Es fácil conformarse con soluciones de medios de pantalla que requieren tiempos de inactividad para su limpieza y sustitución. Mejore su rendimiento, reduzca el tiempo de inactividad y aumente la producción con la máxima superficie abierta y la facilidad de uso de los paneles Maxi de Polydeck.
En un sector que se remonta a decenas de miles de años, es fácil caer en la autocomplacencia a la hora de considerar los factores de éxito y la eficiencia de las operaciones. Sin embargo, es más que posible diseñar una operación que sea eficiente y avanzada con los medios de cribado adecuados. Polydeck Maxi aumentan el rendimiento y la eficacia de la producción de innumerables maneras.
El rendimiento es, en pocas palabras, una medida de la producción y el éxito. En términos de procesamiento de materiales, significa que sus medios de cribado están haciendo su trabajo. Unos medios de cribado eficientes se adaptan a sus máquinas allí donde están, facilitan la limpieza y la sustitución y proporcionan el máximo cribado de material con el menor tiempo de inactividad posible. Para muchas operaciones, la eficacia es fundamental, especialmente cuando los recursos son limitados. Detenerse para despejar tapones y lidiar con poca superficie abierta simplemente no es una opción cuando se requiere eficiencia y sostenibilidad de la obra.
Si los medios de cribado no rinden como deberían, se producen costosas paradas que obligan a los trabajadores a pasar horas limpiando tapones y llevando las cribas a un lugar en el que puedan comenzar de nuevo la producción. Cliente de Polydeck Dufferin Aggregates Butler PitDufferin, situada en Cambridge, Ontario, estaba experimentando un tiempo de inactividad significativo debido al pegado. Con un enfoque constante en sus objetivos de eficiencia y producción, Dufferin no perdió el tiempo buscando una mejor solución de medios de cribado. Después de que el equipo de Polydeck llevara a cabo un análisis del rendimiento de la pantalla in situ y presentara sus soluciones con la garantía de que Dufferin experimentaría el rendimiento deseado al realizar el cambio, la elección fue sencilla.

Maxi Los finos bordes de los paneles se han diseñado específicamente pensando en el rendimiento, con ángulos de relieve para facilitar el cribado. Una vez colocados en las cribas de nuestros clientes, los paneles proporcionaron el máximo número de aberturas por pie cuadrado. Además de ofrecer unos índices de rendimiento líderes, los poliuretanos especialmente formulados de los paneles Maxi, combinados con la geometría diseñada de los paneles, permitieron que éstos se flexionaran y mantuvieran una vida útil prolongada. Este diseño innovador, junto con el proceso de moldeo por inyección de Polydeck, garantizó un área abierta precisa y uniforme, lo que se tradujo en un aumento de la eficiencia global en Butler Pit.
Maxi ofrecen también una ventaja sobre las telas metálicas si se tiene en cuenta la resistencia a la abrasión de los materiales sintéticos y la facilidad de uso. A menudo se opta por las telas metálicas cuando los requisitos de producción son elevados, pero los paneles Maxi suponen una importante reducción de costes si se tiene en cuenta el tiempo de inactividad necesario para cambiar las telas metálicas. La modularidad de los paneles Maxi y sus cierres a presión facilitan y agilizan los cambios. Menos tiempo de inactividad significa más horas productivas en la obra. Más producción significa más rendimiento de su obra. En resumen, añadir los paneles Maxi de Polydeck a sus operaciones significa que obtendrá más rendimiento de su obra que nunca.
La clave del éxito de los soportes de pantalla reside en la tecnología actual y en la eficacia de los sistemas Polydeck. Maxi paneles. Como se vio en las instalaciones de nuestro cliente, los paneles Maxi de Polydeck redujeron el tiempo de inactividad y aumentaron la producción, dos elementos muy críticos para el éxito en cualquier operación.
¿Está preparado para aumentar el éxito de su operación?
Cuando se eliminan los cuellos de botella de la parte superior, se aumenta la capacidad de producción y se pone más producto vendible sobre el terreno. Lea cómo Polydeck ayudó a conseguir un mayor nivel de eficiencia de forma rentable.
Si dirige una planta de áridos, sabrá que la eficacia de sus cribas de cubierta superior es fundamental para el rendimiento global de su explotación. Es una fórmula sencilla: Cuando se eliminan los cuellos de botella de la cubierta superior, se aumenta la capacidad de producción y se pone más producto vendible en el suelo. Pero, ¿cómo pueden los operadores alcanzar ese nivel de eficiencia de forma rentable?
La respuesta de Polydeck a esta pregunta es una ecuación de medios de pantalla que combina paneles modulares de pantalla de alambre soldado con paneles de medios sintéticos. Cada tipo de panel modular está estratégicamente situado en la plataforma superior para ofrecer la máxima superficie abierta y una vida útil superior. Para los operadores, el resultado es un mayor rendimiento y un menor tiempo de inactividad por mantenimiento = más beneficios y menos gastos.
Socio de Polydeck, Recursos de Alleytones un productor de agregados y concreto premezclado con sede en Houston, TX. Sus operaciones incluyen 11 sitios RMC y ocho lugares de procesamiento de agregados, y proporcionan transporte de materiales, entrega de concreto premezclado, bombeo de concreto, y arena estabilizada y lechada a sus clientes.
Brandon Genzer (director de planta de la planta Vox de Alleyton en Garwood, Texas, en aquel momento) se enfrentaba a depósitos gruesos en el emplazamiento, así como a dificultades para desalojar la cubierta superior de su criba secundaria húmeda de acabado inclinado, que estaba equipada con medios de poliuretano.
"La criba se alimenta con material de 2-1/2 pulgadas menos", explica. "Teníamos mucho arrastre de material de 1-1/2 pulgadas, lo que creaba cargas de recirculación innecesarias que volvían a la trituradora".
Esto suponía un gran problema para sus operaciones, ya que las cargas recirculantes aumentaban significativamente tanto el desgaste de la trituradora como los costes operativos por tonelada. Además, estaba mermando los márgenes de beneficio de las instalaciones al enviar el producto acabado de vuelta a la trituradora en lugar de a la pila de productos vendibles.

Para eliminar este costoso problema de arrastre, Genzer consultó con el responsable de Polydeck para la región del sur de Texas en aquel momento, Kent Ropp. "Trabajo estrechamente con cada productor de mi zona para analizar su aplicación y crear configuraciones de paneles de pantalla modulares que ofrezcan las especificaciones deseadas".
Ropp trabajó con Genzer para especificar los nuevos materiales realizando varias horas de funcionamiento para cada muestra de material. "Conectábamos distintos materiales para ajustar nuestro módulo de finura justo donde lo necesitábamos", recuerda Genzer.
Finalmente, Ropp recomendó una combinación de productos de alto rendimiento de Polydeck. Para una mayor superficie abierta y rendimiento, Polydeck METALDEX™ Se instalaron paneles modulares de acero en el extremo de descarga de la criba de 6 x 16 pies. Para absorber el impacto en el extremo de alimentación de la criba, RUBBERDEX Se instalaron paneles de caucho sintético para maximizar la vida útil de la cubierta superior. Las cubiertas intermedia e inferior se equiparon con POLYDEX paneles modulares de pantalla de poliuretano.

El METALDEX™ ofrecen un área abierta que iguala o supera a las telas metálicas tradicionales de la misma abertura y diámetro de alambre. Además de una mayor superficie abierta, la modularidad de los paneles permite aplicarlos en el extremo de alimentación o, lo que es más importante, en el extremo de descarga, donde una mayor superficie abierta es fundamental para eliminar las cargas de recirculación.
Las pruebas realizadas por Ropp en la planta de Vox determinaron que la adición de paneles Metaldex en el extremo de descarga aumentó el rendimiento de la criba hasta 55,9% de área abierta por encima de los 33,4% que conseguían con los anteriores paneles de caucho sintético.

"Incluso en turnos prolongados de 12 a 16 horas, el primer juego duró más de cuatro meses. Cuando ampliamos el horario, comprobamos las pantallas al final de cada turno. Si es necesario, el personal puede cambiar los paneles en cuestión de minutos y volvemos a estar en marcha".
Según Ropp, la clave de la mayor duración de METALDEX es que: "Está compuesto de acero Brinell AR 500 resistente a la abrasión, que prolonga la vida útil en la mayoría de las aplicaciones frente a la de las telas metálicas estándar. El alambre soldado simplemente ofrece un mayor grado de rendimiento en fuerza y resistencia a la corrosión".
Otra ventaja para la planta de Vox es que METALDEX™ Los paneles friegan mejor el material, eliminando el contenido de arcilla. "Ahora obtenemos lo mejor de ambos mundos: roca más limpia con un mayor rendimiento", afirma Genzer, que añade que la planta produce una media de 550 toneladas por hora, un aumento significativo desde que se ajustó el circuito de cribado. Desde entonces, Alleyton ha implantado un sistema METALDEX™ criba en otra operación para ayudar a romper y eliminar el contenido de arcilla en su material.
Dado que la flexibilidad de procesamiento es importante en las instalaciones de Vox -que produce principalmente material de 1-1/2 pulg. menos, material de 3/8 pulg. menos y arena de hormigón- la modularidad de los paneles de cribado les permite cambiar fácilmente los paneles o ajustar las configuraciones para adaptarse a las distintas alimentaciones de material o requisitos de procesamiento. Además, los bordes de cada panel de alambre soldado de 1 pie x 2 pies están recubiertos de poliuretano, lo que facilita mucho su manipulación en comparación con las grandes secciones de tela metálica.
"METALDEX™ es otro innovador diseño de panel de cribado de Polydeck que mejora la gama de soluciones de medios de cribado y ayuda a nuestros clientes a superar sus objetivos de producción", afirma Ropp. "Ofrece la prolongada vida útil del acero resistente a la abrasión con el área abierta de la tela metálica, y la ingeniería modular permite una fácil manipulación y una sencilla fijación al sistema de bastidor de largueros de Polydeck."
La eliminación de los cuellos de botella en el cribado es esencial para maximizar el rendimiento en el cribado de cubierta superior, que es, a su vez, crítico para el rendimiento óptimo de la planta. En la planta Vox de Alleyton Resources, la innovadora combinación de alambre soldado y paneles de medios sintéticos de Polydeck fue la fórmula precisa para resolver sus problemas de cribado.
NUEVO METALDEX de Polydeck™ VR

En 2020, Polydeck lanzó una nueva oferta de productos: METALDEX™ VR. La nueva solución de pantalla de alambre modular de Polydeck se integra con nuestro PIPETOP™ sistema de largueros. Perfecto para aplicaciones de encolado en seco en las que se requiere más superficie abierta y eficacia, METALDEX™ VR se instala idealmente en el extremo de descarga, donde proporciona una mayor vida útil y un mejor rendimiento, y su exclusivo patrón en forma de diamante elimina el cegamiento y el taponamiento.
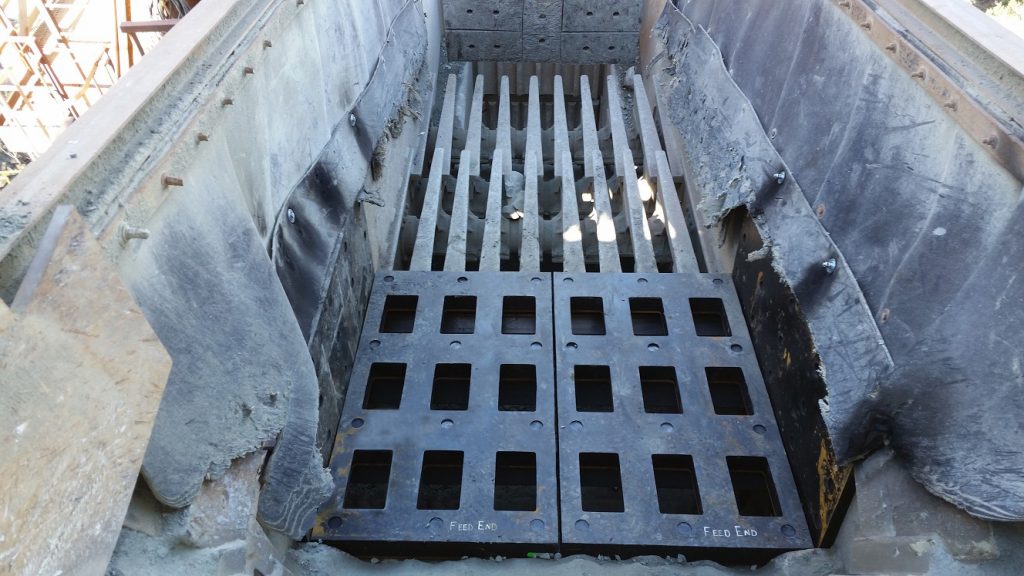
Para que los circuitos de machaqueo primario y secundario funcionen de forma óptima, es esencial que el escalpado sea eficaz. Para aumentar la eficacia del scalping, la operación Hanson instaló ARMADEX secciones de goma personalizadas al segundo escalón, al que pronto seguirá el tercero.
Sencillamente, la capacidad de producción y la vida útil aumentan cuando se eliminan los finos de la alimentación primaria de la mandíbula; cuando se alimentan las mandíbulas con exceso de material; y cuando el material de tamaño inferior a los ajustes de la trituradora de mandíbulas pasa a través de las barras grizzly para su posterior trituración y clasificación.
Sin embargo, en aplicaciones extremadamente abrasivas, de alto impacto y gran desgaste, lograr la eficacia óptima de descascarillado puede ser todo un reto.
Problema-Solución
Para reducir los costes de explotación por tonelada y satisfacer al mismo tiempo la demanda del mercado de áridos para asfalto y hormigón de alta calidad, la cantera Clayton de Lehigh Hanson, con sede en California, trató de eliminar los cuellos de botella existentes o potenciales en toda su planta. La cantera Clayton, que da servicio a la región de la bahía de San Francisco, es uno de los 200 centros de producción de áridos y terminales de distribución propiedad de Hanson, que produce áridos, asfalto, hormigón premezclado y otros materiales de construcción en toda Norteamérica.
"Nuestro tajo es una cantera de roca dura de perforación y voladura que se inició en 1956", dice Marc McNeil, director de planta de la cantera Clayton. "Desde finales de la década de 1990, nuestro enfoque ha cambiado gradualmente de la producción de roca base a la piedra triturada y la arena manufacturada, y nuestra planta envejecida requería algunas actualizaciones desde la alimentación inicial hasta el acabado del producto".
Marc McNeil, director de planta de Lehigh Hanson's Clayton Quarry, supervisa las mejoras actuales de la planta, desde la alimentación inicial hasta el acabado del producto.
Las mejoras empezaron por abordar los retos del descascarillado y el dimensionamiento. La dura aplicación de descamación de rocas granalladas de alto impacto de la cantera Clayton implicaba un desgaste extremo, así como unos costes de mantenimiento y una mano de obra excesivos para sustituir y reparar las barras grizzly desgastadas.
Finalmente, la cantera Clayton eligió una solución de cribado personalizada diseñada y fabricada por Polydeck. ARMADEX es un producto de cribado de caucho personalizado que se aplicó en secciones atornilladas al primer escalón (5 pies) del alimentador vibratorio Grizzly de la planta.
"Desde que instalamos ARMADEX, hemos reducido significativamente el tiempo de inactividad por mantenimiento y los costes de desgaste, hasta el punto de que finalmente hemos aplicado ARMADEX al segundo escalón de la criba, con planes de instalación en el tercer escalón actualmente en curso", afirma McNeil.
Retos del scalping de alto impacto
La cantera Clayton extrae una roca diabasa que se transporta hasta la planta de trituración primaria y se carga en una tolva de 150 toneladas.
Para reducir el tiempo de inactividad por mantenimiento y los costes de desgaste, un producto de cribado de goma a medida, ARMADEXse aplicó en secciones atornilladas al primer escalón del grizzly.
Un alimentador de bandeja toma el material de 24 pulgadas menos de la tolva y lo alimenta al grizzly vibratorio. El grizzly sufre un fuerte impacto, ya que el material desciende 3,5 m antes de golpear las barras del grizzly. El impacto sobre el material de acero generaba un ruido considerable y provocaba un desgaste excesivo del extremo de alimentación del grizzly.
Además, la alimentación fina procedente del pozo a menudo provocaba que el primer conjunto de barras grizzly se puenteara.
"Las barras están atornilladas a una barra de soporte, pero con el puenteo y el desgaste excesivo, las barras empezarían a moverse y a abrirse, permitiendo el paso de roca de mayor tamaño", dice McNeil. "Cuando esa roca de gran tamaño pasa al circuito secundario, la trituradora de cono pierde eficacia".
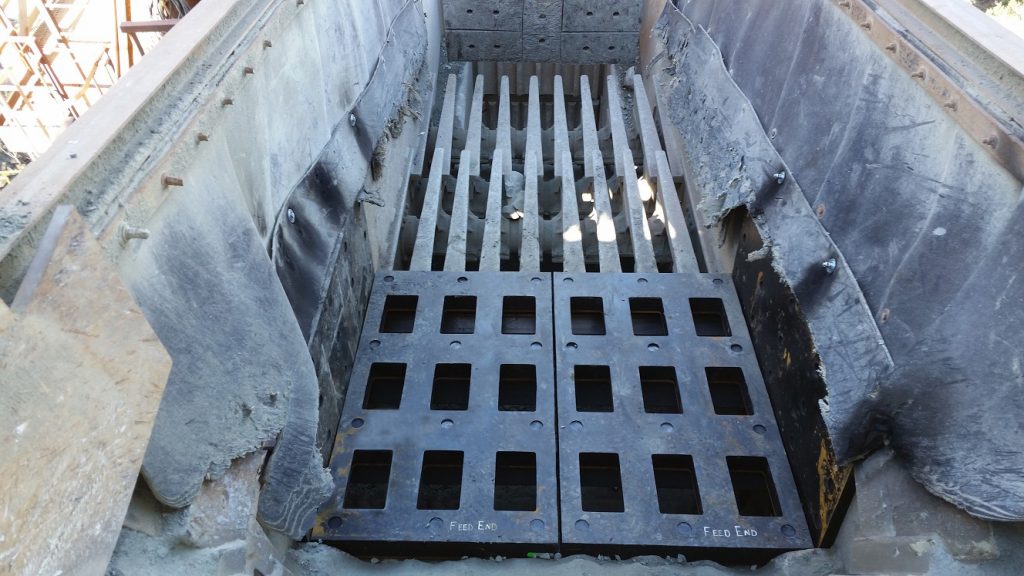
Lo más importante era el tiempo de inactividad por mantenimiento adicional y los costes de mano de obra. El movimiento de las barras Grizzly requería hasta 20 horas semanales de soldadura para fijarlas en su sitio, afirma McNeil.
"Por motivos de seguridad, para trabajar en un Grizzly hay que llevar arnés", añade. "Así que si un trabajador está soldando barras con regularidad, se convierte en todo un reto. Intentamos sustituir todo el juego de barras y fue muy costoso. Tenía que haber otra forma".
Soluciones de scalping personalizadas
En toda su planta de acabado, tanto en las cribas húmedas como en las secas, la cantera Clayton utiliza paneles modulares de poliuretano sintético y caucho Polydeck.
La cantera Clayton utiliza paneles modulares de poliuretano sintético y caucho en toda su planta de acabado, tanto en cribas húmedas como secas.
"Hemos tenido buenos resultados con sus productos de medios de pantalla, así que pedimos a los ingenieros de aplicaciones de Polydeck que evaluaran nuestro circuito de scalping para ver qué se podía hacer", dice McNeil. "Propusieron utilizar ARMADEXun material muy adecuado para aplicaciones de descascarillado abrasivas y duras. Decidimos probarlo en el primer escalón de la criba, y vimos beneficios inmediatos en la reducción del tiempo de inactividad por mantenimiento y de los costes de desgaste".
Como subraya Peter Babinski, de Polydeck, los productores de áridos desean el máximo tiempo de actividad, un mantenimiento mínimo, una mayor vida útil y una reducción del ruido, especialmente en aplicaciones de alimentadores grizzly abrasivos. Los productores suelen buscar soluciones de materiales sintéticos para obtener esas ventajas, afirma.
Como explica Babinski, los medios de cribado de caucho ARMADEX utilizan la tecnología de moldeo por inyección a alta presión, un método de fabricación de Polydeck que produce 10 veces la presión normalmente utilizada para producir caucho moldeado por compresión.
"La combinación de esta tecnología con nuestro compuesto de goma de caucho de primera calidad y el soporte de chapa de acero HSLA produce una resistencia sin precedentes en un producto que ofrece una vida útil mucho más larga a un menor coste por tonelada", afirma Babinski, que trabaja en Polydeck como director del territorio de áridos de la Costa Oeste/Estados Montañosos.
"Con las barras Grizzly, las operaciones no pueden ajustarlas a menos que las cambien completamente o las suelden para cambiar las aberturas", dice Babinski. "Las secciones atornilladas ARMADEX nos dan la flexibilidad de acceder a aberturas más pequeñas o más grandes para ajustar el rendimiento en una aplicación determinada".
Para instalar las secciones ARMADEX en el alimentador grizzly de la cantera Clayton, Polydeck diseñó un marco personalizado que se atornilla a los paneles laterales del grizzly. Las secciones ARMADEX se atornillan fácilmente a ese bastidor.
"Para nosotros fue una sustitución sencilla y directa, con muy poco tiempo de inactividad, gracias a la atención al detalle que Polydeck prestó a la personalización de nuestra aplicación", afirma McNeil.
Eficacia de escalado y dimensionamiento
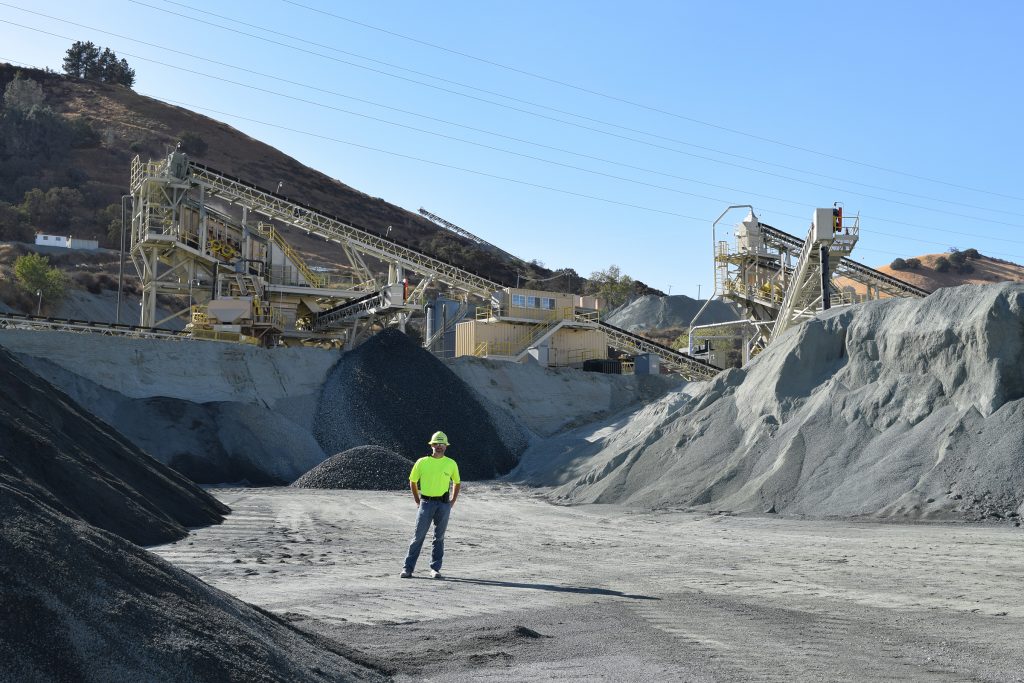
Según McNeil, la operación ha mejorado enormemente la eficiencia diaria de scalping y dimensionamiento mediante el uso de ARMADEX secciones de medios. Al impedir que el material de gran tamaño pasara a la trituradora de cono, la operación aumentó el rendimiento de trituración y redujo el tiempo de inactividad.
"Hemos reducido drásticamente los costes de mantenimiento, ya que todavía no hemos cambiado ninguna sección ARMADEX desde su instalación, y no requieren soldaduras semanales", afirma McNeil, que añade que las secciones de medios en el primer escalón de la criba han procesado un caudal de material de casi 3 millones de toneladas en tres temporadas de producción.
La cantera Clayton sigue trabajando con Polydeck para mejorar el rendimiento. El circuito de corte empleará aberturas redondas en las secciones ARMADEX utilizadas en el tercer escalón del alimentador grizzly, lo que aumentará el rendimiento de la roca angular que puede quedar atrapada en aberturas cuadradas o rectangulares.
Si se ajustan los circuitos de extracción en la parte superior de la cadena, los siguientes sufrirán menos desgaste, aumentarán su capacidad de producción y se venderán más productos en los almacenes.
Escrito por Carol Wasson, veterana redactora independiente de los sectores de los áridos y los equipos de construcción.
LafargeHolcimLafargeHolcim, líder mundial en materiales y soluciones para la construcción, es un productor activo en los segmentos de negocio de Cemento, Áridos, Hormigón Premezclado y Soluciones y Productos de las industrias a las que sirve la Compañía. Como empresa cuya actividad se centra en el uso de materiales naturales, LafargeHolcim es plenamente consciente de sus responsabilidades desde el punto de vista de la sostenibilidad. Recientemente, el equipo directivo de la empresa puso de manifiesto que la sostenibilidad es un componente clave de su estrategia empresarial y algo que están evaluando activamente en cada centro con sus informes anuales. Considerar el impacto medioambiental y de sostenibilidad de cada una de sus operaciones y centros es fundamental para su éxito como empresa que depende de materiales naturales.
Woodstock de LafargeHolcimLa cantera de Polydeck, en Ontario, Canadá, experimentó un gran avance en la sostenibilidad de la operación y en el rendimiento final de material utilizable gracias a la tecnología líder de Polydeck. boquilla pulverizadora tecnología. Anteriormente, la cantera de Woodstock se dedicaba en gran medida a extraer y procesar yacimientos de piedra caliza, un material de construcción fundamental. Históricamente, la explotación se centraba en la voladura, extracción, trituración y cribado de piedra caliza. Como planta de alimentación de una cementera cercana, la viabilidad de la explotación de la cantera era evidente. Sin embargo, cuando el mercado de la piedra caliza cambió, la explotación se vio en la necesidad de adaptarse a las cambiantes demandas del mercado.
El cambio de mercado hizo que se suministrara más piedra para asfalto y hormigón. Cuando la explotación empezó a centrarse en estos materiales, empezó a generar finos. De hecho, el equipo de la cantera de Woodstock se dio cuenta de que estaban produciendo montañas de finos. Como la cultura de la empresa había evolucionado para tener en cuenta el impacto de cada operación e innovar en materia de sostenibilidad, la bombilla empezó a encenderse en Woodstock: los finos resultantes podían procesarse para convertirlos en un material propio y utilizable. Aunque el objetivo final parecía claro, aún era necesaria cierta adaptación y creatividad. Ahí es donde entró el equipo de Polydeck para ayudar a la planta a definir su nuevo enfoque.
LafargeHolcim sabía que los finos reprocesados serían altamente comercializables, y tenían razón. Resultó obvio que las boquillas de pulverización de Polydeck, diseñadas para soportar lavados intensivos, eran la respuesta para adaptar las cubiertas y crear un producto comercializable.
Aunque una boquilla pulverizadora parece un producto sencillo, el diablo está realmente en los detalles. Cuando la cantera empezó a buscar una solución de lavado, sabía que necesitaba el producto más eficaz y duradero del mercado. Lo ideal era que las boquillas pulverizadoras tuvieran la capacidad de suministrar agua a la presión y geometría adecuadas para producir un efecto de lavado que diera como resultado una separación y rendimiento adecuados del material. Las boquillas pulverizadoras de Polydeck, instaladas en la máquina horizontal Simplicity 8x20 Triple Deck de LafargeHolcim, hicieron precisamente eso. Cuando una boquilla pulverizadora funciona correctamente, los materiales no deseados clasificados y distribuidos se liberan y aíslan como material utilizable.
La cantera de Woodstock empezó a probar un proceso de lavado para extraer los finos utilizando tela metálica, que es un producto habitual en las operaciones de lavado. Sin embargo, el mantenimiento y el tiempo de intervención de la tela metálica pronto resultaron muy ineficaces para la operación. El tiempo dedicado a cambiar las telas metálicas era tiempo que no se empleaba en producir material vendible.
Tras darse cuenta de que la tela metálica era una solución ineficaz, LafargeHolcim recurrió de nuevo a Polydeck y decidió diseñar una planta para producir el material patentado. Polydeck equipó las tres cubiertas de LafargeHolcim con medios sintéticos así como boquillas de pulverización. Los resultados fueron asombrosos. Adaptándose a una situación que presentaba un reto de espacio extremadamente estrecho, las boquillas de pulverización de Polydeck no sólo encajaron, sino que ejecutaron el trabajo con seguridad. El material que antes se desperdiciaba ahora se separaba gracias a los eficientes resultados de lavado producidos por la combinación de las boquillas de pulverización Polydeck y los medios de cribado. Las boquillas de aspersión Polydeck cuentan con una función de autolimpieza que eliminó una cantidad significativa de horas-hombre y su facilidad de reemplazo y mantenimiento aseguró que la cantera Woodstock no experimentara un tiempo de inactividad significativo en caso de que una pieza o boquilla necesitara ajuste, reemplazo o limpieza.
LafargeHolcim aprendió de primera mano cómo la adaptación de su operación de lavado con boquillas de pulverización Polydeck en su operación de Woodstock aumentó su eficiencia, rendimiento y sostenibilidad. Un subproducto anterior con aplicaciones muy limitadas se transforma en un producto altamente comercializable dentro de unas especificaciones muy estrictas. El mantenimiento se reduce y simplifica. La "cubierta de dinero", como muchos la llaman, queda libre para producir material que genere beneficios para la operación. Cuando los resultados y la sostenibilidad importan, las boquillas de pulverización autolimpiantes, de alta resistencia y eficacia de Polydeck son insuperables.
Vicdom Sand & Gravel sabe muy bien que producir y lavar áridos es duro para los equipos. Esta empresa familiar de tercera generación lleva más de 40 años produciendo piedra, arena y grava en Uxbridge, Ontario (Canadá), a 30 minutos en coche al noreste de Toronto.
La dirección de Vicdom también sabe que los tiempos de inactividad innecesarios tienen un coste elevado. Hasta hace poco, la empresa había tenido problemas periódicos de desgaste con los medios de tamizado de alambre de 5' x 7' en su tamiz de dos pisos de 5' x 14'. Dillon cribas de lavado. Las cribas se utilizaban para producir +5/8" sobre el piso superior, 9/16"-1/4" sobre el piso inferior y 1/4" de viruta a través del piso inferior. Aunque las cribas tenían una vida útil aceptable y cumplían los requisitos de producción cuando estaban en funcionamiento, cuando se dañaban había que sustituirlas por completo.
"Nos hacíamos un agujero en la zona de alimentación y teníamos que cambiar toda la criba, aunque el 75% de la criba siguiera en buen estado", dice Victor Giordanosubdirector de Vicdom y nieto del difunto cofundador de Vicdom, Vic Giordano. "Una pantalla $500 era ahora basura".
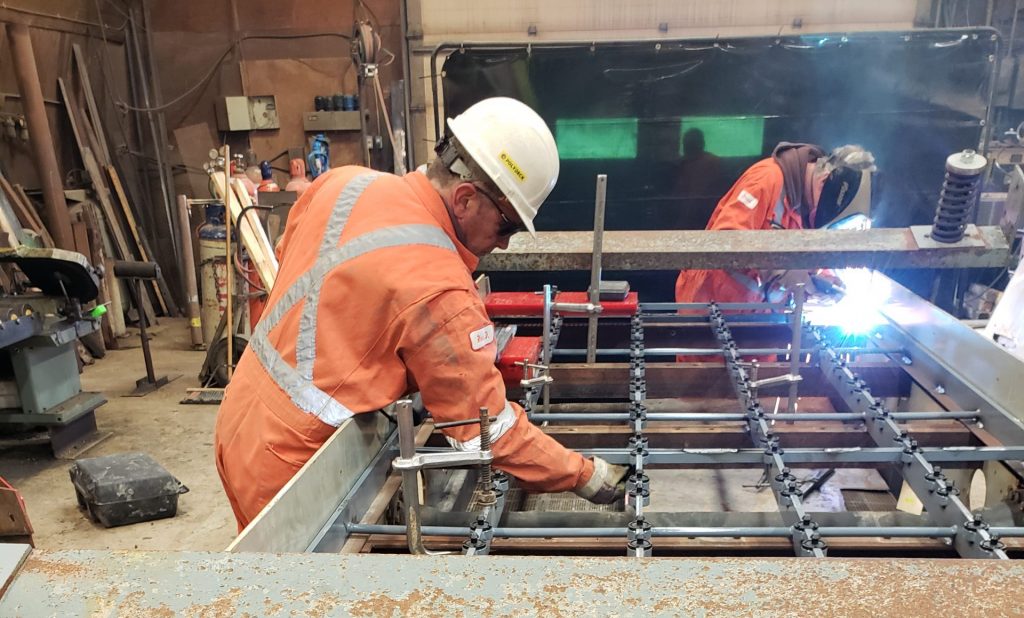
El mayor coste derivado de la sustitución de las rejillas era el tiempo de inactividad que suponía cambiar el material de las rejillas de 5 x 7 pies, lo que, según Giordano, costaba a su empresa entre una y tres horas de inactividad cada vez que había que sustituirlas. Así que, cuando Alex CaruanaCuando el Sr. Giordano, director territorial de Polydeck para Canadá Central y Atlántico, le explicó que la empresa podía ahorrar dinero y reducir el tiempo de inactividad en sus operaciones reequipando sus pantallas de lavado con un sistema modular de encaje a presión, Giordano quiso saber más.
"Alex trajo un diagrama e hizo un buen trabajo explicando lo que teníamos antes con la malla metálica y lo que podíamos tener con Polydeck", dice Giordano. "La mayor pega de goma y poliuretano es que no tiene suficiente superficie abierta como la malla metálica, pero él demostró que no se perdía ninguna superficie abierta".
Caruana demostró a Giordano que no perdería ninguna zona abierta utilizando un método muy simple, pero eficaz.
"Lo que suelo hacer para una planta cuando se plantean una o varias cubiertas es muy sencillo. Cierro, salto a la pantalla o hago una foto y me limito a contar las aberturas. Sé lo grandes que son las aberturas, porque las he medido, y eso también me permite tener en cuenta cualquier obstrucción, como barras diagonales, rieles de sujeción laterales, desviadores, pernos y otras cosas por el estilo. Eso me permite mostrar al cliente que con su tela metálica actual tiene 'X' superficie abierta, sea lo que sea 'X'", explica Caruana. "Y luego, puedo mostrarles que en su aplicación, usando nuestros medios, su área abierta sería ahora "X+", y ese es su nuevo número de área abierta".
En muchos casos, esta comparación abre los ojos a los productores.
"Incluso con tela metálica, puede que no tuvieran toda la zona abierta que pensaban que tenían", explica Caruana. "Imagínese un trozo de malla delante de usted. No tiene obstáculos y su superficie abierta catalogada, o valor contable, podría ser 65%. Parece muy atractiva. Pero cuando lo colocas en su sitio, hay piezas de maquinaria debajo. Así que no tienes 65%, sino 48%. En cambio, el material sintético no es lo mismo. Cuando el material sintético da un área abierta, ese es el número bruto y neto. Cuando se instala, sigue teniendo esa superficie abierta. Si alguien te dice que tienes 48%, ese es el número instalado. Así que, al hacer yo esa comparación para gente como Victor en Vicdom, tienen esa información a su disposición y pueden hacer una selección más educada".
Vicdom decidió cambiar una de sus cubiertas de lavado por un sistema modular a presión utilizando paneles de poliuretano Polydeck de 1' x 1' con aberturas cuadradas de 1/2" en la cubierta superior y aberturas de 1/4" en la inferior. Giordano quedó impresionado con los resultados.
"Este año hemos cambiado dos paneles en total", explica. "Normalmente habríamos cambiado cinco o seis pantallas enteras. En cambio, cambiamos dos paneles que costaban $90 canadienses cada uno por $180 en un año. La eficiencia es buena, la capacidad es buena y el tiempo de inactividad es asombroso".
Vicdom ha equipado ahora las cuatro cubiertas de sus dos pantallas de lavado con el sistema modular de encaje a presión de Polydeck utilizando paneles de poliuretano de 1' x 1'. La segunda pantalla de lavado tiene aberturas de 5/8" en la cubierta superior y de 1/4" en la inferior.
La reducción del tiempo de inactividad por cambio de soportes de pantalla no es la única razón por la que Vicdom disfruta trabajando con Polydeck. Giordano afirma que el nivel de profesionalidad de Caruana ha sido un gran argumento de venta, ya que siempre está disponible para ayudar con cualquier problema que surja in situ.
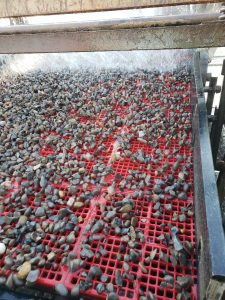
La empresa tuvo un problema de tramitación el año pasado con la primera conversión, así que llamaron a Caruana para tratar el asunto.
"Me preguntó: '¿Estás seguro de que tus excéntricas van cuesta abajo?". recuerda Giordano.
Así pues, Giordano consultó a su equipo de mantenimiento y resultó que ese mismo día habían realizado un trabajo previo y habían recableado accidentalmente el motor al revés en la pantalla, provocando que las excéntricas funcionaran cuesta arriba.
"Arreglamos el cableado, sacamos la piedra y volvió a funcionar. Con sus conocimientos, pudimos solucionar el problema enseguida", dice Giordano, y añade que aprecia mucho los conocimientos técnicos que Caruana aporta a la obra. "No veo a un vendedor. Veo a un tipo con mucha experiencia en boxes ahora en ventas, y eso ayuda."
¿Está pensando en reconvertirse?
Polydeck cuenta con un equipo de profesionales y más de 40 años de experiencia para ayudarle a optimizar el rendimiento de su tamiz minimizando los tiempos de inactividad.
"Se pierde superficie abierta al cambiar de tela metálica a material sintético."
Muchos operadores de instalaciones siguen creyendo que si se cambia de telas metálicas a pantallas modulares de medios sintéticos, se se perder área abierta en su cubierta. Sin embargo, a medida que más productores prueban los medios sintéticos, disfrutan de un mayor rendimiento y tiempo de actividad con la máxima superficie abierta y una mayor vida útil, lo que demuestra que esta idea es un mito.
Un ejemplo
Compañía de materiales Winter Brothers es una empresa familiar dedicada a la extracción de arena y grava que lleva 70 años abasteciendo las necesidades de áridos de la zona de San Luis. Los dos hermanos fundadores, George "Pete" Winter y Robert A. Winter dirigieron excursiones fluviales en la región durante la década de 1930 y, tras servir en la Segunda Guerra Mundial, regresaron a la zona y fundaron la empresa en 1946.
Situada en el río Meramec, afluente del Mississippi, Winter Brothers explota un yacimiento aluvial con una forma, uniformidad y pureza de partículas únicas. "Nuestra región ha sido bendecida con la disponibilidad de grava de calidad uniforme y arena sin lignito depositada por la naturaleza en este valle fluvial", afirma Ryan Winter, miembro del equipo directivo de Winter Brothers.
Más del 70% de los productos de la empresa se utilizan en la industria del premezclado y funcionan bien en diversas mezclas de cemento Portland. Los productos también se destinan a las industrias de tejados, albañilería, asfalto, paisajismo, sistemas sépticos y pozos de extracción.
El desafío
En su planta de Hagemann, los principales circuitos de cribado de la instalación producen seis tamaños diferentes de áridos gruesos junto con dos tamaños de productos de arena. "Desde que abrimos la planta, siempre habíamos utilizado tela metálica en todas las cubiertas de cada circuito de cribado", afirma Winter, quien admite que su equipo directivo se había resistido durante mucho tiempo al uso de medios sintéticos debido a la preocupación por la pérdida de superficie abierta y la disminución de la capacidad de producción.
Algo que no habían tenido en cuenta era la cantidad de superficie abierta que perdían debido al pegado y cegado del material. Los paneles de tela metálica que utilizaban se anunciaban como de "máxima" superficie abierta, pero, como cuenta Winter, "se cegaban en el primer par de semanas y perdíamos un porcentaje significativo de rendimiento."
También surgieron problemas con el tiempo de inactividad debido al mantenimiento de las cribas durante los periodos de mayor actividad, cuando la planta aumenta la producción. Cada una de sus cubiertas utilizaba cinco láminas de tela metálica de 4 por 8 pies, por lo que Winter recuerda que se trataba de un problema crítico para él.
"Cuando una de esas cribas reventaba, teníamos que parar todo, sacar a los trabajadores de otros trabajos, traer una grúa, cambiar las cribas... Todo eso nos quitaba varias horas del día de producción cada vez que ocurría". Además, cada vez que una criba de tela metálica se agujereaba, caía material de gran tamaño y contaminaba las reservas de producto.
Así que Winter, junto con el superintendente de planta Steve Klahs -un veterano del sector con 30 años de experiencia-, empezaron a estudiar detenidamente los soportes sintéticos porque querían comprender mejor las ventajas y los inconvenientes del cambio. Afortunadamente, pidieron consejo a Polydeck.
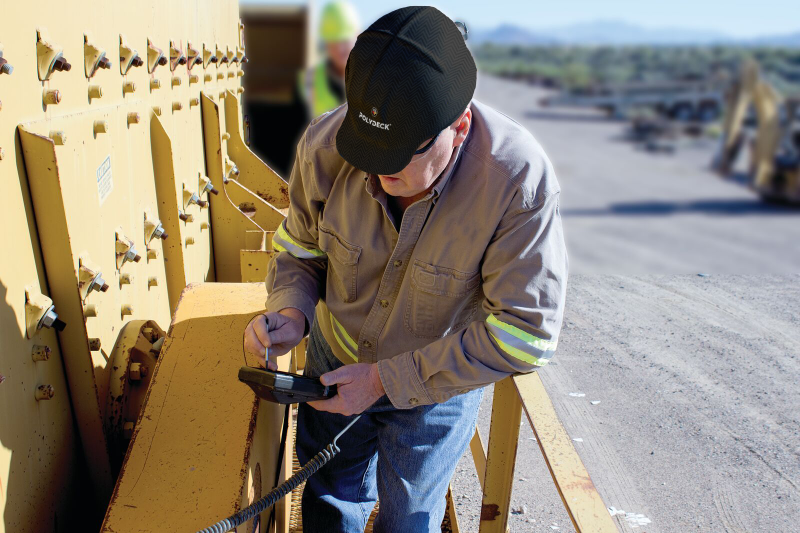
Evaluación
Después de hablar con varios fabricantes de soportes sintéticos, Winter dice que eligió Polydeck por nuestra experiencia y profesionalidad, y por su sólida relación con el distribuidor local de Polydeck, CT Fike Co.
"Dan Fike fue muy proactivo", explica Winter. "Trajo a miembros clave del equipo de Polydeck para que examinaran de cerca nuestros procesos y pudieran especificar los tipos de paneles adecuados para nuestras aplicaciones y gradaciones."
Joe TeagueVicepresidente de Ventas de Polydeck, pero que en aquel momento ocupaba el cargo de Director Regional de Ventas de Polydeck, trabajó en estrecha colaboración con el equipo directivo de Winter Brothers. Les demostró que su preocupación por la pérdida de superficie abierta radica en cómo se suele definir y calcular la "superficie abierta".
"Los porcentajes de área abierta publicados dan lugar a errores de cálculo a la hora de especificar el área de cribado y el tamaño de criba vibratoria necesarios para una aplicación determinada", explica Teague. "Muchos catálogos de telas metálicas indican porcentajes de área abierta que figuran en todos las aberturas de una sección de pantalla. Sin embargo, en el momento de la instalación, parte de esas aberturas quedan bloqueadas por las barras de refuerzo, la goma de la corona, los raíles de sujeción y las sujeciones centrales. Esto significa que el área abierta es significativamente menor, lo que hace que los cálculos sean erróneos hasta en un 40% o más".
En el caso de muchas marcas de soportes sintéticos, la superficie abierta suele calcularse simplemente ignorando el borde. "El panel tradicional tiene un gran borde o área "muerta" alrededor del perímetro que a menudo no se tiene en cuenta", dice Teague. "Así que, de nuevo, eso significa que el porcentaje de área abierta es exagerado para estos productos".
Teague mostró a la dirección de Winter Brothers que cuando las empresas de ingeniería y los usuarios finales utilizan estos cálculos inexactos del área abierta en su software de análisis del flujo de la planta, ésta puede diseñarse con cribas vibratorias de tamaño insuficiente o excesivo.
El consejo que les dio Teague fue toda una revelación: El área abierta debe calcularse tomando el número total de aberturas en el panel de la pantalla, y determinando el porcentaje de actual agujeros abiertos frente al completa superficie del propio panel. Sugirió que Winter Brothers adoptara un enfoque muy básico para comparar la superficie abierta entre dos fabricantes, contando simplemente el número de agujeros de cada panel de pantalla.
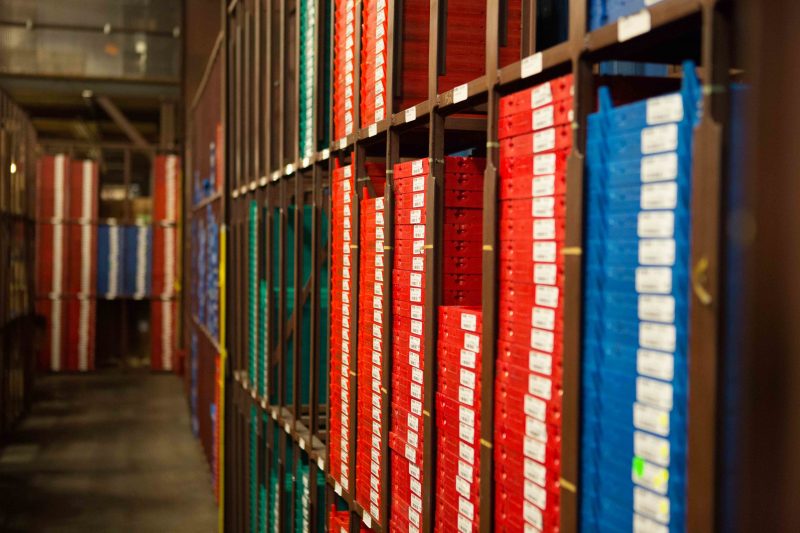
La solución
El objetivo era asegurarse de que el circuito siguiera el ritmo de la parte de trituración, por lo que el enfoque de Polydeck comenzó por adaptar correctamente los medios a los parámetros de la criba vibratoria, seleccionando de nuestra biblioteca de más de 1.500 opciones de diseño de paneles de criba.
Revisamos todas las mezclas de productos para identificar posibles incoherencias de gradación y cuellos de botella en la planta, y realizar los ajustes necesarios. Una vez recopiladas las estadísticas de procesamiento más importantes, ejecutamos escenarios hipotéticos para optimizar las especificaciones de los medios en función de las aplicaciones de Winter Brothers y determinar cómo afectaría a la eficiencia general cualquier cambio en las variables de las operaciones de cribado.
Según Winter, "Polydeck garantizado que sus configuraciones de paneles nos permitirían cumplir las especificaciones exigidas. De no ser así, realizarían los cambios necesarios. a su costa. Eso nos dio mucha confianza a la hora de cambiar tantos mazos a medios sintéticos."
Al final de la evaluación, Winter Brothers tomó la decisión de instalar Polydeck. paneles modulares de poliuretano.
Los resultados hablan por sí solos
Desde la instalación de los medios sintéticos, Winter Brothers ha cumplido sistemáticamente las especificaciones del sector.
"Desde que hicimos el cambio, sólo hemos tenido que sustituir algunos paneles en las zonas de impacto. Estamos muy contentos con el aumento de la vida útil del poliuretano porque, cuando utilizábamos tela metálica en esas cubiertas, cambiábamos una o dos pantallas cada semana", afirma Klahs.
Aunque Klahs pensaba que el cambio de las cribas de alambre reduciría la producción, ahora reconoce que el uso de medios sintéticos está ahorrando tiempo y dinero. "Estamos viendo un aumento increíble de la producción, casi el doble, sobre todo en la arena fina", afirma. "Además, el área abierta de los paneles de poliuretano nos proporciona un rendimiento excelente. Estamos especialmente impresionados por el área abierta que obtenemos en nuestro procesamiento de arena para mampostería."
Para Ryan Winter, la durabilidad y el consiguiente ahorro de costes de mano de obra que supone el uso de paneles de poliuretano es el principal argumento de venta. Nuestro material es muy duro", explica. "Mientras que la piedra caliza típica tiene una dureza de 3 a 4 en la escala MOHS, nuestra arena y grava tiene una dureza de 7 a 8. Por tanto, aunque el rendimiento y la superficie abierta son importantes, la durabilidad es fundamental". Así que, aunque el rendimiento y la superficie abierta son importantes, la durabilidad es fundamental".
"Estamos muy satisfechos con los años de vida útil que estamos obteniendo de estos paneles, y el personal de mantenimiento puede detectar cualquier problema de desgaste antes de que se convierta en un tiempo de inactividad o en un problema de contaminación. Si los muestreos de control de calidad son ligeramente erróneos, el personal de mantenimiento sabe que debe comprobar si hay desgaste. Si tienen que sustituir un panel, sólo necesitan unos minutos para retirar la rejilla desgastada y colocar una nueva".
"A veces las empresas se quedan con los métodos de siempre porque es la forma en que siempre han hecho las cosas", admite Winter. "Por eso nos quedamos con la tela metálica durante tanto tiempo. Pero al final hicimos el cambio a los soportes sintéticos de Polydeck y nos alegramos de haberlo hecho."
Mito... ¡destruido!
La nueva solución de medios de cribado de Polydeck maximiza el rendimiento y la mezcla de productos.
Aggregate Industries (AIUS) se ha convertido en una de las mayores empresas de materiales de construcción de EE.UU. gracias a su estrategia de sostenibilidad, gestión medioambiental y relaciones a largo plazo con los clientes. La cantera Morrison de la empresa -una explotación de granito de 3 millones de toneladas anuales situada en el condado de Jefferson, Colorado- ilustra perfectamente su misión.
El condado de Jefferson es uno de los tres condados de la región de Denver, formada por seis condados, dentro de la Región Centro-Oeste de AIUS que ofrece fuentes disponibles de piedra triturada. Dado que muchos de los recursos potenciales de áridos de la zona de Denver no son accesibles para su extracción, la cantera Morrison desempeña un papel fundamental para satisfacer la demanda de materiales áridos de alta calidad de la región.
Director de la planta de Morrison, Trulane Vanatta dirige una planta de "productos agotados", lo que significa que todo lo que se procesa en un día determinado se vende al día siguiente. Para él, explica sin rodeos, "El rendimiento lo es todo."
Como resultado, la planta mantiene un enfoque constante en la mejora de la eficiencia del procesamiento y la capacidad de producción. Para eliminar los cuellos de botella en los circuitos de cribado, el equipo directivo de Morrison se puso en contacto con los expertos en ingeniería de Polydeck.
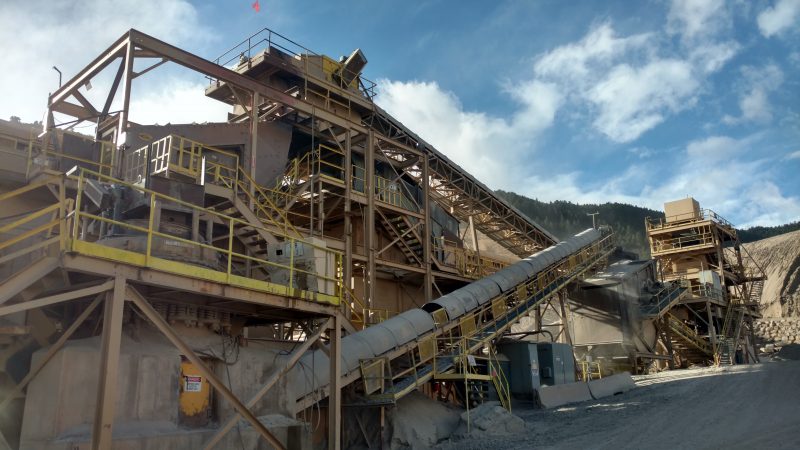
Reducción de las cargas de recirculación y las multas
El equipo de Vanatta detectó un problema en el circuito terciario de la planta de nueve cribas. Sus muestras de cinta indicaban una elevada profundidad de lecho en las cubiertas centrales de las tres cribas del circuito. Cada una de las cribas de tres pisos de 8 por 20 pies es clave para la producción del material #57/#67 (1 pulgada) de Morrison.
"Esa es nuestra máquina de hacer dinero; y tenemos que maximizar su volumen de produccióndice Vanatta.
Su equipo detectó un "preocupante" arrastre de 51%, un cuello de botella que provocaba cargas recirculantes y producía un exceso de finos, un problema de producción habitual. "Lo primero que se nos ocurrió fue sustituir las cubiertas intermedias de dos de las cribas terciarias por tela metálica para conseguir más superficie abierta.recuerda Vanatta.
Pero resulta que el Director Regional de Polydeck, Sam DurnavichSam fue subdirector de planta en la cantera Morrison hace más de una década, antes de unirse a la organización Polydeck. Con su conocimiento de la operación, Sam consultó con la dirección de Morrison y trabajó estrechamente con el equipo de ingeniería de Polydeck para crear una solución de medios que abordara con mayor eficacia su desafío de arrastre.
Tras un análisis exhaustivo del funcionamiento de Morrison, el equipo de producción de Polydeck diseñó e instaló un producto totalmente nuevo: DMAX™ un sistema de cribado sintético de área ultraabierta que aumenta significativamente el rendimiento y permite a la cantera incrementar la producción de sus productos de mayor valor.
Los nuevos paneles de cribado DMAX de Polydeck están pensados para su uso cuando el área abierta y el rendimiento son las consideraciones más importantes. Se trata de una solución de paneles de cribado sintéticos modulares que igualan o incluso superan la superficie abierta de la tela metálica, al tiempo que ofrecen una mayor vida útil y una instalación más sencilla. El sistema de paneles de cribado DMAX también puede formularse con caucho o poliuretano en función de la aplicación.
Superar los objetivos de producción
Desde la instalación del primer DMAX Gracias a la instalación de paneles de cribado en dos de los pisos intermedios en octubre de 2015, la empresa ha alcanzado sus objetivos de producción y, con frecuencia, los supera. También han logrado una eficiencia de cribado mucho mayor, según Vanatta: casi 54% de área abierta en sus cubiertas intermedias, en comparación con las 42% de área abierta que ofrecía su cubierta de cribado anterior. Esto supone un aumento espectacular de 28,5% de superficie abierta. Morrison instaló posteriormente paneles DMAX en una tercera cubierta intermedia a mediados de 2016.
"Para nosotrosdice Vanatta".El aumento de la superficie abierta se tradujo en un incremento de 11% en la producción de roca rentable de 1 pulgada, y redujo los finos en casi 1%. La única desventaja de la superficie abierta es que los paneles se desgastan un poco más rápido, pero eso es esencialmente irrelevante, ya que el beneficio del aumento de tonelaje amortiza la inversión en medios de cribado más de diez veces.."
La cantera Morrison también emplea paneles de criba modulares Rubberdex® de Polydeck en las cubiertas superior e inferior de sus cribas terciarias de 8 por 20 pies.
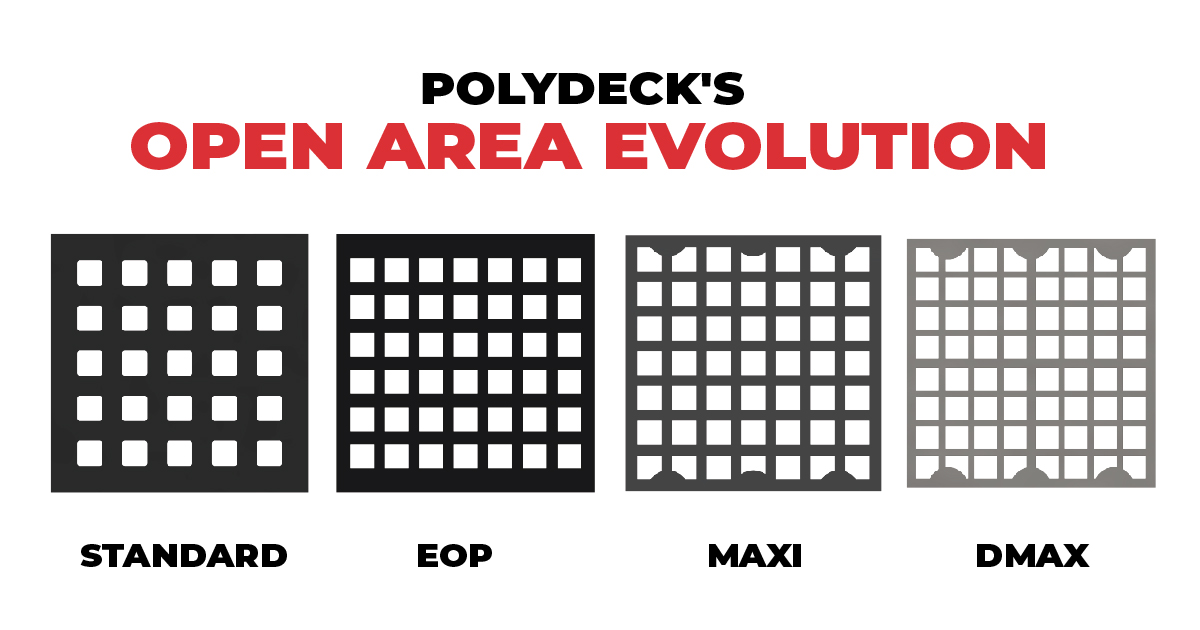
Experiencia en ingeniería
Explica Sam Durnavich, de Polydeck, "Hemos fabricado los paneles DMax con puentes que tienen la mitad de anchura que los de nuestro panel maxi estándar, pero mucho más profundos. Esto es importante, porque la reducción de la anchura del puente entre aberturas permite más aberturas en la superficie del panel de pantalla, lo que se traduce en un mayor paso del producto.."
"A la superficie abierta adicional contribuye el hecho de que los paneles DMax están diseñados para encajar en los sistemas de largueros Polydeck PipeTop II existentes.continúa Durnavich. "Este sistema de armazón presenta raíles de fijación exclusivos de media pulgada de ancho en lugar de los estilos de montaje de los sistemas de armazón convencionales con hasta 3 pulgadas de espacio muerto donde se acumulan las multas. Además, nuestra capacidad de utillaje interno nos permite ofrecer muchas más opciones en estos sistemas de armazón, desde diferentes opciones de fijación, opciones de materiales y estilos y tipos de largueros.."
"El aumento de la superficie abierta hace vienen con una reducción de la vida útil del panel de la pantalla", admite Durnavich.Sin embargo, si se comparan con los paneles de criba de uso estándar, los paneles DMax sólo tienen una vida útil 20-25% inferior, que sigue siendo superior a la de las telas metálicas.."
"Nuestro uso del moldeo por inyección es un factor importante en la capacidad de crear paneles sintéticos de superficie abierta extrema.añade Durnavich. "El moldeo por inyección garantiza que todos los paneles de pantalla tengan tamaños y formas de abertura precisos y estén completamente curados.."
"Nuestros resultados reales en varias aplicaciones han demostrado aumentos de producción de hasta 50% y aumentos de la eficacia de cribado de más de 25%.dice Durnavich con una sonrisa.
Polydeck sigue ampliando la gama de aberturas disponibles en la serie DMax, con aberturas cuadradas de 12,5 mm a 32 mm, así como aberturas ranuradas de 3x20 mm a 25x74 mm.
Se suele decir: Si hay un cuello de botella en una planta, probablemente esté en el circuito de cribado. En la cantera Morrison, el rendimiento lo es todo, por lo que aumentar continuamente la eficacia del cribado es esencial para mantener la rentabilidad y la calidad del producto. Trabajando juntos, la cantera Morrison y Polydeck resolvieron un problema inmediato y crearon una solución a largo plazo.
KWIKDECK es una forma sencilla y rentable de probar los medios modulares.
Medios de pantalla es un componente esencial para los sectores de los áridos, la energía, la industria y la minería. Durante décadas, las telas metálicas han sido el material preferido del sector, pero su instalación es engorrosa y no tan versátil como la de los materiales modulares. Si utiliza telas metálicas, probablemente esté acostumbrado a cambiarlas cada pocas semanas, una tarea que lleva mucho tiempo y a veces es peligrosa.
¿Y si sólo tuviera que sustituir los soportes de pantalla dos veces al año?
Polydeck KWIKDECK ofrece una solución mejor: Una conversión de marcos que le permite probar soportes de pantalla sintéticos prácticamente sin riesgos, con unos costes de instalación mínimos y una instalación sencilla.
KWIKDECK le ayuda a reducir los costes operativos, reduce el tiempo de inactividad al tiempo que mejora la seguridad y mantiene su equipo funcionando al máximo rendimiento.
¿Por qué KWIKDECK es una solución ideal?
- Es fácil de instalar - KWIKDECK tarda unos 45 minutos en cambiar una sección de 4 por 6 pies. Reutiliza los rieles de sujeción laterales existentes y no requiere alterar el marco del escritorio existente.
- Es adaptable - KWIKDECK funciona con cubiertas coronadas y puede modificarse para adaptarse a las dimensiones y configuraciones de la mayoría de las máquinas vibratorias.
- Es rentable - KWIKDECK le permite utilizar medios de pantalla sintéticos, que duran al menos diez veces más que las pantallas de alambre,[1] y requieren menos mantenimiento y menos cambios que las de alambre.
KWIKDECK también es perfecto para operaciones de cribado portátiles que necesitan alternar entre tela metálica y medios sintéticos. Los operarios pueden alternar fácilmente entre distintos tipos de medios para maximizar los requisitos de producción.
KWIKDECK ofrece a los usuarios de telas metálicas tradicionales la oportunidad de probar los medios sintéticos con un coste o un riesgo mínimos. Instálelo en el extremo de alimentación de su criba vibratoria y compruebe usted mismo la diferencia que supone.
Más información KWIKDECKotro producto innovador de sus socios de Polydeck, y sólo un ejemplo más de cómo estamos juntos fuertes.
[1] http://www.pitandquarry.com/pq-university-lesson-8-screening/