É fácil ser complacente com soluções de mídia de tela que requerem tempo parado para limpeza e substituição. Melhore seu rendimento, reduza o tempo de parada e aumente a produção com a máxima área aberta e facilidade de uso dos Maxi Panels da Polydeck's.
Em uma indústria que data de dezenas de milhares de anos atrás, é fácil tornar-se complacente ao considerar fatores de sucesso e eficiências em sua operação. Entretanto, é mais do que possível projetar uma operação que seja eficiente e avançada com a mídia de tela certa. Polydeck's Maxi As soluções de tela de painel aumentam o rendimento de uma operação e a eficiência de produção de inúmeras maneiras.
O rendimento é, em poucas palavras, uma medida de produção e sucesso. Em termos de processamento de material, isso significa que sua mídia de tela está fazendo seu trabalho. Uma mídia de tela eficiente encontra suas máquinas onde elas estão, permite facilidade de limpeza e substituição, e proporciona a máxima peneiração do material com o mínimo de tempo parado possível. Para muitas operações, a eficiência é crítica, especialmente onde os recursos são limitados. Parar para limpar tampões e lidar com a baixa área aberta simplesmente não é uma opção quando a eficiência e a sustentabilidade são exigidas do local.
Se a mídia de tela não estiver funcionando como deveria, resultam paradas dispendiosas, exigindo que os trabalhadores passem horas limpando as tampas e levando as telas para um local onde possam recomeçar a produção. Cliente Polydeck Dufferin Aggregates Butler PitOntário, localizado em Cambridge, estava passando por um significativo período de paralisação devido à fixação de pinos. Com um foco constante em suas metas de eficiência e produção, a Dufferin não perdeu seu tempo buscando uma melhor solução de mídia de tela. Depois que a equipe da Polydeck conduziu uma análise de desempenho da tela no local e apresentou suas soluções com a garantia de que a Dufferin experimentaria sua produção desejada fazendo a troca, a escolha foi simples.

Maxi As bordas finas dos painéis são projetadas especificamente com a produtividade em mente, apresentando ângulos de relevo para ajudar na triagem adequada. Uma vez que os painéis foram colocados nas telas de nossos clientes, eles forneceram o número máximo de aberturas por pé quadrado. Além de oferecer taxas de rendimento líderes, os poliuretanos especialmente formulados da Maxi painéis, combinados com a geometria do painel projetada, permitiram que os painéis flexionassem e mantivessem vida útil prolongada. Este design inovador aliado ao processo de moldagem por injeção da Polydeck garantiu uma área aberta precisa e consistente que resultou em maior eficiência geral no Butler Pit.
Maxi Os painéis também oferecem uma vantagem sobre a tela metálica quando se considera a resistência à abrasão dos meios de tela sintética e a facilidade de uso. As operações muitas vezes são padronizadas para telas metálicas quando os requisitos de produção são altos, mas os painéis Maxi oferecem um custo benefício significativo quando se considera o tempo de parada necessário para trocar as telas metálicas. A modularidade dos painéis Maxi e os fechos de encaixe facilitam e aceleram as trocas. Menos tempo de parada significa mais horas produtivas no local. Mais produção significa mais retorno de seu local de produção. Em resumo, adicionar os painéis Maxi da Polydeck à sua operação significa que você receberá mais de sua fábrica do que nunca.
As chaves para o sucesso com a mídia de tela estão na tecnologia atual e na eficiência encontrada na Polydeck's Maxi painéis. Como visto nas instalações de nossos clientes, os painéis Maxi da Polydeck's reduziram o tempo de parada e aumentaram a produção, dois elementos muito críticos para o sucesso em qualquer operação.
Você está pronto para aumentar o sucesso de sua operação?
Quando você elimina os gargalos do convés superior, você aumenta a capacidade de produção e coloca mais produto vendável no chão. Leia sobre como a Polydeck ajudou com um maior nível de eficiência de forma econômica.
Se você estiver administrando uma planta agregada, então você sabe que o eficiência de suas telas de decks superiores é fundamental para o desempenho geral de sua operação. É uma fórmula simples: Quando você elimina os gargalos do convés superior, você aumenta a capacidade de produção e coloca mais produtos vendáveis no chão. Mas como os operadores podem atingir esse nível de eficiência de uma maneira econômica?
A resposta de Polydeck a esta pergunta é uma equação de tela de mídia que combina painéis modulares de tela com fio soldado com painéis de mídia sintética. Cada tipo de painel modular é posicionado estrategicamente no convés superior para proporcionar máxima área aberta e vida útil superior. Para os operadores, o resultado é maior rendimento e menor tempo de parada para manutenção = mais lucro e menos despesas.
Parceiro da Polydeck, Recursos AlleytonA TX, é uma produtora de agregados e concreto pronto, com sede em Houston, TX. Suas operações incluem 11 locais RMC e oito locais de processamento de agregados, e fornecem transporte de material, entrega de concreto pronto, bombeamento de concreto e areia e polpa estabilizada para seus clientes.
Brandon Genzer (gerente da fábrica de Vox da Alleyton em Garwood, TX, na época) estava lidando com depósitos grosseiros no local, bem como com dificuldades para desocupar o convés superior de sua tela de acabamento secundário úmido e inclinado, que estava equipada com meios de poliuretano.
"A tela está sendo alimentada com material de 2-1/2", explica ele, "Tivemos uma grande transferência de material de 1-1/2", o que criou cargas de recirculação desnecessárias voltando para o triturador".
Este foi um enorme problema para sua operação porque a recirculação de cargas aumenta significativamente tanto o desgaste do britador quanto os custos operacionais por tonelada. Estava se esvaziando as margens de lucro da instalação ao enviar o produto acabado de volta para o triturador em vez de para o estoque de produtos comercializáveis.

Para eliminar este dispendioso problema de transporte, a Genzer consultou o gerente da Polydeck para a região do Sul do Texas na época, Kent Ropp. "Trabalho em estreita colaboração com cada produtor de minha área para analisar sua aplicação e criar configurações modulares de painéis de tela que fornecem as especificações desejadas".
A Ropp trabalhou com a Genzer para especificar as novas mídias, conduzindo várias horas de tempo de execução para cada amostra de material. "Nós ligaríamos diferentes mídias para discar em nosso módulo FM [fineness modulus] exatamente onde precisávamos", recorda Genzer.
A Ropp acabou recomendando uma combinação de produtos de alto desempenho da Polydeck. Para maior área aberta e rendimento, os produtos Polydeck's METALDEX™ painéis de mídia de tela de aço modular foram instalados na extremidade de descarga da instalação de 6 pés. x tela de 16 pés. Para absorver o impacto na extremidade de alimentação da tela, RUBBBERDEX®. painéis de borracha sintética foram instalados para uma vida útil máxima no convés superior. Os decks médio e inferior foram equipados com POLYDEX®. painéis modulares de tela de poliuretano.

O METALDEX™ Os painéis oferecem uma área aberta que iguala ou supera a tradicional tela metálica com a mesma abertura e diâmetro de arame. Além da maior área aberta, a modularidade dos painéis permite que as operações os apliquem na extremidade de alimentação ou, mais importante, na extremidade de descarga, onde o aumento da área aberta é crítico para eliminar cargas recirculantes.
Testes realizados pela Ropp na fábrica Vox determinaram que a adição de painéis Metaldex à extremidade de descarga aumentou o desempenho da tela para 55,9% de área aberta sobre a classificação 33,4% que eles alcançaram com os painéis de borracha sintética anteriores.

"Estamos obtendo um bom desgaste também nos painéis", relata Genzer, "Mesmo em turnos prolongados de 12 a 16 horas, o primeiro conjunto durou mais de quatro meses". Quando estendemos as horas, verificamos as telas no final de cada turno. Se necessário, a tripulação pode trocar os painéis em questão de minutos, e estamos de volta ao funcionamento".
De acordo com a Ropp, a chave para a maior vida útil da METALDEX é que: "Ele é composto de aço Brinell AR 500 resistente à abrasão, o que prolonga a vida útil na maioria das aplicações contra a das telas metálicas padrão. O arame soldado simplesmente proporciona um maior grau de desempenho em resistência e resistência à corrosão".
Outro bônus para a fábrica Vox é que a METALDEX™ painéis esfregam melhor o material, removendo o conteúdo de argila. "Estamos obtendo o melhor dos dois mundos, agora rochas mais limpas com um rendimento maior", diz Genzer, acrescentando que a média da planta é de 550 toneladas por hora, um aumento significativo desde que o circuito de peneiramento foi aperfeiçoado. A Alleyton implementou desde então um METALDEX™ em outra operação para ajudar a quebrar e eliminar o conteúdo de argila em seu material.
Como a flexibilidade de processamento é importante nas instalações da Vox - que produz principalmente material de 1-1/2", material de 3/8" e areia de concreto - a modularidade dos painéis de tela lhes permite mudar facilmente os painéis ou afinar as configurações para acomodar diferentes alimentações de material ou requisitos de processamento. As bordas de cada painel de arame soldado de 1 x 2 pés são revestidas também de poliuretano, tornando-as muito mais fáceis de manusear do que grandes seções de tela metálica.
"METALDEX™ é outro projeto inovador de painel de tela da Polydeck que aumenta a gama de soluções de mídia de tela e ajuda nossos clientes a superar suas metas de produção", diz a Ropp. "Ela oferece a vida útil prolongada do aço resistente à abrasão com a área aberta da tela metálica, e a engenharia modular permite o fácil manuseio e a fixação simples ao sistema de estrutura de stringer da Polydeck".
A eliminação de gargalos de peneiramento é essencial para maximizar a produtividade no peneiramento de decks superiores, o que, por sua vez, é crítico para o desempenho ideal da planta. Na fábrica Vox da Alleyton Resources, a combinação inovadora de arame soldado e painéis de mídia sintética da Polydeck foi a fórmula precisa para resolver seus problemas de peneiramento.

Em 2020, a Polydeck lançou uma nova oferta de produtos - METALDEX™ VR. A nova solução modular de tela metálica da Polydeck integra-se com nosso PIPETOP™ sistema stringer. Perfeito para aplicações de dimensionamento a seco onde mais área aberta e eficiência é necessária, METALDEX™ O VR é idealmente instalado na extremidade de descarga, onde proporciona maior vida útil e melhor rendimento, e seu padrão único, em forma de diamante, elimina o cegamento e o entupimento.
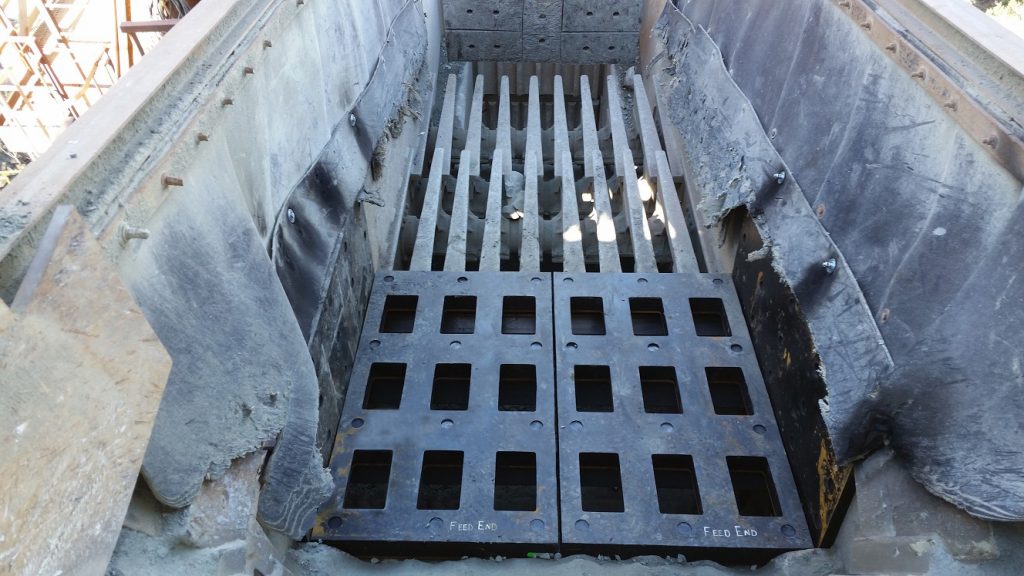
O escalpe eficiente é essencial para o ótimo desempenho dos circuitos de britagem primária e secundária. Para aumentar a eficiência do escalpamento, a operação Hanson instalou ARMADEX seções de borracha personalizadas para o segundo passo - com o terceiro passo a ser seguido em breve.
Muito simplesmente, a capacidade de produção e a vida útil aumentam quando os finos são removidos da alimentação primária da mandíbula; quando os excessos são alimentados até a mandíbula; e quando o material dimensionado abaixo da configuração do britador de mandíbulas passa através das barras pardo para mais trituração e dimensionamento.
Entretanto, em aplicações extremamente abrasivas, de alto impacto e de alto desgaste, atingir a eficiência ótima de escalpelização pode ser um desafio.
Solução de problemas
Para reduzir os custos operacionais por tonelada enquanto atendia a demanda do mercado por asfalto de alta qualidade e agregado de concreto, a Pedreira Clayton da Lehigh Hanson, sediada na Califórnia, procurou eliminar quaisquer gargalos existentes ou potenciais em toda a sua planta. Servindo a região da Baía de São Francisco, a Pedreira Clayton é um dos 200 locais de produção de agregados e terminais de distribuição de propriedade da Hanson, que produz agregados, asfalto, concreto pronto e outros materiais de construção em toda a América do Norte.
"Nossa mina é uma pedreira de perfuração e jateamento de rocha dura que foi iniciada em 1956", diz Marc McNeil, gerente da fábrica da Pedreira Clayton. "Desde o final dos anos 90, nosso foco mudou gradualmente da produção de rochas básicas para a produção de pedra britada e areia fabricada, e nossa planta de envelhecimento exigiu algumas atualizações desde a alimentação inicial até o acabamento do produto".
Marc McNeil, gerente da fábrica em Lehigh HansonA Pedreira Clayton, supervisiona as atualizações atuais da fábrica, desde a alimentação inicial até o acabamento do produto.
As melhorias começaram por enfrentar os desafios de escalpelização e dimensionamento. A aplicação dura e de alto impacto da Pedreira Clayton em escalpes de rocha envolveu desgaste extremo, bem como custos de manutenção e mão-de-obra excessivos para substituir e reparar barras pardas desgastadas.
Por fim, a Pedreira Clayton escolheu uma solução de escalpagem personalizada, projetada e fabricada pela Polydeck. ARMADEX é um produto personalizado de peneiramento de borracha que foi aplicado em seções parafusadas no primeiro degrau (5 pés) do alimentador pardo vibratório da planta.
"Desde a instalação do ARMADEX, reduzimos significativamente o tempo de parada de manutenção e os custos de desgaste - ao ponto de eventualmente aplicarmos o ARMADEX à segunda etapa do pardo, com planos de instalação na terceira etapa atualmente em andamento", diz McNeil.
Desafios de escalada de alto impacto
A Pedreira Clayton minera uma rocha diabólica que é içada para a planta de britagem primária e carregada em uma tremonha de 150 toneladas.
Para reduzir o tempo de parada de manutenção e os custos de desgaste, um produto de peneiramento de borracha personalizado, ARMADEXA primeira etapa do grizzly foi aplicada em seções aparafusadas.
Um alimentador de panela retira o material de 24" do funil e o alimenta até o pardo da etapa vibratória. O grizzly é altamente impactado, pois o material cai 12 pés antes de atingir as barras de grizzly. O impacto sobre a mídia de aço gerou um ruído considerável ao mesmo tempo em que fez com que a extremidade de alimentação do grizzly se desgastasse excessivamente.
Além disso, a alimentação fina do poço muitas vezes fez com que o primeiro conjunto de barras pardas passasse por cima.
"As barras são aparafusadas a uma barra de apoio, mas com a ponte e o desgaste excessivo, as barras começariam a se mover e a se abrir, permitindo a passagem de rochas maiores", diz McNeil. "Quando aquela rocha de tamanho excessivo passa para o circuito secundário, o triturador de cone se torna menos eficaz".
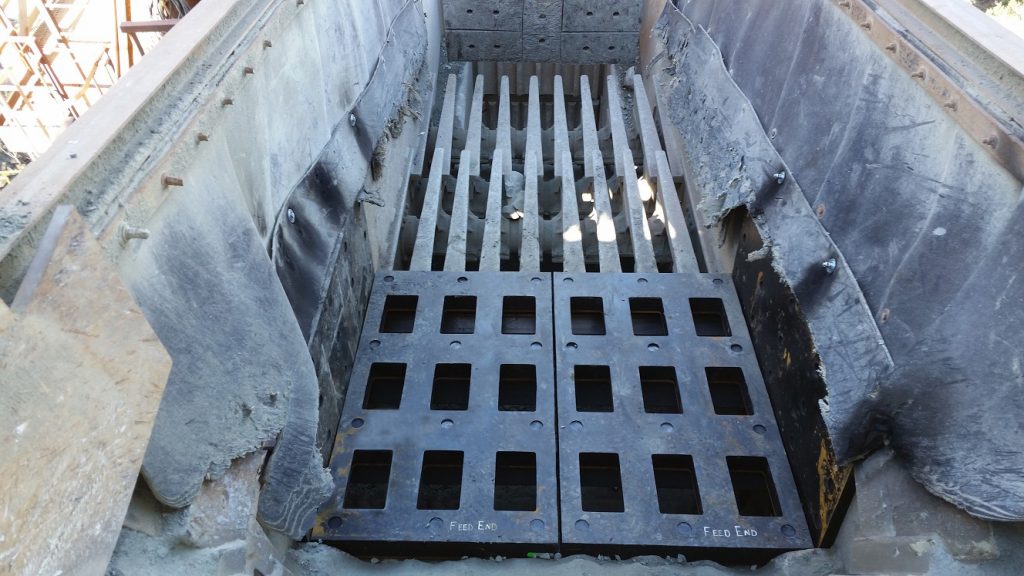
O mais importante, o tempo de parada de manutenção adicional e os custos de mão-de-obra entraram em jogo. O movimento das barras pardas exigia até 20 horas por semana de solda para fixá-las no lugar, diz McNeil.
"Para segurança, trabalhar em um pardo requer ser aproveitado", acrescenta ele. "Portanto, se um trabalhador está soldando barras regularmente, isso se torna um grande desafio". Tentamos substituir todo o conjunto de barras e isso foi muito caro. Tinha que haver outra maneira".
Soluções de escalonamento personalizadas
Em toda sua planta de acabamento, tanto em telas úmidas quanto secas, a Pedreira Clayton utiliza painéis de poliuretano sintético modular Polydeck e telas de mídia de borracha.
A Pedreira Clayton utiliza painéis modulares de poliuretano sintético e tela de borracha em toda a sua planta de acabamento, tanto em telas úmidas quanto em telas secas.
"Tivemos bons resultados com seus produtos de mídia de tela, então pedimos aos engenheiros de aplicação da Polydeck que avaliassem nosso circuito de escalpe para ver o que poderia ser feito", diz McNeil. "Eles propuseram o uso de ARMADEXA tecnologia de escalpe de topo, uma mídia altamente adequada para aplicações de escalpe resistentes e abrasivas no convés superior. Decidimos experimentar no primeiro passo do grizzly - e vimos benefícios imediatos na redução do tempo de parada de manutenção e dos custos de desgaste".
Como salienta Peter Babinski, da Polydeck, os produtores de agregados querem tempo máximo de atividade, manutenção mínima, aumento da vida útil e redução do ruído - particularmente em aplicações de alimentadores de pardo abrasivo. Os produtores freqüentemente buscam soluções de mídia sintética para esses benefícios, diz ele.
Como explica Babinski, a borracha ARMADEX utiliza a tecnologia de moldagem por injeção a alta pressão, um método de fabricação Polydeck que produz 10 vezes a pressão normalmente utilizada para produzir borracha moldada por compressão.
"A combinação desta tecnologia com nosso composto de borracha de goma premium e suporte de chapa de aço HSLA produz uma resistência sem precedentes em um produto de mídia que proporciona uma vida útil muito mais longa a custos mais baixos por tonelada", diz Babinski, que serve à Polydeck como gerente de território agregado da Costa Oeste/Estados de Montanha.
"Com barras pardas, as operações não podem ajustá-las a menos que as mudem completamente ou as solde para mudar as aberturas", diz Babinski. "As seções aparafusadas ARMADEX nos dão a flexibilidade de acessar aberturas menores ou maiores para afinar o desempenho em uma determinada aplicação".
Para instalar as seções ARMADEX no alimentador de grizzly na Pedreira Clayton, a Polydeck projetou uma estrutura personalizada que se aparafusa aos painéis laterais do grizzly. As seções ARMADEX são facilmente aparafusadas nessa estrutura.
"Foi um simples substituto para nós com muito pouco tempo parado, devido à atenção da Polydeck aos detalhes relativos à personalização de nossa aplicação", diz McNeil.
Eficiência em escalonamento e dimensionamento
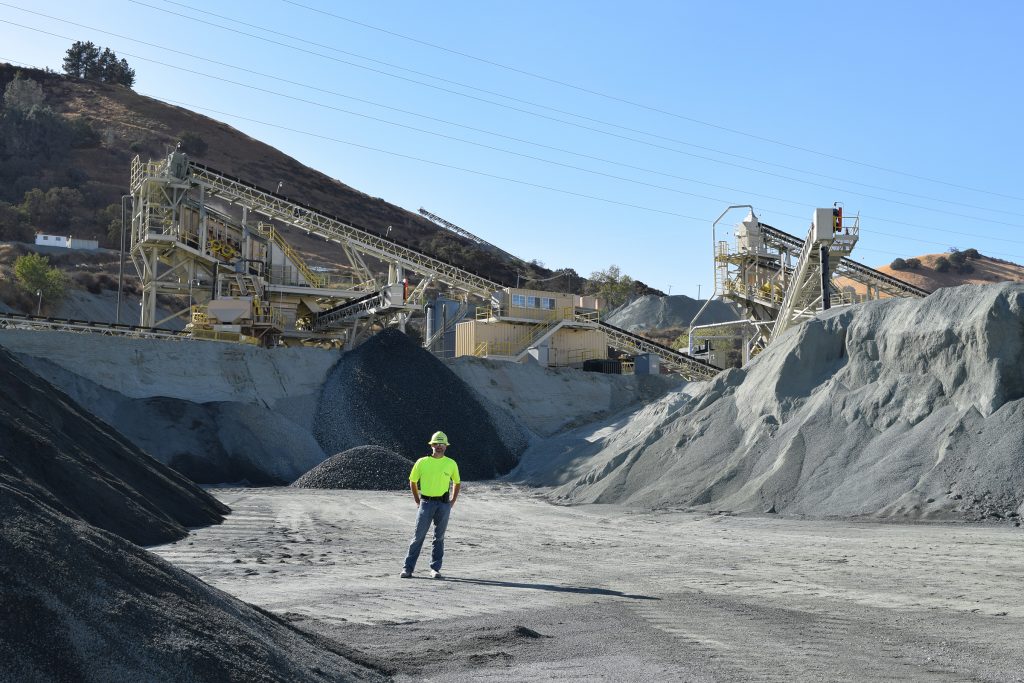
De acordo com McNeil, a operação melhorou muito a eficiência do dia-a-dia de escalonamento e dimensionamento, usando ARMADEX seções de mídia. Ao impedir a passagem de material de tamanho excessivo para o triturador de cone, a operação aumentou o desempenho de britagem enquanto reduzia o tempo de parada.
"Reduzimos drasticamente os custos de manutenção, pois ainda não mudamos uma seção ARMADEX desde sua instalação - e eles não precisam de soldagem semanal", diz McNeil, acrescentando que as seções de mídia na primeira etapa do grizzly processaram uma produção de material de quase 3 milhões de toneladas ao longo de três estações de produção.
A Pedreira Clayton continua a trabalhar com a Polydeck para aprimorar ainda mais o desempenho. O circuito de escalpe empregará aberturas redondas nas seções ARMADEX utilizadas na terceira etapa do alimentador pardo, aumentando a produção de rochas angulares que podem ficar encravadas em aberturas quadradas ou retangulares.
Ao ajustar os circuitos de escalonamento no topo da cadeia, aqueles que se seguem vêem menos desgaste, maior capacidade de produção e produtos mais vendáveis até as pilhas de estoque.
Escrito por Carol Wasson, veterana redatora freelancer para as indústrias de equipamentos agregados e de construção.
LafargeHolcimA empresa, líder mundial em materiais e soluções de construção, é um produtor ativo nos segmentos de negócios de Cimento, Agregados, Concreto Pronto-Mix e Soluções & Produtos das indústrias que a empresa atende. Como uma empresa cujo negócio está centrado no uso de materiais naturais, a LafargeHolcim tem plena consciência de suas responsabilidades a partir de uma perspectiva de sustentabilidade. Recentemente, a equipe de liderança da empresa tornou evidente que a sustentabilidade é um componente chave de sua estratégia de negócios e algo que eles estão avaliando ativamente em cada local com seus relatórios anuais. Considerando o impacto ambiental e de sustentabilidade de cada uma de suas operações e locais é fundamental para seu sucesso como uma empresa que depende de materiais naturais.
LafargeHolcim's WoodstockON, a pedreira canadense experimentou um grande avanço em sustentabilidade para a operação e a última palavra em produtividade de material utilizável graças à liderança da indústria Polydeck bico de pulverização tecnologia. A pedreira Woodstock estava anteriormente muito envolvida na extração e processamento do depósito de calcário, um material de construção chave. A operação historicamente se concentrava na jateamento, extração, trituração e peneiramento do calcário. Como uma planta de alimentação para uma fábrica de cimento próxima, a viabilidade operacional da jazida era clara. Entretanto, quando o mercado para o calcário mudou, a operação achou crítico adaptar-se às novas exigências do mercado.
A mudança do mercado resultou no fornecimento de mais pedras para asfalto e concreto. Quando a operação começou a se concentrar nestes materiais, começou a gerar finos. Na verdade, a equipe da pedreira Woodstock percebeu que estavam produzindo montanhas de finos. Como a cultura da empresa havia evoluído para considerar o impacto de cada operação e para inovar com relação à sustentabilidade, a lâmpada começou a se iluminar em Woodstock - os finos resultantes podiam ser processados em um material proprietário e utilizável. Embora o objetivo final parecesse claro, ainda havia alguma adaptação e criatividade que seria necessária. Foi aí que a equipe da Polydeck entrou para ajudar a fábrica a descobrir sua nova abordagem.
A LafargeHolcim sabia que as multas reprocessadas seriam altamente comercializáveis, e estavam certas. Tornou-se óbvio que os bicos pulverizadores Polydeck, projetados para lidar com lavagens pesadas, eram a resposta para adaptar os decks para criar um produto comercializável.
Enquanto um bico de pulverização parece ser um produto simples, o diabo está realmente nos detalhes. Quando a pedreira começou a procurar uma solução de lavagem, eles sabiam que precisavam do produto mais eficiente e durável do mercado. O ideal seria que os bicos pulverizadores tivessem a capacidade de fornecer água com a pressão e a geometria certas para produzir um efeito de lavagem que resultasse na separação e no rendimento adequados do material. Os bicos de pulverização Polydeck, instalados na máquina horizontal Simplicity 8x20 Triple Deck da LafargeHolcim no local, fizeram exatamente isso. Quando um bico de pulverização funciona corretamente, os materiais indesejáveis dimensionados e distribuídos são liberados e isolados como material utilizável.
A pedreira Woodstock começou a testar um processo de lavagem para extrair os finos usando tela metálica, que é um produto comum em uma operação de lavagem. No entanto, a manutenção e o tempo de trabalho da tela metálica logo se mostrou altamente ineficiente para a operação. O tempo gasto na troca da tela de arame foi o tempo não gasto na produção de material vendável.
Após perceber que a tela metálica era uma solução ineficiente, a LafargeHolcim recorreu mais uma vez à Polydeck e decidiu projetar uma fábrica para produzir o material proprietário. A Polydeck equipou todos os três decks da LafargeHolcim com mídia sintética bem como os bicos de pulverização. Os resultados foram surpreendentes. Adaptando-se a uma situação que apresentava um desafio extremamente estreito, os bicos de pulverização Polydeck não só se encaixaram, mas também executaram o trabalho com certeza. O material que antes resultava em desperdício estava agora sendo separado devido aos eficientes resultados de lavagem produzidos pela combinação dos bicos de pulverização Polydeck e da tela. Os bicos de pulverização Polydeck apresentam uma característica de autolimpeza que eliminou horas de trabalho significativas e sua facilidade de substituição e manutenção garantiu que a pedreira Woodstock não sofreria tempo de parada significativo caso uma peça ou bico precisasse de ajuste, substituição ou limpeza.
A LafargeHolcim aprendeu em primeira mão como adaptar sua operação de lavagem com os bicos de pulverização Polydeck em sua operação Woodstock aumentou sua eficiência, rendimento e sustentabilidade. O subproduto anterior com aplicações muito limitadas é transformado em um produto altamente comercializável dentro de especificações apertadas. A manutenção é reduzida e simplificada. O "convés do dinheiro", como muitos o chamam, é livre para produzir material que resulte em lucro para a operação. Quando os resultados e a sustentabilidade são importantes, os bicos pulverizadores Polydeck de autolimpeza, pesados e de alta eficiência são inigualáveis.
Areia e cascalho Vicdom sabe muito bem que produzir e lavar agregados é difícil para o equipamento. A empresa familiar de terceira geração produz pedra, areia e cascalho há mais de 40 anos em Uxbridge, Ontário, Canadá, a 30 minutos de carro ao nordeste de Toronto.
A administração da Vicdom também sabe que o tempo de inatividade desnecessário tem um custo elevado. Até recentemente, a empresa tinha encontrado problemas de desgaste periódico com a tela metálica de 5' x 7' em seus dois decks, 5' x 14' Dillon telas de lavagem. As telas estavam sendo usadas para produzir +5/8" sobre o convés superior, 9/16"-1/4" sobre o convés inferior, e 1/4" de chip através do convés inferior. Embora as telas tivessem uma vida útil decente e atendessem aos requisitos de produção quando em operação, uma vez danificadas, elas tinham que ser completamente substituídas.
"Teríamos um buraco na zona de alimentação e teríamos que mudar toda a tela, mesmo que 75% da tela ainda esteja em boa forma", diz Victor GiordanoO fundador do Vicdom, Vic Giordano, e neto do falecido co-fundador do Vicdom, Vic Giordano. "Uma tela de $500 era agora lixo".
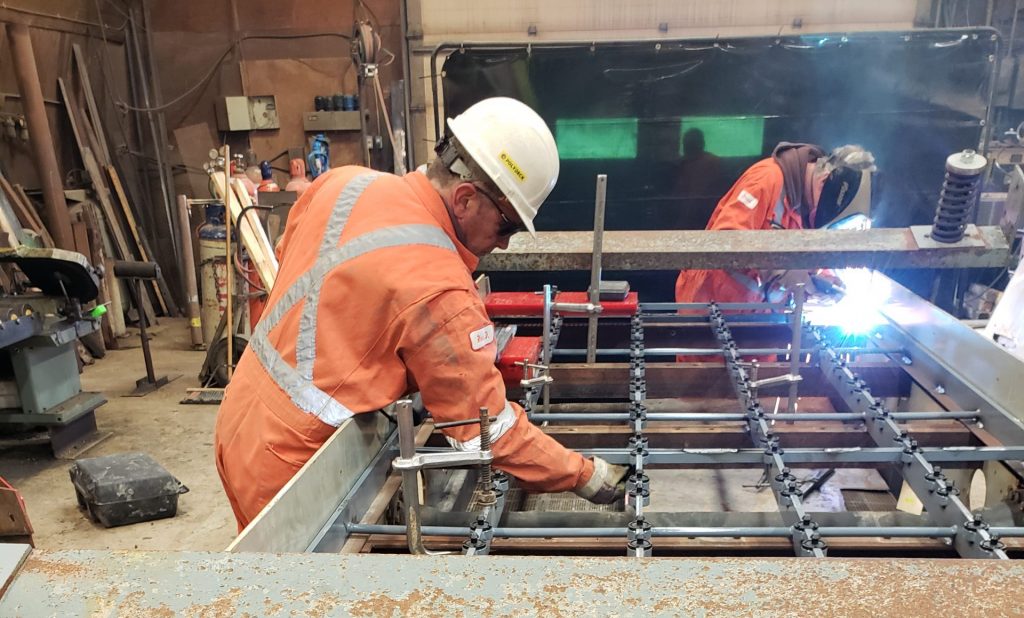
O custo maior decorrente das substituições de tela foi o tempo de inatividade que veio com a troca da tela de 5' x 7', que Giordano diz ter custado sua operação entre uma e três horas de inatividade cada vez que precisavam ser substituídas. Então, quando Alex CaruanaO gerente de território da Polydeck para o Canadá Central e Atlântico, Giordano explicou que a empresa poderia economizar dinheiro e reduzir o tempo de inatividade em sua operação, adaptando suas telas de lavagem com um sistema modular de encaixe, Giordano queria saber mais.
"Alex trouxe um diagrama e fez um bom trabalho ao explicar o que tínhamos antes com a malha de arame e o que poderíamos ter com o Polydeck", diz Giordano. "A maior batida em borracha e poliuretano é que não tem área aberta suficiente como a malha de arame, mas ele mostrou que você não perdeu nenhuma área aberta".
Caruana mostrou a Giordano que ele não perderia nenhuma área aberta usando um método muito simples, mas eficaz.
"O que eu normalmente faço por uma planta quando eles estão considerando um ou mais decks é muito simples. Eu fecho, pulo na tela ou tiro uma foto, e conto apenas as aberturas. Sei quão grandes são as aberturas, porque eu as medi, e isso também me permite levar em conta quaisquer obstruções como barras de pás, barras de fixação lateral, quaisquer desviadores, quaisquer parafusos e outras coisas deste tipo. Isso me permite mostrar ao cliente que com suas telas metálicas atuais, eles têm 'X' de área aberta, qualquer que seja o 'X'", explica Caruana. "E então, sou capaz de mostrar a eles que em sua aplicação, usando nossa mídia, sua área aberta seria agora "X+", e esse é o novo número de área aberta deles".
Em muitos casos, esta comparação é um grande abridor de olhos para os produtores.
"Mesmo com tela de arame, eles podem não ter tido todos os área aberta eles pensaram que sim", explica Caruana. "Imaginem um pedaço de tela de rede na sua frente". Ela está desobstruída, e sua área aberta catalogada, ou valor contábil, pode ser 65%. Ela parece muito atraente. Mas quando você realmente a coloca no lugar, há peças de máquina embaixo dela. Portanto, você não tem realmente 65%, pode ser 48%. Já a mídia sintética não é a mesma. Quando a mídia sintética está dando uma área aberta, isto é, o número bruto e líquido. Quando instalada, ela ainda tem essa área aberta. Se alguém lhe disser que você tem 48%, então esse é o número que está no lugar. Então, fazendo essa comparação para pessoas como Victor no Vicdom, eles têm essa informação disponível para eles e podem fazer uma seleção mais educada".
A Vicdom decidiu mudar um de seus decks de lavagem com um sistema modular de snap usando painéis de poliuretano de 1' x 1' Polydeck com aberturas quadradas de 1/2" no deck superior e aberturas de aproximadamente 1/4" no deck inferior. Giordano ficou impressionado com os resultados.
"Este ano mudamos dois painéis, no total, na conversão", diz ele. "Normalmente teríamos trocado cinco ou seis telas inteiras". Em vez disso, trocamos dois painéis que custaram $90 canadenses cada um por $180 em um ano. As eficiências são boas, a capacidade é boa e o tempo de inatividade é incrível".
A Vicdom agora equipou os quatro decks em suas duas telas de lavagem com o sistema de encaixe modular Polydeck usando painéis de poliuretano de 1' x 1'. A segunda tela de lavagem tem aberturas de 5/8" no convés superior e aproximadamente 1/4" no convés inferior.
A redução do tempo de inatividade com a troca de telas não é a única razão pela qual a Vicdom gosta de trabalhar com a Polydeck. Giordano diz que o nível de profissionalismo de Caruana tem sido um grande ponto de venda, sempre se tornando disponível para auxiliar em qualquer problema que ocorra no local.
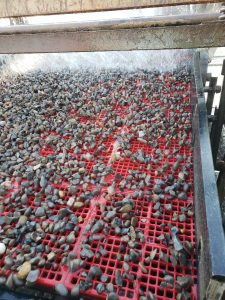
A empresa teve um problema de processamento no ano passado com a primeira conversão, então eles chamaram a Caruana para discutir o assunto.
"Ele perguntou: 'Você tem certeza de que seus excêntricos estão descendo"? recorda Giordano.
Assim, Giordano checou com sua equipe de manutenção e se constatou que eles haviam feito algum trabalho anteriormente naquele dia e acidentalmente religaram o motor para trás na tela, fazendo com que os excêntricos corressem para cima.
"Nós consertamos a fiação, arrancamos a pedra e ela estava funcionando novamente. Com seu conhecimento, conseguimos consertar essa questão imediatamente", diz Giordano, acrescentando que ele tem um grande apreço pelo conhecimento técnico que Caruana traz consigo para o local de trabalho. "Eu não vejo um vendedor. Vejo um cara com muita experiência em vendas, e isso ajuda".
Pensando em uma conversão?
A Polydeck tem uma equipe de profissionais e mais de 40 anos de experiência para ajudá-lo a otimizar seu desempenho de triagem enquanto minimiza o tempo de inatividade.
“Você perde a área aberta quando muda da tela metálica para meios sintéticos.”
Muitos operadores de instalações ainda acreditam que se você mudar de telas metálicas para telas modulares de mídia sintética, você irá perder área aberta em seu convés. No entanto, à medida que mais produtores tentam meios sintéticos, eles desfrutam de maior rendimento e tempo de atividade com o máximo de área aberta e vida útil prolongada, provando que esta idéia é um mito.
Caso em questão
Winter Brothers Material Company é uma operação familiar de areia e cascalho que supre as necessidades agregadas da área de St. Louis por 70 anos. Os dois irmãos fundadores, George "Pete" Winter e Robert A. Winter lideraram viagens fluviais na região durante a década de 1930, e após servir na Segunda Guerra Mundial, eles retornaram à área e fundaram a empresa em 1946.
Localizado no rio Meramec, um afluente do Mississippi, a Winter Brothers minera um depósito aluvial com formato de partícula único, uniformidade e pureza. "Nossa região é abençoada com a disponibilidade do cascalho de grau consistente e da areia livre de lignite depositada pela natureza neste vale do rio", diz Ryan Winter, um membro da equipe de gerenciamento da Winter Brothers.
Mais de 70% dos produtos da empresa são utilizados na indústria de misturas prontas e têm bom desempenho em uma variedade de misturas de cimento Portland. Os produtos também são direcionados para as indústrias de telhados, alvenaria, asfalto, paisagismo, sistemas sépticos e poços de extração.
O desafio
Em sua planta Hagemann, os principais circuitos de peneiramento da instalação produzem seis tamanhos diferentes de agregados grosseiros juntamente com dois tamanhos de produtos de areia. "Desde a abertura da fábrica, sempre usamos telas metálicas em todos os decks de cada circuito de peneiramento", diz Winter, que admite que sua equipe de gestão há muito resistiu ao uso de meios sintéticos devido à preocupação com a perda de área aberta e a diminuição da capacidade de produção.
Algo que eles não haviam levado em conta era a quantidade de área aberta que estavam perdendo devido à fixação do material e à cegueira. Os painéis de tela metálica que usavam eram anunciados como tendo "máxima" área aberta, mas como diz o inverno, "eles cegariam dentro das primeiras semanas, e perderíamos uma porcentagem significativa da produção".
Outros problemas surgiram com o tempo de parada devido à manutenção da tela durante períodos ocupados, quando a fábrica aumenta a produção de carne bovina. Cada um de seus decks utilizava cinco lonas de 4 por 8 pés. de tela metálica, então o Winter lembra que este era um problema crítico para ele.
"Quando uma dessas telas explodiria, teríamos que desligar tudo, tirar os trabalhadores de outros empregos, trazer uma grua, trocar as telas - tudo isso levaria várias horas fora do dia de produção cada vez que acontecesse". Além disso, sempre que uma tela de arame rebentava de repente um buraco, o material em excesso caía e contaminava o estoque de produtos.
Assim, o inverno, juntamente com o Superintendente de Fábrica Steve Klahs - um veterano de 30 anos da indústria - começou a dar uma olhada dura na mídia sintética porque eles queriam entender melhor os benefícios e as armadilhas da troca. Felizmente, eles chamaram a Polydeck para obter conselhos.
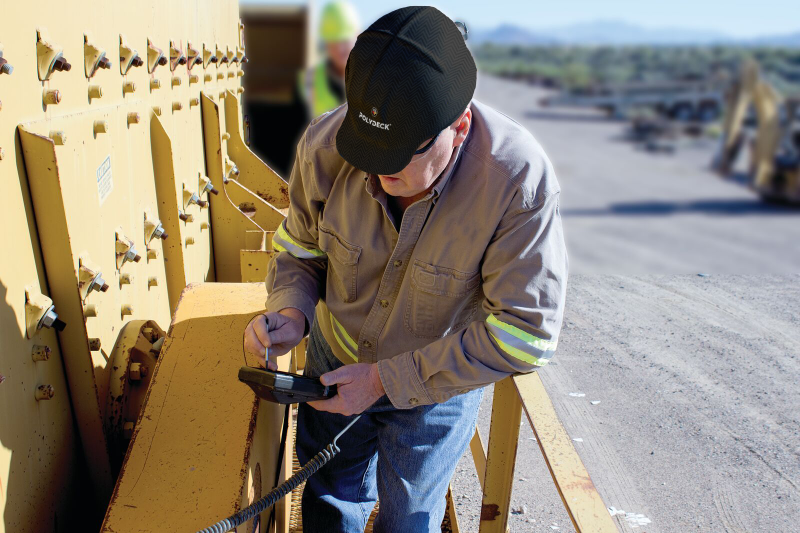
A Avaliação
Depois de conversar com vários fabricantes de mídia sintética, Winter diz que ele escolheu a Polydeck devido à nossa experiência e profissionalismo, e devido ao seu forte relacionamento com o revendedor local Polydeck, CT Fike Co.
"Dan Fike foi muito pró-ativo", explica Winter, "Ele trouxe membros-chave da equipe Polydeck para examinar de perto nossos processos para que pudessem especificar os tipos de painéis adequados para nossas aplicações e gradações".
Joe TeagueA Polydeck, Vice-presidente de Vendas, mas na época atuava como Gerente Regional de Vendas da Polydeck, trabalhou em estreita colaboração com a equipe de gestão da Winter Brothers. Ele demonstrou a eles que sua preocupação com a perda de área aberta está em como a "área aberta" é tipicamente definida e calculada.
"Os percentuais de área aberta publicados resultam em erros de cálculo na especificação da área da peneira e no tamanho da peneira vibratória necessária para uma determinada aplicação", explica Teague. "Muitos catálogos de telas metálicas listam porcentagens de área aberta que figuram em todos as aberturas em uma seção da tela. Na instalação, no entanto, uma parte dessas aberturas é bloqueada por barras de pás, borracha da coroa, calhas de grampo e pinos centrais. Isto significa que a área aberta é significativamente menor, fazendo com que os cálculos fiquem fora até 40 por cento ou mais".
No caso de muitas marcas de mídia sintética, a área aberta é muitas vezes calculada simplesmente ignorando a fronteira. "O painel tradicional tem uma grande borda ou área "morta" ao redor do perímetro que muitas vezes não é levada em conta", diz Teague, "Portanto, mais uma vez, isso significa que a porcentagem de área aberta é exagerada para estes produtos".
Teague mostrou à gerência da Winter Brothers que quando as empresas de engenharia e os usuários finais utilizam esses cálculos imprecisos de área aberta em seu software de análise de fluxo da planta, a planta pode ser projetada com peneiras vibratórias subdimensionadas ou sobredimensionadas.
O conselho de Teague para eles foi uma revelação: A área aberta deve ser calculada tomando o número total de aberturas no painel de tela, e determinando a porcentagem de atual buracos abertos versus o completo superfície do próprio painel. Ele sugeriu que a Winter Brothers adotasse uma abordagem muito básica para comparar a área aberta entre dois fabricantes, contando simplesmente o número de furos em cada painel de tela.
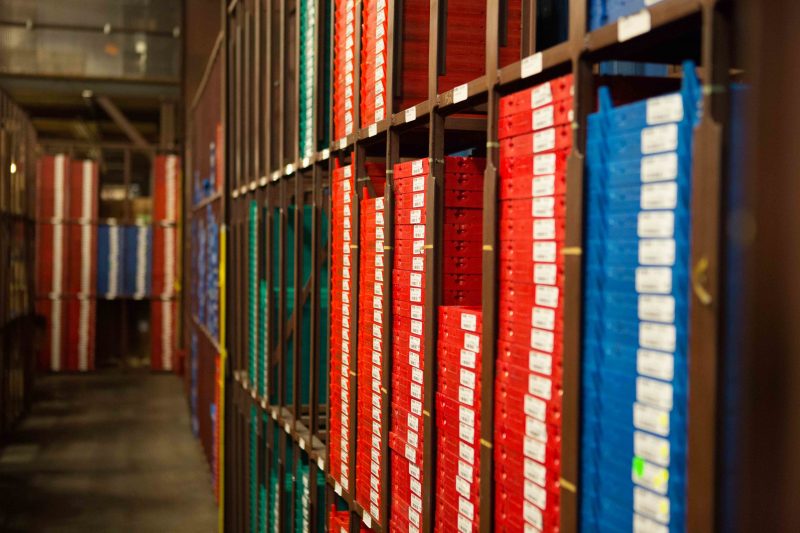
A solução
O objetivo era garantir que o circuito mantivesse o ritmo com o lado esmagador, de modo que a abordagem da Polydeck começou combinando corretamente a mídia com os parâmetros da peneira vibratória, selecionando em nossa biblioteca mais de 1.500 opções de design de painel de tela.
Revisamos todas as misturas de produtos para identificar possíveis inconsistências de gradação e gargalos de plantas, e fazemos quaisquer ajustes iniciais. Após capturar as estatísticas críticas de processamento, executamos cenários "e se" para otimizar as especificações da mídia para as aplicações da Winter Brothers, e determinar como qualquer mudança nas variáveis dentro das operações de triagem afetaria a eficiência geral.
De acordo com o inverno, "Polydeck garantido que suas configurações de painel nos permitiriam atender às especificações exigidas. Se não, então eles fariam qualquer alteração necessária. ao seu custo. Isso nos deu muita confiança quando mudamos tantos decks para mídia sintética.”
No final da avaliação, a Winter Brothers tomou a decisão de instalar o Polydeck's painéis modulares de mídia de poliuretano.
Os resultados Fale por si mesmo
Desde a instalação da mídia sintética, a Winter Brothers tem atendido consistentemente às especificações da indústria.
"Desde que trocamos de lugar, tivemos que substituir apenas alguns painéis nas áreas de impacto. Estamos muito felizes com o aumento da vida útil do poliuretano porque, quando estávamos usando telas metálicas naqueles decks, estávamos trocando uma ou duas telas semanalmente", diz Klahs.
Enquanto Klahs pensava que a mudança das telas metálicas inibiria a produção, ele agora reconhece que o uso de meios sintéticos está economizando tempo e dinheiro na operação deles. "Estamos vendo um aumento inacreditável na produção - quase o dobro - particularmente na areia fina", diz ele. "Além disso, a área aberta nos painéis de poliuretano nos dá um excelente rendimento. Estamos particularmente impressionados com a área aberta que obtemos em nosso processamento de areia de alvenaria".
Para Ryan Winter, a durabilidade e a economia de custos de mão-de-obra resultante do uso de painéis de poliuretano é o principal ponto de venda. Nosso material é muito duro", explica ele, "Enquanto o calcário típico é um 3 a 4 na escala de dureza MOHS, nossa areia e cascalho é um 7 a 8". Portanto, embora o rendimento e a área aberta sejam importantes, a durabilidade é crítica".
"Estamos muito satisfeitos com os anos de vida útil que estamos recebendo destes painéis, e a equipe de manutenção pode pegar qualquer problema de desgaste antes que eles se tornem um problema de parada ou contaminação. Se as amostras de QC estiverem um pouco fora de uso, a equipe de manutenção sabe que deve verificar o desgaste. Se eles precisarem substituir um painel, leva apenas alguns minutos para tirar a tela desgastada e colocar uma nova tela".
"Às vezes as empresas permanecem com os mesmos métodos antigos porque é assim que sempre fizeram as coisas", admite Winter. "É por isso que ficamos com a tela de arame por tanto tempo". Mas acabamos por fazer a mudança para a mídia sintética da Polydeck e estamos felizes por tê-lo feito".
Mito...quebrado!
A nova solução de mídia de tela da Polydeck maximiza a produção e o mix de produtos.
A Aggregate Industries (AIUS) tornou-se uma das maiores empresas de construção e material de construção dos EUA ao enfatizar a sustentabilidade estratégica, a gestão ambiental e as relações de longo prazo com os clientes. A pedreira Morrison da empresa - uma operação de 3 milhões de toneladas de granito por ano localizada no condado de Jefferson, em Colorado- ilustra perfeitamente sua missão.
O Condado de Jefferson é um dos três condados da região de seis condados de Denver dentro da Região Centro-Oeste da AIUS que oferece fontes disponíveis de pedra britada. Como muitos dos recursos agregados potenciais na região de Denver não são acessíveis para extração, a Pedreira Morrison desempenha um papel fundamental para atender à demanda da região por materiais agregados de alta qualidade.
Morrison Plant Manager, Trulane Vanatta opera uma fábrica "esgotada", o que significa que tudo que é processado em um determinado dia é vendido no dia seguinte. Para ele, ele explica sem rodeios,"O rendimento é tudo.”
Como resultado, a instalação mantém um foco constante no aumento da eficiência do processamento e da capacidade de produção. Para eliminar os gargalos nos circuitos de peneiramento, a equipe de gestão da Morrison contratou os especialistas em engenharia da Polydeck.
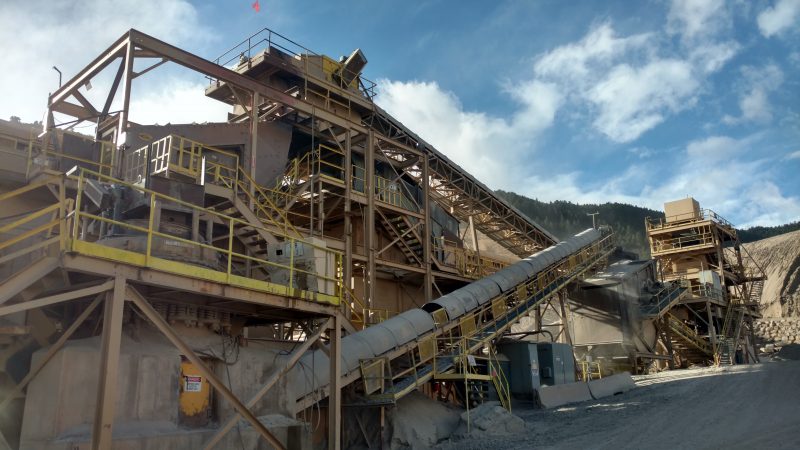
Redução de Cargas Recirculantes e Multas
A equipe da Vanatta identificou um problema no circuito terciário da fábrica de nove telas. Suas amostras de correia indicaram uma profundidade de leito elevada nos decks médios das três telas do circuito. Cada uma das telas de 8 pés por 20 pés. de três decks são fundamentais para a produção do material #57/#67 (1 pol.) da Morrison.
“É o nosso fazedor de dinheiro; e temos que maximizar seu volume de produção", diz Vanatta.
Sua equipe encontrou um "preocupante" transporte do 51%, um gargalo que estava causando a recirculação de cargas e produzindo multas excessivas - um problema de produção comum. “A primeira coisa em que pensamos foi substituir os decks médios em duas das telas terciárias por telas metálicas para conseguir uma área mais aberta", lembra Vanatta.
Acontece, entretanto, que o Gerente Regional da Polydeck's, Sam DurnavichA Polydeck foi gerente assistente da fábrica na Pedreira Morrison há mais de uma década, antes de se juntar à organização Polydeck. Com seu conhecimento da operação, Sam consultou a gerência da Morrison e trabalhou de perto com a equipe de engenharia da Polydeck para criar uma solução de mídia que abordasse mais efetivamente seu desafio de transporte.
Após uma análise completa do funcionamento da Morrison, a equipe de produção da Polydeck projetou e instalou um produto novinho em folha: DMAX™ painéis de tela, um sistema de mídia de tela sintética de área ultra-alta aberta que aumenta significativamente a produção e permite que a pedreira aumente a produção de seus produtos de maior valor.
Os novos painéis de tela DMAX da Polydeck são destinados para uso onde a área aberta e a produtividade são as considerações mais importantes. É uma solução modular de painel de tela sintética que combina ou até excede a área aberta da tela metálica, ao mesmo tempo em que proporciona maior vida útil e maior facilidade de instalação. O sistema de painel de tela DMAX também pode ser formulado com borracha ou poliuretano, dependendo da aplicação.
Exceder as metas de produção
Desde a instalação do primeiro DMAX painéis de tela em dois dos decks médios em outubro de 2015, a operação cumpriu e freqüentemente excede suas metas de produção. Eles também alcançaram uma eficiência de peneiramento muito maior, de acordo com a Vanatta, em uma área aberta de 54% em seus decks médios, em comparação com a área aberta de 42% entregue por seu deck de peneiras anterior. Isso é um aumento dramático de 28,5% em área aberta. Posteriormente, a Morrison instalou painéis DMAX em um terceiro deck médio, em meados de 2016.
“Para nósdiz Vanatta", ".O aumento da área aberta resultou em um aumento de 11% na produção de rochas rentáveis de 1 pol. e reduziu as multas em quase 1%. A única desvantagem da área aberta é que os painéis se desgastam um pouco mais rápido - mas isso é essencialmente irrelevante, pois o lucro do aumento da tonelagem paga pelo investimento em mídia de tela mais de dez vezes.”
A pedreira Morrison também emprega painéis de tela modular Polydeck's Rubberdex® nos decks superior e inferior de suas telas terciárias de 8 pés. por 20 pés.
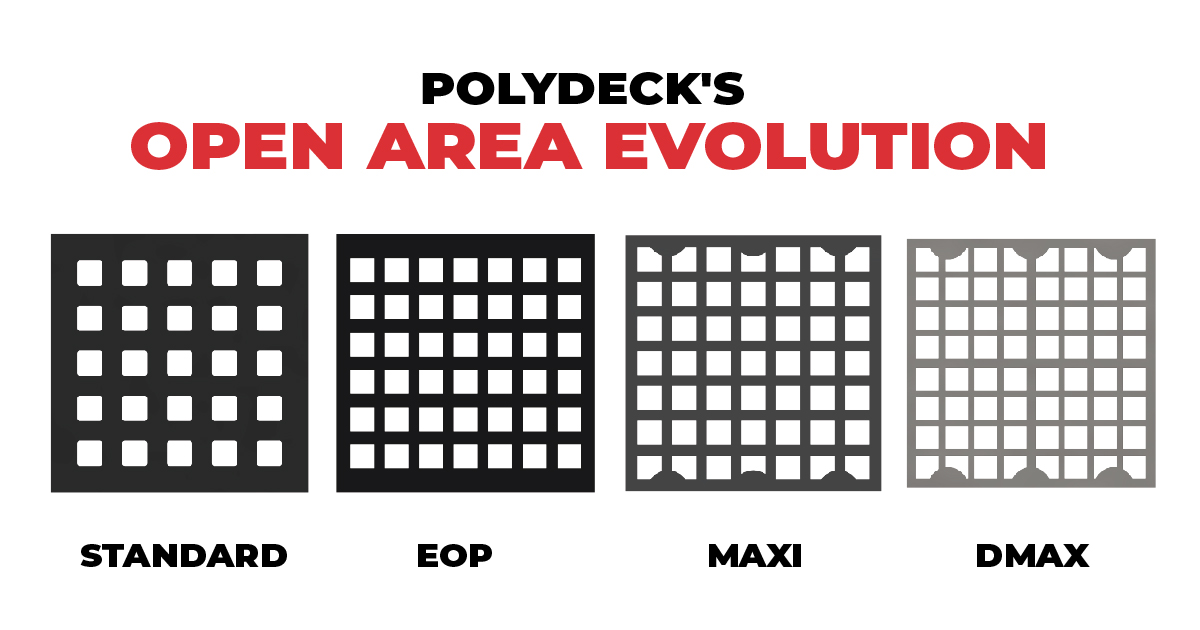
Especialização em engenharia
Explica o Sam Durnavich da Polydeck, "Fizemos os painéis DMax com pontes que são metade da largura daqueles em nosso painel maxi padrão, mas muito mais profundos. Isso é importante, porque a redução da largura da ponte entre as aberturas permite mais aberturas na superfície da tela do painel, o que se traduz em uma maior passagem do produto..”
“Contribuindo para uma área aberta adicional está o fato de que os painéis DMax são projetados para se encaixarem nos sistemas de stringer Polydeck PipeTop II existentescontinua Durnavich. “Este sistema de estrutura apresenta trilhos de fixação exclusivos de meia polegada de largura em vez dos estilos de montagem em sistemas de estrutura convencionais com até 3 pol. de espaço morto onde as multas se acumulam. Além disso, nossas capacidades internas de ferramentas nos permitem oferecer muito mais opções nestes sistemas de armação - desde várias opções de fixação, opções de material e estilos e tipos de stringer.”
“O aumento da área aberta faz vêm com uma redução na vida útil do painel de telaDurnavich admite: "...Mas quando comparados com os painéis de tela para serviço padrão, os painéis DMax estão funcionando com apenas 20-25% menos vida útil, o que ainda excede a das telas metálicas.”
“Nosso uso de moldagem por injeção é um grande fator na capacidade de criar painéis sintéticos de área aberta extrema", acrescenta Durnavich. “A moldagem por injeção garante que cada painel de tela tenha tamanhos e formas precisas de abertura, e que seja completamente curado em todo o.”
“Nossos resultados reais de campo em várias aplicações têm demonstrado aumentos de produção de até 50%, e aumentos de eficiência de peneiramento de mais de 25%Durnavich com um sorriso", diz Durnavich.
A Polydeck continua a expandir a gama de aberturas disponíveis na série DMax, com aberturas quadradas de 12,5mm até 32mm, bem como aberturas ranhuradas de 3x20mm até 25x74mm.
É dito com freqüência: Se há um gargalo em uma fábrica, provavelmente está no circuito de peneiramento. O rendimento é tudo na pedreira Morrison, portanto, o aumento contínuo da eficiência da peneirada é essencial para sua rentabilidade e qualidade contínua do produto. Trabalhando em conjunto, a Pedreira Morrison e a Polydeck resolveram um problema imediato e criaram uma solução a longo prazo.
KWIKDECK é uma maneira simples e econômica de tentar meios modulares.
Mídia de tela é um componente crítico para as indústrias agregada, de energia e industrial e de mineração. Durante décadas, a tela metálica tem sido o meio de comunicação das indústrias, mas a sua instalação é incômoda e não tão versátil quanto a mídia modular. Se você usa tela metálica, provavelmente está acostumado a mudá-las a cada poucas semanas, uma tarefa demorada e às vezes perigosa.
E se você só tivesse que substituir sua mídia de tela duas vezes por ano?
Polydeck's KWIKDECK oferece uma solução melhor: Uma conversão de quadros que permite experimentar telas sintéticas praticamente sem riscos, com custos mínimos de configuração e fácil instalação.
O KWIKDECK ajuda você a cortar custos operacionais, reduz o tempo de inatividade enquanto melhora a segurança e mantém seu equipamento funcionando com o máximo desempenho.
O que faz do KWIKDECK uma solução tão ideal?
- É simples de instalar - O KWIKDECK leva cerca de 45 minutos para trocar uma seção de 4 pés por 6 pés. Ele reutiliza os trilhos de fixação laterais existentes, e não requer a alteração da estrutura da mesa existente.
- É adaptável - O KWIKDECK trabalha com decks coroados, e pode ser modificado para se adaptar às dimensões e configurações da maioria das máquinas vibratórias.
- É rentável - O KWIKDECK permite o uso de telas sintéticas, que duram pelo menos dez vezes mais que as telas metálicas[1] e requerem menos manutenção e menos trocas do que as telas metálicas.
O KWIKDECK também é perfeito para operações de peneiramento portáteis que precisam alternar entre tela metálica e meios sintéticos. Os operadores podem facilmente alternar entre diferentes tipos de mídia para maximizar os requisitos de produção.
O KWIKDECK oferece uma oportunidade para os usuários tradicionais de telas metálicas experimentarem os meios sintéticos com custo ou risco mínimo. Instale-o na extremidade de alimentação de sua peneira vibratória, e veja por si mesmo que diferença isso faz.
Saiba mais sobre KWIKDECKmais um produto inovador de seus parceiros na Polydeck- e apenas mais um exemplo de como somos juntos fortes.
[1] http://www.pitandquarry.com/pq-university-lesson-8-screening/