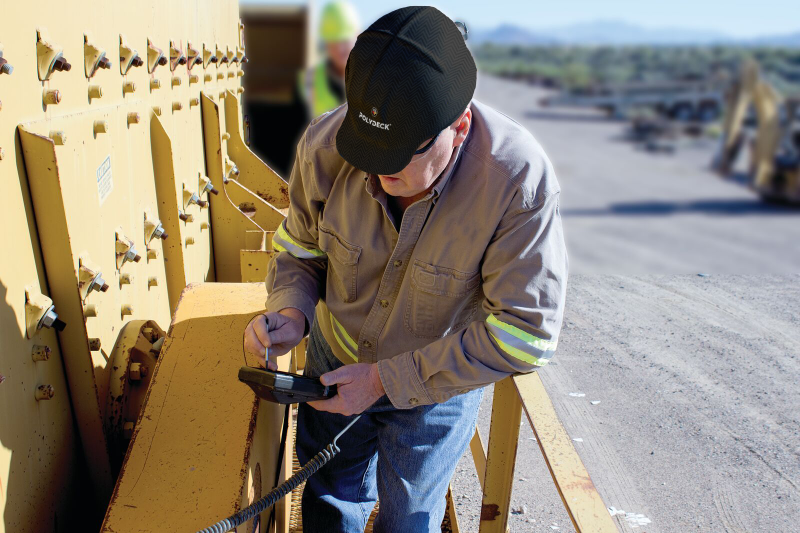
L'évaluation
Après avoir discuté avec plusieurs fabricants de médias synthétiques, Winter dit qu'il a choisi Polydeck en raison de notre expertise et de notre professionnalisme, et en raison de la relation solide qu'il entretient avec son revendeur local de Polydeck, CT Fike Co.
"Dan Fike a été très proactif", explique M. Winter. "Il a fait venir des membres clés de l'équipe Polydeck pour examiner de près nos processus afin qu'ils puissent spécifier les types de panneaux adaptés à nos applications et à nos gradations."
Joe TeagueLe vice-président des ventes, qui était à l'époque directeur régional des ventes de Polydeck, a travaillé en étroite collaboration avec l'équipe de direction de Winter Brothers. Il leur a démontré que leur préoccupation concernant la perte de surface ouverte réside dans la manière dont la "surface ouverte" est généralement définie et calculée.
"Les pourcentages de surface ouverte publiés entraînent des erreurs de calcul dans la spécification de la surface de criblage et de la taille du crible vibrant requises pour une application donnée", explique M. Teague. "De nombreux catalogues de toiles métalliques indiquent des pourcentages de surface ouverte qui sont pris en compte dans le calcul de la surface de criblage. tous les ouvertures d'une section de l'écran. Cependant, lors de l'installation, une partie de ces ouvertures est obstruée par des barres d'abattage, des couronnes en caoutchouc, des rails de serrage et des dispositifs de retenue centraux. Cela signifie que la surface ouverte est nettement plus petite, ce qui entraîne une erreur de calcul pouvant aller jusqu'à 40 %, voire plus".
Dans le cas de nombreuses marques de supports synthétiques, la surface ouverte est souvent calculée en ignorant simplement la bordure. "Le panneau traditionnel comporte une large bordure ou une zone "morte" autour du périmètre qui n'est souvent pas prise en compte", explique M. Teague, "ce qui signifie que le pourcentage de surface ouverte est surestimé pour ces produits".
Teague a montré à la direction de Winter Brothers que lorsque les bureaux d'études et les utilisateurs finaux utilisent ces calculs inexacts de la surface ouverte dans leur logiciel d'analyse des flux de l'usine, celle-ci peut être conçue avec des cribles vibrants sous-dimensionnés ou surdimensionnés.
Le conseil de Teague a été une révélation : La surface ouverte doit être calculée en prenant le nombre total d'ouvertures dans le panneau de l'écran et en déterminant le pourcentage de la surface ouverte. réel des trous ouverts par rapport à la complet surface du panneau lui-même. Il a suggéré que Winter Brothers adopte une approche très élémentaire pour comparer la surface ouverte entre deux fabricants en comptant simplement le nombre de trous sur chaque panneau d'écran.
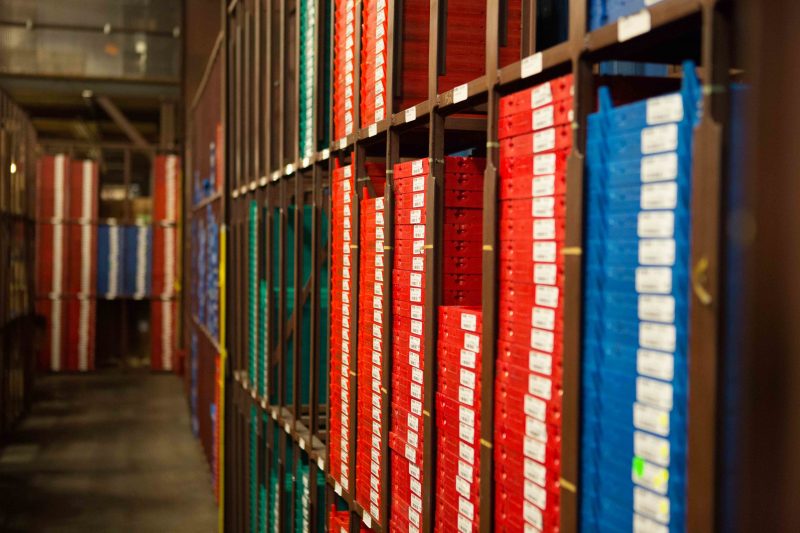
La solution
L'objectif était de s'assurer que le circuit suivait le rythme du concassage. L'approche de Polydeck a donc commencé par faire correspondre correctement le média aux paramètres du crible vibrant, en sélectionnant parmi notre bibliothèque de plus de 1 500 options de conception de panneaux de criblage.
Nous avons passé en revue tous les mélanges de produits afin d'identifier les incohérences potentielles de gradation et les goulets d'étranglement de l'usine, et de procéder à des ajustements en amont. Après avoir capturé les statistiques de traitement critiques, nous avons exécuté des scénarios de simulation afin d'optimiser les spécifications des médias pour les applications de Winter Brothers et de déterminer comment toute modification des variables dans les opérations de criblage affecterait l'efficacité globale.
Selon Winter, "Polydeck garanti Nous nous sommes assurés que la configuration de leurs panneaux nous permettrait de répondre aux spécifications requises. Si ce n'était pas le cas, ils procéderaient aux modifications nécessaires à leur coût. Cela nous a donné beaucoup de confiance lorsque nous avons changé tant de jeux de cartes pour des jeux d'argent. médias synthétiques."
A l'issue de l'évaluation, Winter Brothers a pris la décision d'installer le système Polydeck®. panneaux modulaires en polyuréthane.
Les résultats parlent d'eux-mêmes
Depuis l'installation du média synthétique, Winter Brothers a toujours respecté les spécifications de l'industrie.
"Depuis que nous avons changé, nous n'avons eu à remplacer que quelques panneaux sur les zones d'impact. Nous sommes très satisfaits de l'augmentation de la durée de vie du polyuréthane, car lorsque nous utilisions des toiles métalliques sur ces ponts, nous remplacions un ou deux écrans par semaine", explique M. Klahs.
Alors que M. Klahs pensait que l'abandon des cribles à fils entraverait la production, il reconnaît aujourd'hui que l'utilisation de médias synthétiques permet à l'entreprise d'économiser du temps et de l'argent. "Nous constatons une augmentation incroyable de la production - presque un doublement - en particulier pour le sable fin", déclare-t-il. "En outre, la surface ouverte des panneaux en polyuréthane nous permet d'obtenir un excellent débit. Nous sommes particulièrement impressionnés par la surface ouverte que nous obtenons pour le traitement du sable de maçonnerie.
Pour Ryan Winter, la durabilité des panneaux en polyuréthane et les économies de main-d'œuvre qui en résultent constituent le principal argument de vente. "Notre matériau est très dur", explique-t-il. "Alors que le calcaire typique a une dureté de 3 à 4 sur l'échelle MOHS, notre sable et notre gravier ont une dureté de 7 à 8. Ainsi, si le débit et la surface ouverte sont importants, la durabilité l'est tout autant".
"Nous sommes très satisfaits de la durée de vie de ces panneaux, et l'équipe de maintenance peut détecter tout problème d'usure avant qu'il ne devienne un problème de temps d'arrêt ou de contamination. Si les échantillonnages de contrôle de qualité sont légèrement décalés, l'équipe de maintenance sait qu'il faut vérifier l'usure. S'il faut remplacer un panneau, il suffit de quelques minutes à une personne pour retirer l'écran usé et en mettre un nouveau.
"Parfois, les entreprises s'en tiennent aux mêmes vieilles méthodes parce qu'elles ont toujours procédé ainsi", admet M. Winter. "C'est la raison pour laquelle nous sommes restés si longtemps avec le tissu métallique. Mais nous avons finalement opté pour les supports synthétiques de Polydeck et nous sommes heureux de l'avoir fait."
Mythe... démenti !
La nouvelle solution de tamisage de Polydeck maximise le débit et le mélange de produits..
Aggregate Industries (AIUS) est devenue l'une des plus grandes entreprises de matériaux de construction et de bâtiment aux États-Unis en mettant l'accent sur la durabilité stratégique, la gestion de l'environnement et les relations à long terme avec les clients. La carrière Morrison de la société, une exploitation de granit de 3 millions de tonnes par an située dans le comté de Jefferson, dans le Colorado, illustre parfaitement sa mission.
Le comté de Jefferson est l'un des trois comtés de la région de Denver, qui compte six comtés et fait partie de la région centrale ouest de l'AIUS, qui offre des sources disponibles de pierre concassée. Étant donné que de nombreuses ressources potentielles en granulats dans la région de Denver ne sont pas accessibles à l'extraction, la carrière de Morrison joue un rôle essentiel pour répondre à la demande de la région en matériaux granulats de haute qualité.
Trulane Vanatta, directeur de l'usine Morrison, exploite une usine "à guichet fermé", ce qui signifie que tout ce qui est traité un jour donné est vendu le lendemain. Pour lui, explique-t-il sans ambages, " [ ?Le débit est essentiel."
Par conséquent, l'installation se concentre constamment sur l'amélioration de l'efficacité du traitement et de la capacité de production. Pour éliminer les goulots d'étranglement dans les circuits de criblage, l'équipe de gestion de Morrison a fait appel aux experts en ingénierie de Polydeck.
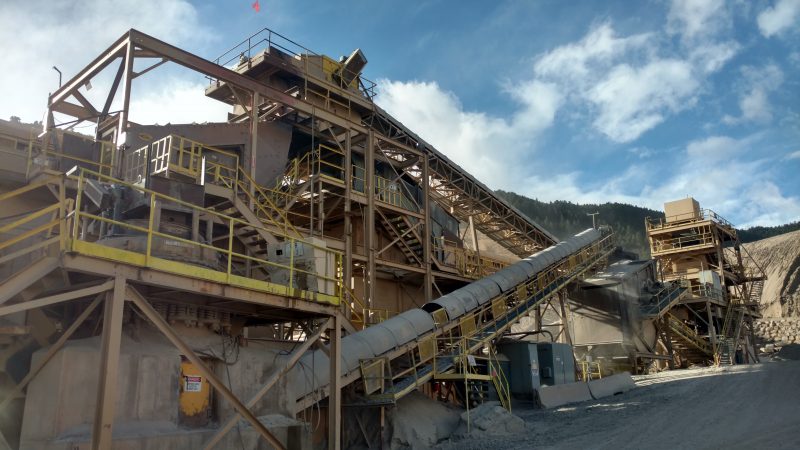
Réduire les charges de recirculation et les amendes
L'équipe de Vanatta a identifié un problème dans le circuit tertiaire de l'usine à neuf cribles. Leurs échantillons de bande indiquaient une profondeur de lit élevée sur les ponts intermédiaires des trois cribles du circuit. Chacun des cribles à trois étages de 8 pieds sur 20 pieds est essentiel à la production du matériau #57/#67 (1 pouce) de Morrison.
"C'est notre gagne-pain, et nous devons maximiser son volume de production.dit Vanatta.
Son équipe a trouvé un report " troublant " de 51%, un goulot d'étranglement qui provoquait des charges de recirculation et produisait des fines excessives - un problème de production courant. "La première chose à laquelle nous avons pensé a été de remplacer les ponts intermédiaires de deux des cribles tertiaires par du tissu métallique pour obtenir une plus grande surface ouverte.", se souvient Vanatta.
Il s'avère cependant que le directeur régional de Polydeck, Sam DurnavichIl y a plus de dix ans, Sam était le directeur adjoint de l'usine de la carrière Morrison avant de se joindre à l'organisation Polydeck. Grâce à sa connaissance de l'exploitation, Sam a consulté la direction de Morrison et a travaillé en étroite collaboration avec l'équipe d'ingénieurs de Polydeck afin de créer une solution média qui permettrait de relever plus efficacement le défi de l'entraînement.
Après une analyse approfondie du fonctionnement de Morrison, l'équipe de production de Polydeck a conçu et installé un tout nouveau produit : DMAX™ un système de tamis synthétique à très grande surface ouverte qui augmente considérablement le débit et permet à la carrière d'accroître la production de ses produits de plus grande valeur.
Les nouveaux panneaux de criblage DMAX de Polydeck sont destinés à être utilisés lorsque la surface ouverte et le débit sont les considérations les plus importantes. Il s'agit d'une solution modulaire de panneaux de criblage synthétiques dont la surface ouverte est égale ou même supérieure à celle des toiles métalliques, tout en offrant une plus grande durée de vie et une installation plus facile. Le système de panneaux de criblage DMAX peut également être formulé avec du caoutchouc ou du polyuréthane, selon l'application.
Dépasser les objectifs de production
Depuis l'installation du premier DMAX Grâce à l'installation de panneaux de criblage sur deux des étages intermédiaires en octobre 2015, l'entreprise a atteint et souvent dépassé ses objectifs de production. Ils ont également atteint une efficacité de criblage bien plus grande, selon Vanatta - près de 54% de surface ouverte sur leurs ponts intermédiaires, par rapport aux 42% de surface ouverte fournis par leur pont de criblage précédent. Il s'agit d'une augmentation spectaculaire de 28,5% de la surface ouverte. Morrison a ensuite installé des panneaux DMAX sur un troisième pont intermédiaire à la mi-2016.
"Pour nous", dit Vanatta, "L'augmentation de la surface ouverte s'est traduite par une augmentation de 11% de la production de roche rentable de 1 pouce, et a réduit les fines de près de 1%. Le seul inconvénient de la surface ouverte est que les panneaux s'usent un peu plus vite, mais cela n'a pas d'importance puisque le bénéfice de l'augmentation du tonnage rembourse plus de dix fois l'investissement dans le média de criblage.."
La carrière de Morrison utilise également les panneaux de criblage modulaires Rubberdex® de Polydeck sur les étages supérieurs et inférieurs de ses cribles tertiaires de 8 pieds par 20 pieds.
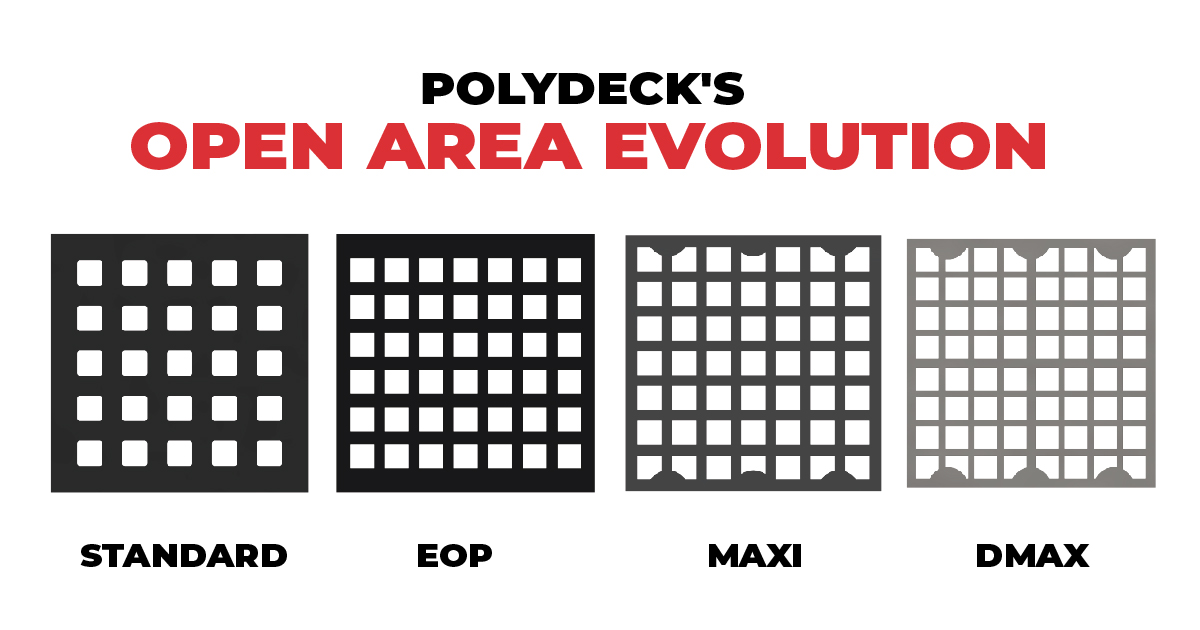
Expertise en ingénierie
Explique Sam Durnavich de Polydeck, "Nous avons fabriqué les panneaux DMax avec des ponts deux fois moins larges que ceux de notre maxi panneau standard, mais beaucoup plus profonds. C'est important, car la réduction de la largeur du pont entre les ouvertures permet d'augmenter le nombre d'ouvertures dans la surface du panneau, ce qui se traduit par un meilleur passage du produit.."
"Le fait que les panneaux DMax soient conçus pour s'adapter aux systèmes de limons Polydeck PipeTop II existants contribue à accroître la surface ouverte.", poursuit M. Durnavich. "Ce système d'armature comporte des rails de fixation uniques d'un demi-pouce de large au lieu des styles de montage des systèmes d'armature conventionnels avec jusqu'à 3 pouces d'espace mort où les amendes s'accumulent. En outre, nos capacités d'outillage en interne nous permettent de proposer beaucoup plus d'options dans ces systèmes d'armature, qu'il s'agisse des options de fixation, des options de matériaux ou des styles et types de longerons.."
"L'augmentation de la surface ouverte fait s'accompagnent d'une réduction de la durée de vie des panneaux d'écran", admet Durnavich, "Mais si l'on compare les panneaux de criblage à usage standard, les panneaux DMax ont une durée de vie inférieure de seulement 20-25%, ce qui dépasse toujours celle des toiles métalliques.."
"Notre utilisation du moulage par injection est un facteur important dans la capacité de créer des panneaux synthétiques à surface ouverte extrême.ajoute M. Durnavich. "Le moulage par injection permet de s'assurer que chaque panneau d'écran a des tailles et des formes d'ouverture précises, et qu'il est entièrement durci.."
"Nos résultats réels sur le terrain dans plusieurs applications ont démontré des augmentations de production allant jusqu'à 50%, et des augmentations de l'efficacité du filtrage de plus de 25%.dit Durnavich avec un sourire.
Polydeck continue d'élargir la gamme des ouvertures disponibles dans la série DMax, avec des ouvertures carrées de 12,5 mm à 32 mm, ainsi que des ouvertures fendues de 3x20 mm à 25x74 mm.
On le dit souvent : S'il y a un goulot d'étranglement dans une usine, c'est probablement au niveau du circuit de criblage. Le débit est primordial pour la carrière Morrison, et l'augmentation continue de l'efficacité du criblage est essentielle à sa rentabilité et à la qualité de ses produits. En travaillant ensemble, la carrière Morrison et Polydeck ont résolu un problème immédiat et créé une solution à long terme.
KWIKDECK est un moyen simple et rentable d'essayer les médias modulaires.
Supports d'écran est un élément essentiel pour les industries des agrégats, de l'énergie, de l'industrie et de l'exploitation minière. Pendant des décennies, les toiles métalliques ont été le support privilégié de l'industrie, mais elles sont encombrantes à installer et ne sont pas aussi polyvalentes que les supports modulaires. Si vous utilisez des toiles métalliques, vous avez probablement l'habitude de les changer toutes les quelques semaines, une tâche qui prend du temps et qui est parfois dangereuse.
Et si vous ne deviez remplacer votre support d'écran que deux fois par an ?
Polydeck KWIKDECK offre une meilleure solution : Une conversion de cadre qui vous permet d'essayer des supports d'écran synthétiques pratiquement sans risque, avec des coûts d'installation minimes et une installation facile.
KWIKDECK vous aide à réduire vos coûts d'exploitation, à diminuer les temps d'arrêt tout en améliorant la sécurité, et à maintenir votre équipement à un niveau de performance optimal.
Qu'est-ce qui fait de KWIKDECK une solution idéale ?
- L'installation est simple - KWIKDECK prend environ 45 minutes pour changer une section de 1,5 m sur 1,5 m. Il utilise les rails de serrage latéraux existants et ne nécessite pas de modifier le cadre du bureau existant. Il réutilise les rails latéraux existants et ne nécessite pas de modifier le cadre du bureau.
- Il est adaptable - KWIKDECK fonctionne avec des plateaux couronnés et peut être modifié pour s'adapter aux dimensions et aux configurations de la plupart des machines vibrantes.
- C'est rentable - KWIKDECK vous permet d'utiliser des tamis synthétiques, qui durent au moins dix fois plus longtemps que les tamis à fils[1], et qui nécessitent moins d'entretien et de remplacement que les tamis à fils.
KWIKDECK est également parfait pour les opérations de criblage portables qui doivent alterner entre le tissu métallique et les médias synthétiques. Les opérateurs peuvent facilement passer d'un type de média à l'autre pour maximiser les exigences de production.
KWIKDECK offre aux utilisateurs de toiles métalliques traditionnelles la possibilité d'essayer des médias synthétiques avec un coût ou un risque minimal. Installez-le à l'extrémité d'alimentation de votre crible vibrant et constatez par vous-même la différence que cela fait.
En savoir plus sur KWIKDECKUn autre produit innovant de vos partenaires de Polydeck et un exemple de plus de la façon dont nous sommes en train d'améliorer la qualité de vie de nos clients. ensemble fort.
[1] http://www.pitandquarry.com/pq-university-lesson-8-screening/