La nécessité est la mère de l'invention. C'est ainsi qu'est né Polydeck, lorsque Manfred Freissle a constaté la nécessité d'un produit plus performant que le tissu métallique.
Aujourd'hui, Polydeck dispose de plus de 1 000 matrices, de nombreux matériaux et caractéristiques de surface - et pourtant, lorsqu'il s'agit d'accomplir une fonction nouvelle et différente, Polydeck invente encore et encore. Poursuivez votre lecture pour découvrir comment nos panneaux passent de l'idée à la production !
1. Le défi
Le défi se présente de lui-même. Il s'agit tout simplement de la partie "nécessité" où une exploitation de granulats, d'énergie et d'industrie ou minière doit faire quelque chose de différent. Lorsque Polydeck confirme que ce défi nécessite un nouveau panneau comme solution, nous nous mettons à inventer !
2. Collecte d'informations
Polydeck recueille toutes sortes d'informations : Quel type de matériau est traité ? Comment le matériau est-il broyé, quelles sont ses caractéristiques difficiles ? Un autre panneau a-t-il été essayé ? Toutes ces informations nous aident à créer la meilleure solution possible pour nos partenaires de criblage.

3. Conception. Conception. Conception.
Sur la base des informations recueillies en partenariat avec notre client, nous nous attelons à la conception du nouveau panneau. Des considérations telles que les caractéristiques de la surface (barrages, barres d'écoulement limité), la fixation, entre autres, qui peuvent ne pas faire partie de la nécessité initiale, garantissent que ce nouveau panneau sera aussi modifiable que possible afin d'offrir les merveilleuses caractéristiques des médias modulaires. Le panneau est élaboré et examiné par plusieurs parties, ce qui garantit qu'aucun détail n'est oublié.
4. Test du panneau
La preuve est faite par les tests. Le panneau est développé et testé, puis intégré à notre vaste gamme de matrices et de panneaux correspondants. Nous attribuons également une couleur au nouveau panneau afin de le différencier plus facilement des panneaux similaires.
5. Fini !
Et puis il est là. Bien qu'il n'y ait pas de baby shower pour lui, nous célébrons tous la naissance d'un nouveau panel, car il nous offre un nouvel ensemble de fonctions pour aider nos partenaires de la sélection.
Écrit par Alex CaruanaResponsable du territoire des granulats pour Polydeck.
Il est facile de se contenter de solutions de média d'écran qui nécessitent des temps d'arrêt pour le nettoyage et le remplacement. Améliorez votre débit, réduisez les temps d'arrêt et augmentez votre production grâce à la surface ouverte maximale et à la facilité d'utilisation des panneaux Maxi de Polydeck.
Dans un secteur qui remonte à des dizaines de milliers d'années, il est facile de se reposer sur ses lauriers lorsqu'on considère les facteurs de réussite et l'efficacité de ses opérations. Cependant, il est tout à fait possible de concevoir une opération efficace et avancée avec le bon média de criblage. La gamme Polydeck Maxi Les solutions de criblage à panneaux augmentent le débit et l'efficacité de la production d'une opération d'innombrables façons.
Le débit est, en termes simples, une mesure de la production et du succès. En termes de traitement des matériaux, cela signifie que votre média de criblage fait son travail. Un média de criblage efficace s'adapte à vos machines là où elles se trouvent, facilite le nettoyage et le remplacement, et assure un criblage maximal des matériaux avec le moins de temps d'arrêt possible. Pour de nombreuses opérations, l'efficacité est essentielle, en particulier lorsque les ressources sont limitées. S'arrêter pour dégager les bouchons et s'occuper d'une faible surface ouverte n'est tout simplement pas une option lorsque l'efficacité et la durabilité sont requises sur le site.
Si le support de l'écran ne fonctionne pas comme il le devrait, des arrêts coûteux en résultent, obligeant les travailleurs à passer des heures à déboucher les écrans et à les remettre en état pour qu'ils puissent reprendre la production. Client Polydeck Agrégats Dufferin Butler PitDufferin, situé à Cambridge, en Ontario, connaissait d'importants temps d'arrêt dus à l'encrassement. Avec une attention constante sur leurs objectifs d'efficacité et de production, Dufferin n'a pas perdu son temps à chercher une meilleure solution de média de tamisage. Après que l'équipe de Polydeck ait effectué une analyse de la performance des tamis sur place et présenté ses solutions avec la garantie que Dufferin atteindrait le débit désiré en faisant le changement, le choix a été simple.

Maxi Les bordures fines des panneaux sont spécialement conçues pour le débit, avec des angles en relief pour faciliter le criblage. Une fois les panneaux posés sur les cribles de nos clients, ils ont permis d'obtenir un nombre maximum d'ouvertures par mètre carré. En plus d'offrir des taux de rendement supérieurs, les polyuréthanes spécialement formulés des panneaux Maxi, combinés à la géométrie des panneaux, ont permis aux panneaux de fléchir et de conserver une durée de vie prolongée. Cette conception innovante, associée au processus de moulage par injection de Polydeck, a permis d'obtenir une surface ouverte précise et cohérente, ce qui s'est traduit par une augmentation de l'efficacité globale de Butler Pit.
Maxi Les panneaux Maxi offrent également un avantage par rapport au tissu métallique si l'on considère la résistance à l'abrasion du média synthétique et la facilité d'utilisation. Les opérations se tournent souvent vers le tissu métallique lorsque les exigences de production sont élevées, mais les panneaux Maxi offrent un avantage significatif en termes de coûts lorsque l'on tient compte des temps d'arrêt nécessaires pour remplacer le tissu métallique. La modularité des panneaux Maxi et les fermetures à pression rendent les changements et les échanges faciles et rapides. Moins de temps d'arrêt signifie plus d'heures productives sur le site. Plus de production signifie plus de rendement pour votre site. En bref, l'ajout des panneaux Maxi de Polydeck à vos opérations signifie que vous obtiendrez plus de votre site que jamais auparavant.
La clé du succès avec les écrans réside dans la technologie d'aujourd'hui et dans l'efficacité du système Polydeck. Maxi Les panneaux Maxi de Polydeck ont permis de réduire les temps d'arrêt et d'augmenter la production. Comme on peut le voir sur le site de notre client, les panneaux Maxi de Polydeck ont permis de réduire les temps d'arrêt et d'augmenter la production, deux éléments très importants pour le succès de toute opération.
Êtes-vous prêt à accroître le succès de votre opération ?
Sable et gravier de Vicdom sait très bien que la production et le lavage de granulats sont des opérations difficiles pour les équipements. Cette entreprise familiale de troisième génération produit des pierres, du sable et du gravier depuis plus de 40 ans à Uxbridge, dans l'Ontario (Canada), à 30 minutes de route au nord-est de Toronto.
La direction de Vicdom sait également que les temps d'arrêt inutiles ont un coût élevé. Jusqu'à récemment, l'entreprise rencontrait des problèmes d'usure périodiques sur les tamis métalliques de 5' x 7' de son système de tamisage à deux étages de 5' x 14'. Dillon écrans de lavage. Les tamis étaient utilisés pour produire +5/8" au-dessus du pont supérieur, 9/16"-1/4" au-dessus du pont inférieur, et 1/4" de copeaux à travers le pont inférieur. Bien que les tamis aient eu une durée de vie décente et aient satisfait aux exigences de production lorsqu'ils étaient en service, une fois endommagés, ils ont dû être complètement remplacés.
"Il suffit d'un trou dans la zone d'alimentation pour devoir changer tout le crible, même si 75 % du crible est encore en bon état", explique-t-il. Victor Giordanodirecteur adjoint chez Vicdom, et petit-fils de Vic Giordano, cofondateur de Vicdom. "Un écran $500 était devenu un déchet."
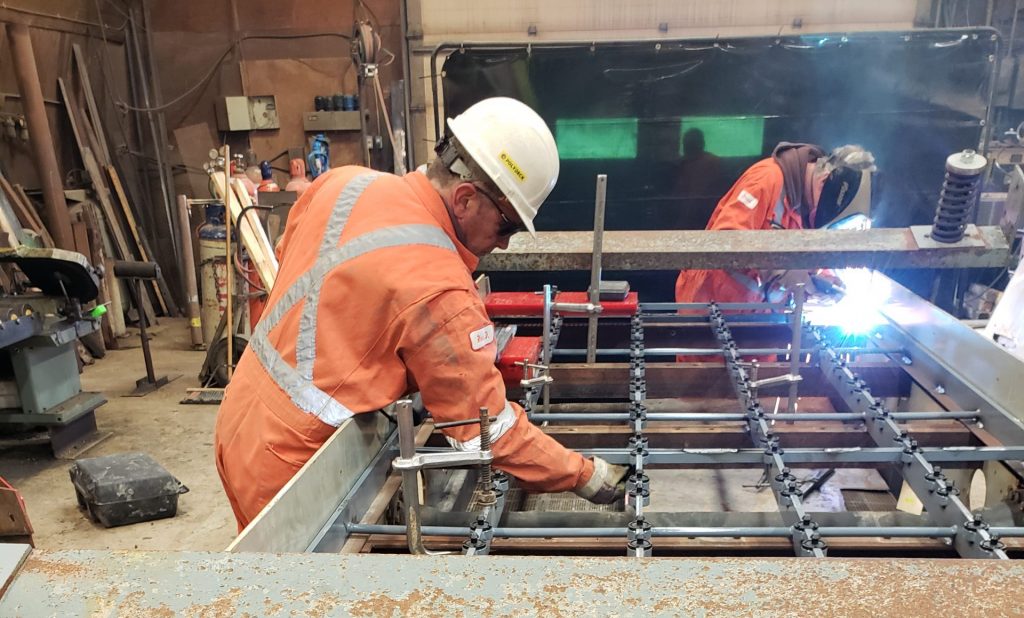
Le coût le plus important découlant du remplacement des écrans était le temps d'arrêt lié au remplacement des supports d'écran de 5' x 7', qui, selon M. Giordano, coûtait à son entreprise entre une et trois heures de temps d'arrêt chaque fois qu'il fallait les remplacer. Ainsi, lorsque Alex CaruanaLorsque M. Giordano, directeur territorial de Polydeck pour le centre du Canada et les provinces de l'Atlantique, a expliqué que l'entreprise pouvait économiser de l'argent et réduire les temps d'arrêt de ses activités en modernisant ses écrans de lavage avec un système modulaire à encliquetage, il a voulu en savoir plus.
"Alex a apporté un diagramme et a bien expliqué ce que nous avions avant avec le treillis métallique et ce que nous pourrions avoir avec Polydeck", dit Giordano. "Le plus gros reproche fait à caoutchouc et polyuréthane est qu'il n'a pas assez de surface ouverte comme le grillage, mais il a montré qu'on ne perdait pas de surface ouverte."
Caruana a montré à Giordano qu'il ne perdrait aucune zone ouverte en utilisant une méthode très simple, mais efficace.
"Ce que je fais généralement pour une usine lorsqu'elle envisage un ou plusieurs ponts est très simple. Je verrouille, je saute sur l'écran ou je prends une photo, et je compte simplement les ouvertures. Je connais la taille des ouvertures, parce que je les ai mesurées, et cela me permet également de tenir compte de toutes les obstructions telles que les barres de poussée, les rails de serrage latéraux, les déviateurs, les boulons et autres choses de ce genre. Cela me permet de montrer au client qu'avec sa toile métallique actuelle, il dispose d'une surface ouverte de 'X', quelle que soit la valeur de 'X'", explique Caruana. "Ensuite, je suis en mesure de leur montrer que dans leur application, en utilisant notre média, leur surface ouverte serait maintenant de "X+", et c'est leur nouveau numéro de surface ouverte."
Dans de nombreux cas, cette comparaison est une véritable révélation pour les producteurs.
"Même avec du tissu métallique, ils n'avaient peut-être pas tous les espace ouvert qu'ils pensaient avoir", explique Caruana. "Imaginez un morceau de grillage devant vous. Il n'est pas obstrué, et sa surface ouverte cataloguée, ou valeur comptable, pourrait être de 65%. Elle semble très attrayante. Mais lorsque vous le mettez en place, il y a des pièces de machine en dessous. Donc, vous n'avez pas vraiment 65%, mais plutôt 48%. Les supports synthétiques ne sont pas les mêmes. Lorsque le média synthétique donne une surface ouverte, c'est le chiffre brut et net. Une fois installé, il a toujours cette surface ouverte. Si quelqu'un vous dit que vous avez 48%, alors c'est le chiffre en place. Donc, si je fais cette comparaison pour des gens comme Victor chez Vicdom, ils ont cette information à leur disposition et ils peuvent faire un choix plus éclairé."
Vicdom a décidé de remplacer l'un de ses ponts de lavage par un système modulaire à enclenchement utilisant des panneaux de polyuréthane Polydeck de 1 pi x 1 pi avec des ouvertures carrées de 1/2 po sur le pont supérieur et des ouvertures d'environ 1/4 po sur le pont inférieur. Giordano a été impressionné par les résultats.
"Cette année, nous avons changé deux panneaux, au total, sur la conversion", dit-il. "Nous aurions normalement changé cinq ou six écrans entiers. Au lieu de cela, nous avons changé deux panneaux qui coûtaient $90 canadiens chacun pour $180 en un an. Les rendements sont bons, la capacité est bonne et les temps d'arrêt sont étonnants".
Vicdom a maintenant équipé les quatre ponts de ses deux tamis de lavage avec le système modulaire d'encastrement de Polydeck en utilisant des panneaux de polyuréthane de 1' x 1'. Le deuxième écran de lavage a des ouvertures de 5/8" sur le pont supérieur et des ouvertures d'environ 1/4" sur le pont inférieur.
La réduction des temps d'arrêt liés au changement de support d'écran n'est pas la seule raison pour laquelle Vicdom apprécie de travailler avec Polydeck. M. Giordano affirme que le niveau de professionnalisme de M. Caruana a été un argument de vente important, car il est toujours disponible pour aider à résoudre les problèmes qui surviennent sur le site.
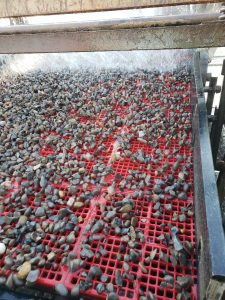
La société a eu un problème de traitement l'année dernière avec la première conversion, et a donc appelé Caruana pour en discuter.
Il m'a demandé : "Vous êtes sûr que vos excentriques vont vers le bas ?". se souvient Giordano.
Giordano a donc vérifié auprès de son équipe de maintenance et il s'est avéré qu'ils avaient effectué des travaux ce jour-là et qu'ils avaient accidentellement recâblé le moteur à l'envers sur l'écran, ce qui faisait que les excentriques tournaient vers le haut.
"Nous avons réparé le câblage, retiré la pierre et le système fonctionnait à nouveau. Grâce à ses connaissances, nous avons pu résoudre ce problème immédiatement", déclare Giordano, ajoutant qu'il apprécie énormément les connaissances techniques que Caruana apporte sur le chantier. "Je ne vois pas un vendeur. Je vois un gars qui a beaucoup d'expérience de la fosse maintenant dans la vente, et cela aide."
Vous envisagez une conversion ?
Polydeck dispose d'une équipe de professionnels et de plus de 40 ans d'expérience pour vous aider à optimiser les performances de votre criblage tout en minimisant les temps d'arrêt.
La nouvelle solution de tamisage de Polydeck maximise le débit et le mélange de produits..
Aggregate Industries (AIUS) est devenue l'une des plus grandes entreprises de matériaux de construction et de bâtiment aux États-Unis en mettant l'accent sur la durabilité stratégique, la gestion de l'environnement et les relations à long terme avec les clients. La carrière Morrison de la société, une exploitation de granit de 3 millions de tonnes par an située dans le comté de Jefferson, dans le Colorado, illustre parfaitement sa mission.
Le comté de Jefferson est l'un des trois comtés de la région de Denver, qui compte six comtés et fait partie de la région centrale ouest de l'AIUS, qui offre des sources disponibles de pierre concassée. Étant donné que de nombreuses ressources potentielles en granulats dans la région de Denver ne sont pas accessibles à l'extraction, la carrière de Morrison joue un rôle essentiel pour répondre à la demande de la région en matériaux granulats de haute qualité.
Trulane Vanatta, directeur de l'usine Morrison, exploite une usine "à guichet fermé", ce qui signifie que tout ce qui est traité un jour donné est vendu le lendemain. Pour lui, explique-t-il sans ambages, " [ ?Le débit est essentiel."
Par conséquent, l'installation se concentre constamment sur l'amélioration de l'efficacité du traitement et de la capacité de production. Pour éliminer les goulots d'étranglement dans les circuits de criblage, l'équipe de gestion de Morrison a fait appel aux experts en ingénierie de Polydeck.
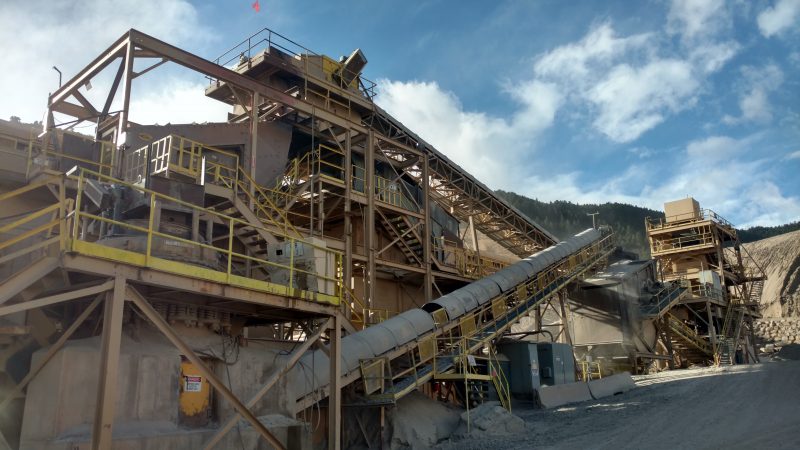
Réduire les charges de recirculation et les amendes
L'équipe de Vanatta a identifié un problème dans le circuit tertiaire de l'usine à neuf cribles. Leurs échantillons de bande indiquaient une profondeur de lit élevée sur les ponts intermédiaires des trois cribles du circuit. Chacun des cribles à trois étages de 8 pieds sur 20 pieds est essentiel à la production du matériau #57/#67 (1 pouce) de Morrison.
"C'est notre gagne-pain, et nous devons maximiser son volume de production.dit Vanatta.
Son équipe a trouvé un report " troublant " de 51%, un goulot d'étranglement qui provoquait des charges de recirculation et produisait des fines excessives - un problème de production courant. "La première chose à laquelle nous avons pensé a été de remplacer les ponts intermédiaires de deux des cribles tertiaires par du tissu métallique pour obtenir une plus grande surface ouverte.", se souvient Vanatta.
Il s'avère cependant que le directeur régional de Polydeck, Sam DurnavichIl y a plus de dix ans, Sam était le directeur adjoint de l'usine de la carrière Morrison avant de se joindre à l'organisation Polydeck. Grâce à sa connaissance de l'exploitation, Sam a consulté la direction de Morrison et a travaillé en étroite collaboration avec l'équipe d'ingénieurs de Polydeck afin de créer une solution média qui permettrait de relever plus efficacement le défi de l'entraînement.
Après une analyse approfondie du fonctionnement de Morrison, l'équipe de production de Polydeck a conçu et installé un tout nouveau produit : DMAX™ un système de tamis synthétique à très grande surface ouverte qui augmente considérablement le débit et permet à la carrière d'accroître la production de ses produits de plus grande valeur.
Les nouveaux panneaux de criblage DMAX de Polydeck sont destinés à être utilisés lorsque la surface ouverte et le débit sont les considérations les plus importantes. Il s'agit d'une solution modulaire de panneaux de criblage synthétiques dont la surface ouverte est égale ou même supérieure à celle des toiles métalliques, tout en offrant une plus grande durée de vie et une installation plus facile. Le système de panneaux de criblage DMAX peut également être formulé avec du caoutchouc ou du polyuréthane, selon l'application.
Dépasser les objectifs de production
Depuis l'installation du premier DMAX Grâce à l'installation de panneaux de criblage sur deux des étages intermédiaires en octobre 2015, l'entreprise a atteint et souvent dépassé ses objectifs de production. Ils ont également atteint une efficacité de criblage bien plus grande, selon Vanatta - près de 54% de surface ouverte sur leurs ponts intermédiaires, par rapport aux 42% de surface ouverte fournis par leur pont de criblage précédent. Il s'agit d'une augmentation spectaculaire de 28,5% de la surface ouverte. Morrison a ensuite installé des panneaux DMAX sur un troisième pont intermédiaire à la mi-2016.
"Pour nous", dit Vanatta, "L'augmentation de la surface ouverte s'est traduite par une augmentation de 11% de la production de roche rentable de 1 pouce, et a réduit les fines de près de 1%. Le seul inconvénient de la surface ouverte est que les panneaux s'usent un peu plus vite, mais cela n'a pas d'importance puisque le bénéfice de l'augmentation du tonnage rembourse plus de dix fois l'investissement dans le média de criblage.."
La carrière de Morrison utilise également les panneaux de criblage modulaires Rubberdex® de Polydeck sur les étages supérieurs et inférieurs de ses cribles tertiaires de 8 pieds par 20 pieds.
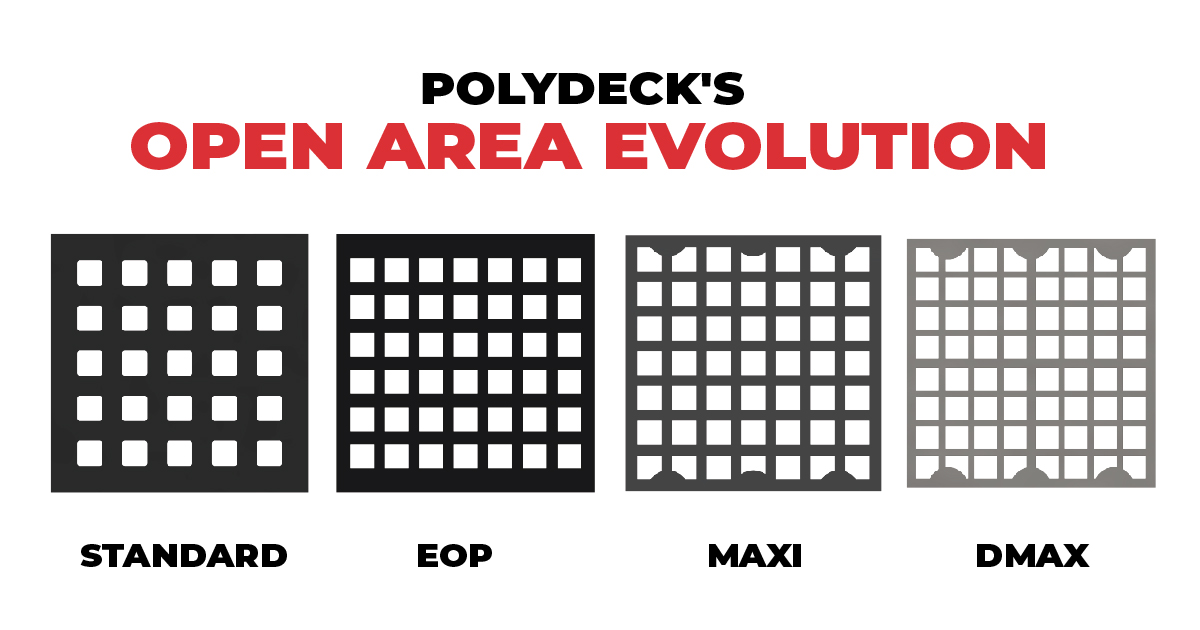
Expertise en ingénierie
Explique Sam Durnavich de Polydeck, "Nous avons fabriqué les panneaux DMax avec des ponts deux fois moins larges que ceux de notre maxi panneau standard, mais beaucoup plus profonds. C'est important, car la réduction de la largeur du pont entre les ouvertures permet d'augmenter le nombre d'ouvertures dans la surface du panneau, ce qui se traduit par un meilleur passage du produit.."
"Le fait que les panneaux DMax soient conçus pour s'adapter aux systèmes de limons Polydeck PipeTop II existants contribue à accroître la surface ouverte.", poursuit M. Durnavich. "Ce système d'armature comporte des rails de fixation uniques d'un demi-pouce de large au lieu des styles de montage des systèmes d'armature conventionnels avec jusqu'à 3 pouces d'espace mort où les amendes s'accumulent. En outre, nos capacités d'outillage en interne nous permettent de proposer beaucoup plus d'options dans ces systèmes d'armature, qu'il s'agisse des options de fixation, des options de matériaux ou des styles et types de longerons.."
"L'augmentation de la surface ouverte fait s'accompagnent d'une réduction de la durée de vie des panneaux d'écran", admet Durnavich, "Mais si l'on compare les panneaux de criblage à usage standard, les panneaux DMax ont une durée de vie inférieure de seulement 20-25%, ce qui dépasse toujours celle des toiles métalliques.."
"Notre utilisation du moulage par injection est un facteur important dans la capacité de créer des panneaux synthétiques à surface ouverte extrême.ajoute M. Durnavich. "Le moulage par injection permet de s'assurer que chaque panneau d'écran a des tailles et des formes d'ouverture précises, et qu'il est entièrement durci.."
"Nos résultats réels sur le terrain dans plusieurs applications ont démontré des augmentations de production allant jusqu'à 50%, et des augmentations de l'efficacité du filtrage de plus de 25%.dit Durnavich avec un sourire.
Polydeck continue d'élargir la gamme des ouvertures disponibles dans la série DMax, avec des ouvertures carrées de 12,5 mm à 32 mm, ainsi que des ouvertures fendues de 3x20 mm à 25x74 mm.
On le dit souvent : S'il y a un goulot d'étranglement dans une usine, c'est probablement au niveau du circuit de criblage. Le débit est primordial pour la carrière Morrison, et l'augmentation continue de l'efficacité du criblage est essentielle à sa rentabilité et à la qualité de ses produits. En travaillant ensemble, la carrière Morrison et Polydeck ont résolu un problème immédiat et créé une solution à long terme.