Mining and aggregate operations that utilize Polydeck synthetic media experience many benefits, including a decrease in downtime with a modular system, increased media wear life, and the ability to add surface features. Polydeck surface features can either be integrated into the panel design or added onto the modular system as an auxiliary feature. This article will review molded surface features, which include dams, restricted flow bars, skid bars, and deflectors. Each can play a key role to increase efficiency when used correctly.
Dams can be molded on both POLYDEX® and RUBBERDEX® media and serve three primary roles: they slow the material flow, help build bed depth, and aid in material stratification. Injection-molded dams come in 1”, 2”, and 3” options. Dams are commonplace in many operations and may be useful to slow material on slurry-fed or incline decks, retain material under spray bars to maximize fines removal and passing of near-size material, or build bed depth in lightly loaded applications. They also stratify the material by agitating and redistributing the fines to the bottom of the material bed.
Pro Tip: For Flexi RUBBERDEX® panels with dams, Polydeck recommends installing dams oriented to the feed end for improved wear life.
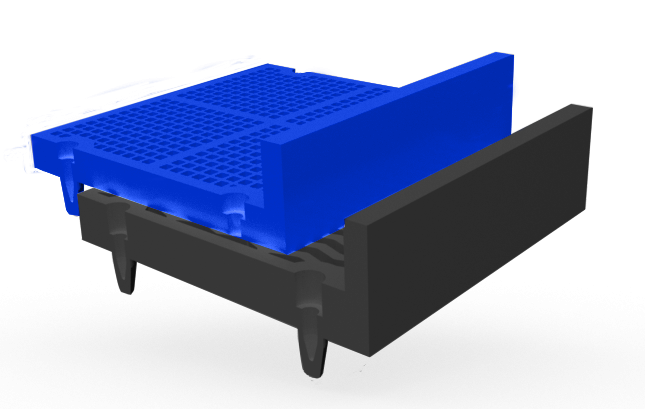
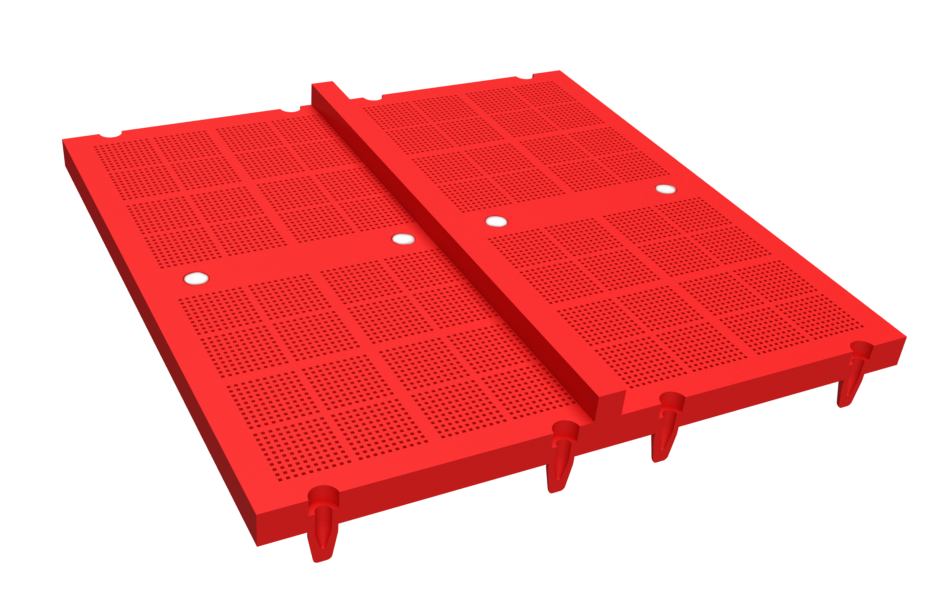
Restricted Flow Bars, or Restricted Flow Dams, consist of a multitude of low-profile dams along the surface of the panel; these are oriented across the flow of material and are available with many POLYDEX® panel designs. Similar to traditional dams, these may aid in slowing material across a deck, but they are especially effective in stratifying material.
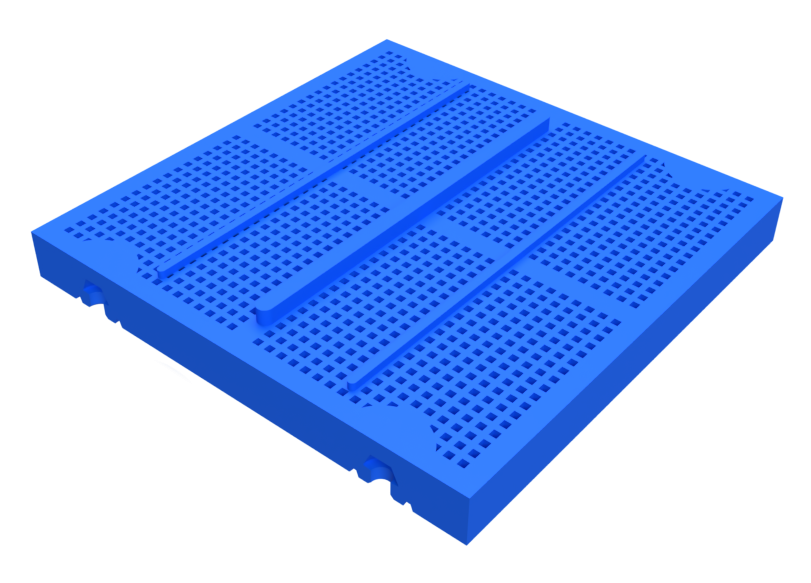
Skid Bars have similar structural form to the Restricted Flow Bars, but the orientation is with the flow of material. The main purpose for skid bar use is to increase wear life in heavily loaded or highly abrasive applications. These may be added to increase panel rigidity, as well, and are available on both POLYDEX® and RUBBERDEX® media.
Pro Tip: Use Skid Bars as stratification aids. Apertures prone to blockage by oversized material can be cleared by elevating the rocks via skid bars; this allows smaller material to pass through the panel.
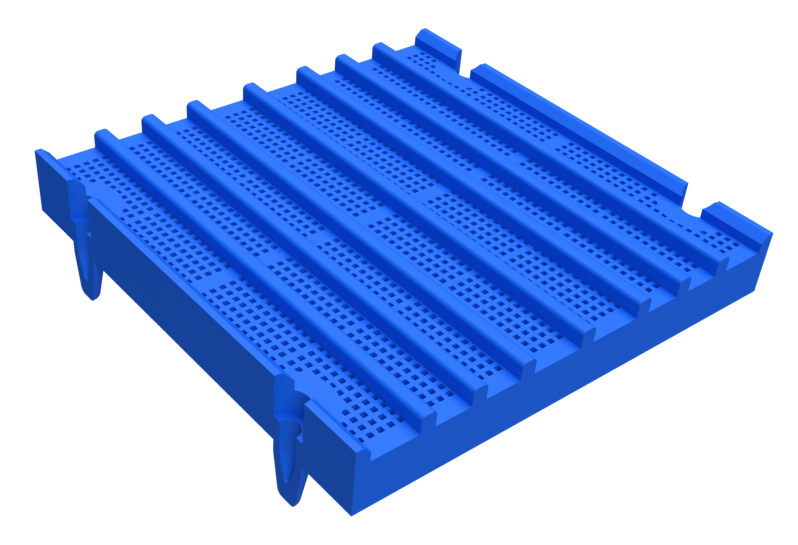
Deflectors are small protrusions intended to prevent material from channeling down the panel margins. As the name implies, these deflect the material from the margins to reroute the material over the apertured panel surface. These are highly effective on Polydeck Standard, Extended Open Area (EOP), and Polyrail panels, which carry wider lateral margins to protect channel and tube stringers.
Pro Tip: For many Standard and EOP applications, an alternative to deflector use is converting the deck support to Polydeck PIPETOP STRINGERS; this change significantly reduces the margin and increases open area with Polydeck MAXI and DMAX media.
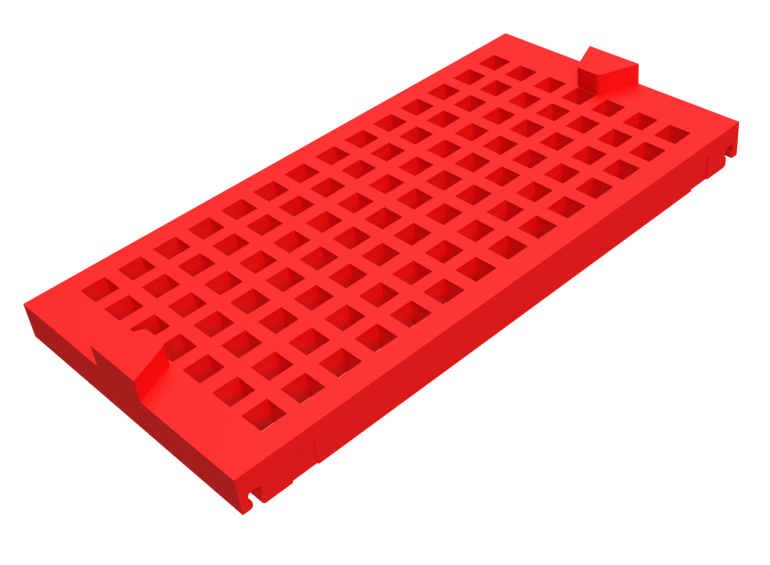
In conclusion, molded surface features are simple additions that can make notable impacts on the efficiency of many screening operations. The molded surface features smoothly integrate into most Polydeck modular media layouts and are an easy means to mitigate common screening challenges with the change of a panel.
Contact Polydeck for more information or a personalized recommendation on molded surface features and other process improvements.
Written by Jamie Mills, Product Development Application Engineer for Polydeck.
Learn about Polydeck PROTEX from our expert and Northwest Regional Manager for Aggregates, Kendall Herring. Kendall assists the aggregate customers in his region to ensure their operations are optimized for efficiency and throughput in order to meet their production goals. In this blog, Kendall details the benefits of utilizing Polydeck’s custom and in-stock wear liners to preserve durability and reduce maintenance time in aggregate operations.
The best-known benefits of Polydeck modular screen media products are wear life, ease of maintenance, and reduced downtime. Why limit these benefits to screen media? Liners are one of the most used products that Polydeck manufactures. Whether you are looking to line a chute, feedbox, discharge lip, conveyor belt liners, hopper or any other wear point, PROTEX is the solution for you.
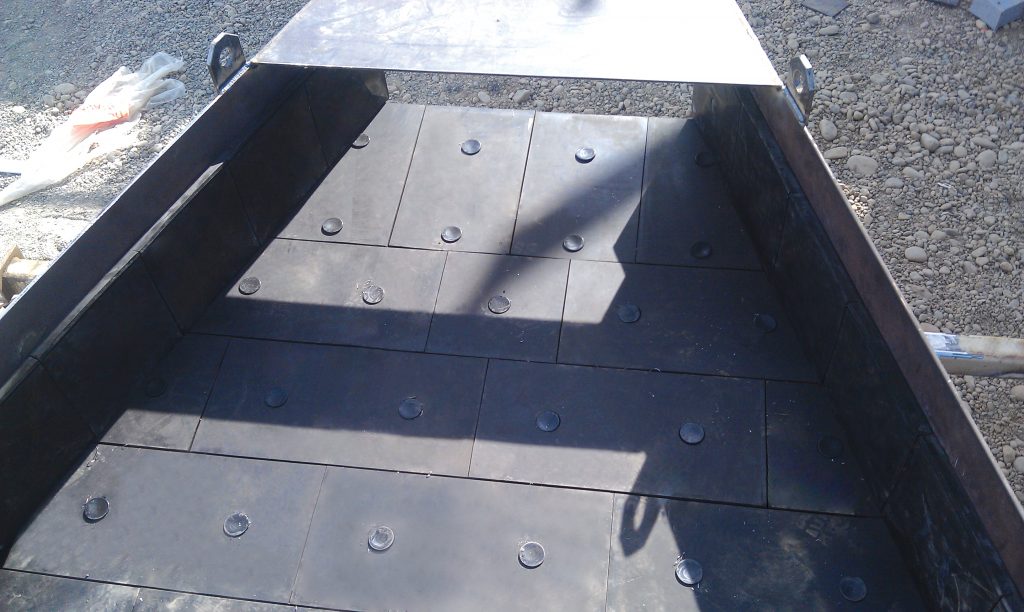
Are you still using wear metal such as AR plate or other hardened steel? Do your employees spend hours cutting and welding inside narrow chutes? If so, it’s time for you to move into the next generation of wear protection: synthetic liners. Pound for pound, steel products simply cannot compete with the longevity of synthetic materials such as polyurethane, rubber, UHMW, and ceramics. Welding in enclosed areas like chutes is time consuming, awkward, and is a health concern for employees exposed to the fumes. Alternative methods of fastening such as bolt-in, whether with stud bolts or through bolts in countersunk holes, make synthetic liners quick and easy to replace and ensure the fastening will last the life of the panel by protecting the bolt from wear. For even faster attachment, Polydeck’s newly released PROTEX ML (magnetic liners) offer a great option. Simply pry out the old magnetic liner, drop in the new one and fire the plant back up.
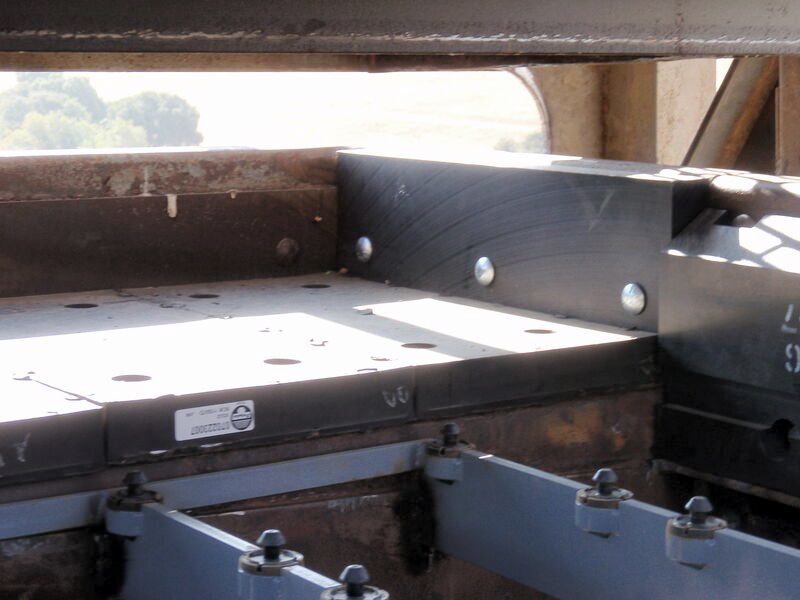
For convenient sizes, quick availability, and robust protection Polydeck stocks 1” and 2” thick PROTEX RL (rubber liners) in 12” x 12” and 12” x 24” sizes. This size range allows you to easily create a tiled pattern on your wear points that can be quickly and easily replaced by a single employee. If you forget to order replacements, these liners can be shipped on demand to your site. For those odd bends and angles in your chutes, the stock liners can be cut to fit in the field. Alternatively, Polydeck can create any custom shape and place bolt holes in any position. These custom liners will arrive ready for installation and immediate use in your plant.
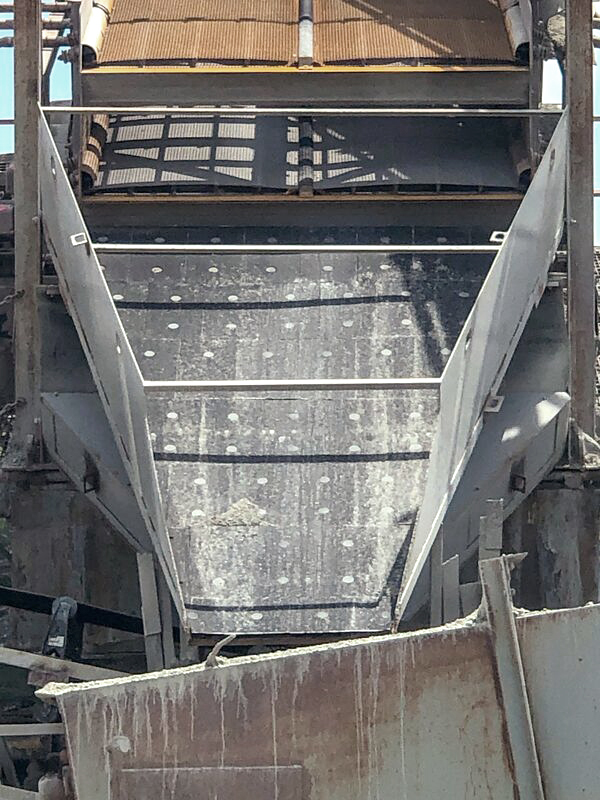
Do you need sizes sufficient for your heavy-duty application? Let’s go BIG! Polydeck is capable of making any size and shape rubber panel up to 4” thick and 4’x8’ overall dimensions. One of the most common applications for these custom liners is to fit the feedbox or discharge lip of any screen arrangement to protect these common impact areas. Still need more protection? For the most extreme applications, Polydeck recommends installing the new PROTEX CL (ceramic liners). Depending on your need for impact or abrasion resistance, Polydeck provides ceramics to maximize your wear life and prevent costly downtime.
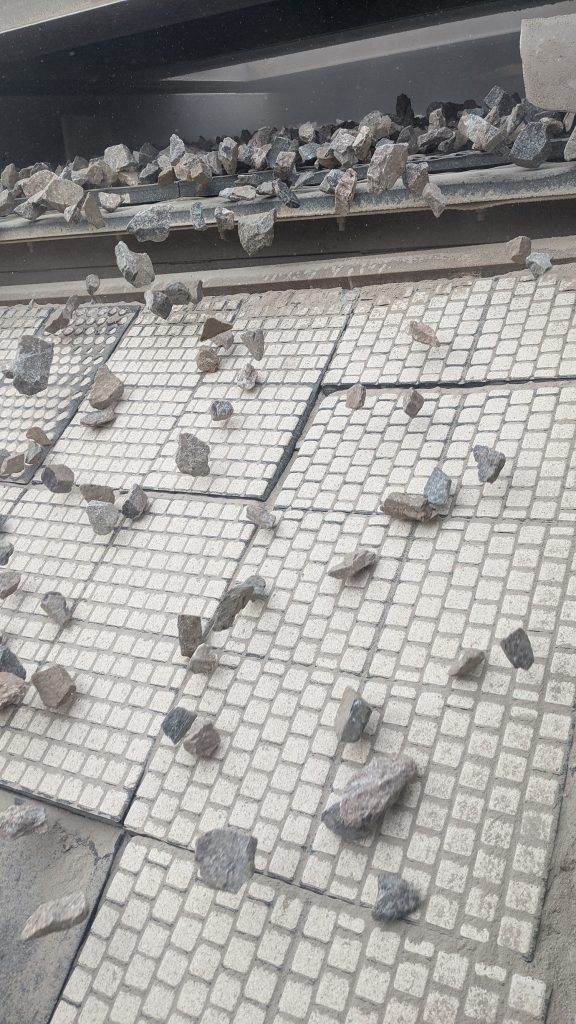
When you chose to upgrade your wear lining components to Polydeck’s PROTEX options, you will receive expert advice on the best liners for your application, and products designed to last. With over 40 years of experience refining our compounds to provide the industry’s premiere synthetic liners, you can rest assured Polydeck products will last. PROTEX will reduce your operation’s maintenance requirements, improve your operating efficiency, and save you money. Go beyond the screen and experience the durability of PROTEX.
Part 2 covers extending the life of your equipment and maintaining operations by being proactive with maintenance and quality control.
In Part 1 of this two-part series, we reviewed some of the many decisions that must be made before selecting the right screening solution for your operation. Asking the right questions upfront can really pay off over the life of your equipment, once you’ve made the investment.
Part 2 below looks at how to extend the life of your equipment and maintain smooth operations over the long-haul by establishing a system of proactive maintenance and quality control. With such a system in place, you achieve greater visibility over your operational performance and can identify emerging issues before they develop into major problems.
Proactive Maintenance
A schedule of regular maintenance is the best way to ensure that your screening system operates reliably, with a longer wear life, consistent specification accuracy, minimal downtime, and maximum cost efficiency.
Whether you use wire cloth or a synthetic option, periodic visual inspections of your system are necessary to detect any extreme or unusual wear.
- Check synthetic screen decks for wear patterns possibly caused by a change in feed rate, uneven material distribution, or high-pressure water spray. Replace worn screens immediately to prevent out-of-spec material or damage to the fastening system or steel support structure.
- Make sure side-tensioned media screens are tensioned correctly upon installation, and be sure to support side-tensioned synthetic screen decks with high-quality bucker bar rubber. Check them on a regular basis, looking for loose clamp bars or blocked apertures that are plugged with material or blinded over, and re-tension the screens where needed.
- Examine side wear liners as they typically last longer than the actual screen surface, looking for wear and for loose bolts or clamping hardware. If all liners are not securely tightened, the screen panels can move, and potentially damage the side wear liners, the screen panels, or the modular support structure itself. Loose side wear liners can also allow screen panels to disengage, causing material to go out of spec.
When replacing modular synthetic media, ensure a secure attachment to the frame by cleaning sand or fines from the frame surfaces and the fastening cavities.
Regularly evaluate your screen equipment for unusual variations in operating parameters, such as acceleration, displacement, deflections, and critical frequency, all of which can hinder screen performance and even seriously damage the support structure.
It’s also important to work closely with your screen media manufacturer to perform a screen analysis on the machine itself, in order to isolate the possible cause of poor screening performance. Don't forget that Polydeck offers screen performance evaluations and we're ready to help.
Quality Control
Frequent quality control sampling to detect spec changes—either sudden or gradual—is an effective method to monitor the wear life and condition of your screen media.
With modular synthetic panels, the maintenance crew should always be looking for any wear before it becomes a contamination problem. If the quality control team detects gradation changes, however, they can also alert the crew to start gauging the screens and check for any unseen wear issues.
Replace affected modular synthetic media when a product gradation begins trending to the high or low end of the spec range. It takes just a few minutes to change out any worn screen panels and resume operation.

No matter what screen media you deploy, it will eventually succumb to the wear-and-tear of everyday use, not to mention the common operational hazards of the industry.
Selecting the right screen media for the job, and then performing proactive maintenance and quality control tasks, are the best strategies for maintaining optimal performance. By repairing or replacing worn components before they fail, operations can ensure the day-to-day reliability of valuable processing equipment while meeting or exceeding production goals at the same time.
To help you get the most out of your synthetic media, we've created a downloadable checklist for you. Click the link below to get your copy.