Pinto Valley Mine, part of the Capstone Mining Corporation, is currently the only open pit copper mine operating in the historic Globe-Miami mining district of Arizona. As an older plant designed to run a maximum of 48,000-tons per day, the facility has recently focused its efforts on optimization initiatives to meet market demand.
30-year mining industry veteran, Bob Dickey, who has overseen the Pinto Valley Mine for the past three years, is the driving force behind optimizing screening circuits and using high-quality screen media to increase efficiency. When Dickey took over the plant, his main goal was to push as much production through the plant as possible. To do this, he knew he would need to bring in suppliers and partners to boost efficiency at the mine to fuel high-impact, quick-payback results.
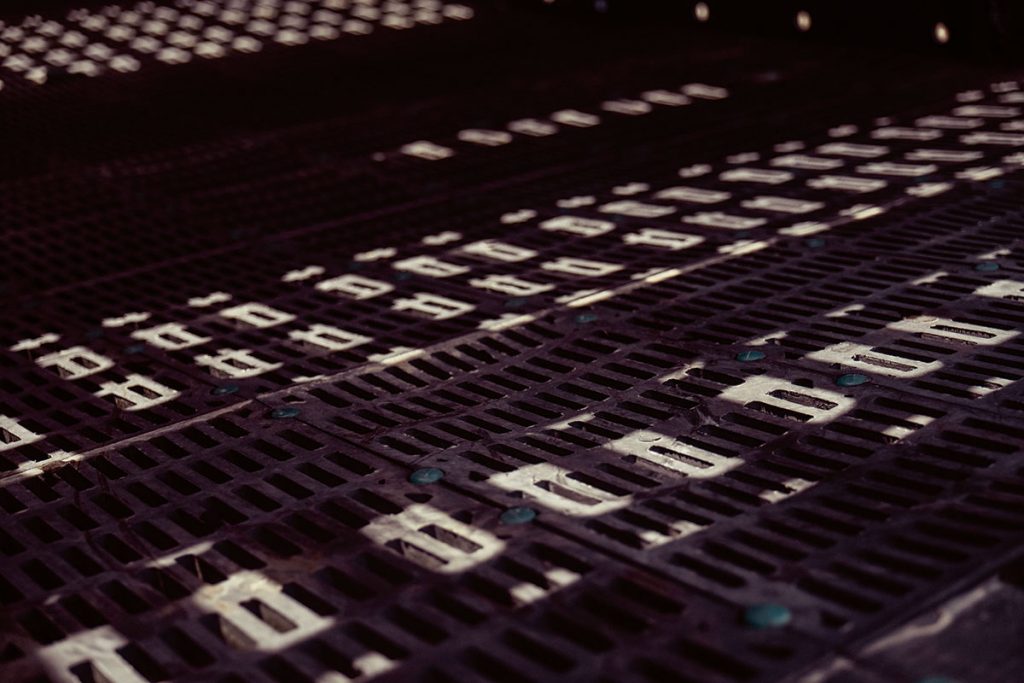
For Pinto Valley, the biggest need was to maximize open area on the screen deck to get the desired throughput. “If a screen deck panel lasts six months, but we’re wearing it to a point that oversize is going to the ball mills, then there’s no value in that. Instead, we focus on maximizing the efficiency of those screen deck panels until we reach the targeted wear point that triggers the deck changeout,” stated Dickey.
As he began prioritizing the elimination of bottlenecks within the screening circuits as a quick way to optimize performance, Dickey turned to Polydeck for assistance.
Polydeck’s Mining expert, Tom Wayment, visited Pinto Valley to learn more about the challenges the site was facing with its existing process. Through extensive on-site testing, hands-on follow up, and service, the Polydeck team worked closely with Pinto Valley to “dial in” the screen circuits to meet specific requirements.
“Since Pinto Valley runs six identical screens side by side, Polydeck media could be tested right next to a competitive media brand,” said Wayment. The video testing showed a clear indication that the Polydeck media resulted in a clean bottom-deck oversize being fed to the tertiary crushers.
The Polydeck team worked to install a custom layout of Polydeck RUBBERDEX® modular screen media on the secondary and tertiary double-deck screening circuits to increase open area and wear life for greater efficiency. RUBBERDEX XLR® media is installed on the first three rows of the feed end on the top deck. The specially formulated XLR media compound is engineered for up to 15-percent increased wear life in abrasive applications. The remainder of the top deck features RUBBERDEX® panel types that target high-wear or heavy-feed applications. The bottom deck also utilizes abrasion resistant XLR media panels on the feed end, with the remainder of the deck featuring RUBBERDEX® panel types designed to minimize blinding and allow higher material throughput.
To maximize open area, decks are mounted on Polydeck PIPETOP™ media systems, with narrow ½-inch-wide rails that allow for more openings on the panels, and consequently, more material throughput.
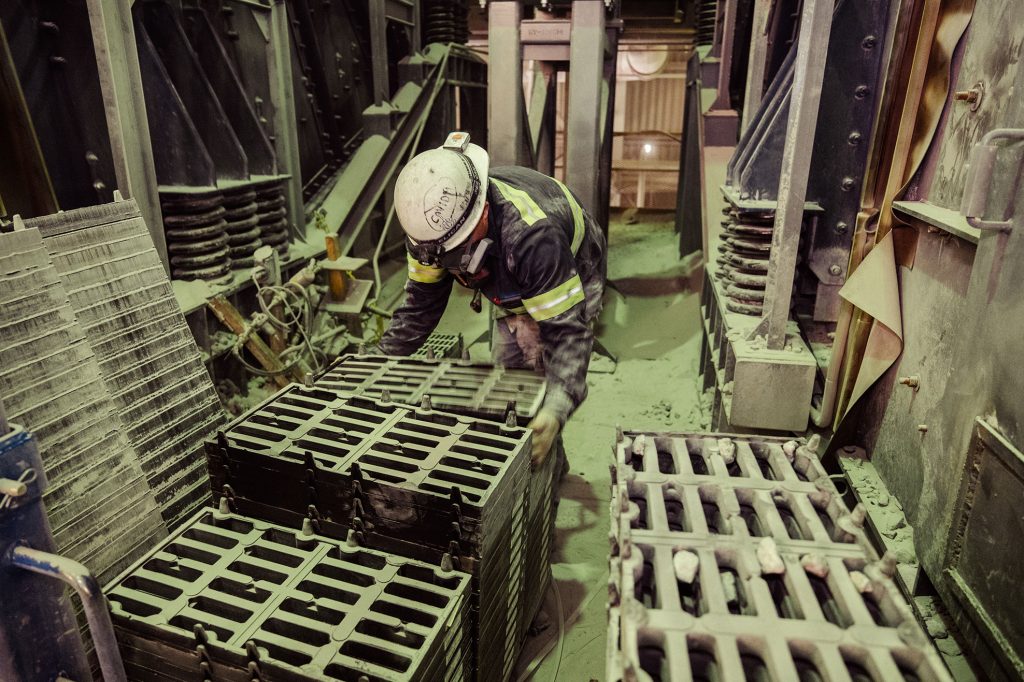
With the help of Polydeck experts and the installation of Polydeck screen media, Pinto Valley increased efficiency to 60,000-tons per day by increasing open area, providing greater screening availability, and maintaining a clean feed being discharged to the crushers. Bob Dickey defined Polydeck as “a true partner, [who helps] to find the ultimate solution – even if it’s not one provided by them”. By consistent testing, evaluation, and tweaking, together with Polydeck, Pinto Valley found a way to combat dated technologies and maximize its operations.
Polydeck’s President, Ron Kuehl and Director of Supply Chain, Bryan Travis, reflect on supply chain in 2021 and what’s in store for 2022.
Q: How would you characterize the supply chain as you look into 2022?
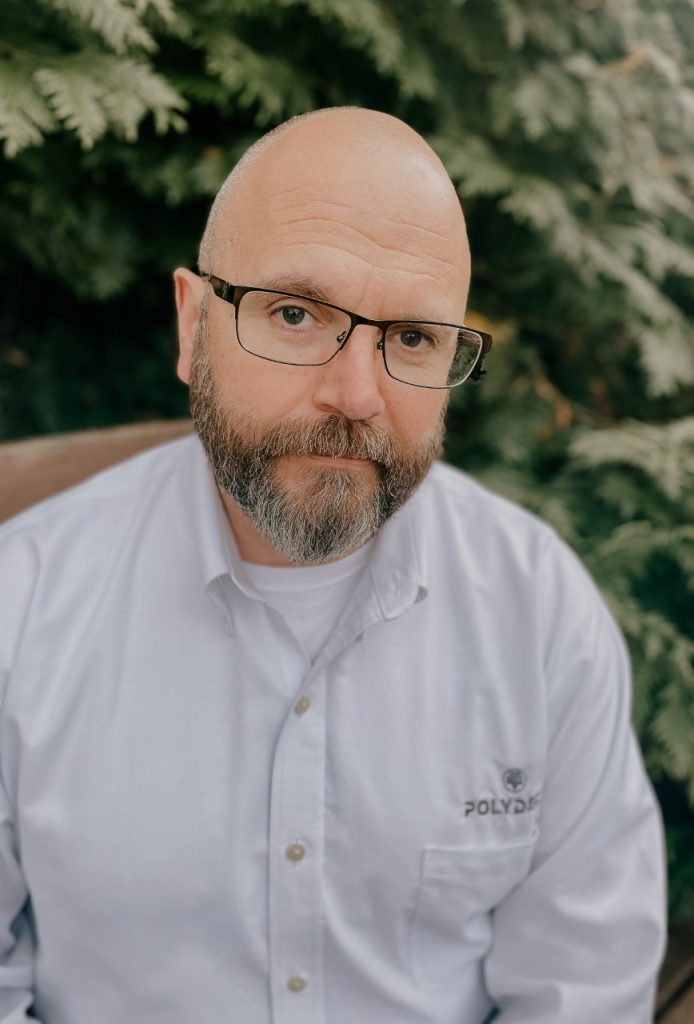
Travis: The global supply chain remains strained on multiple fronts and will face ongoing pressure throughout much of 2022. As material availability improves and the logjam in transportation becomes less congested, there will be sections of the supply chain that ease. These pockets of easing, however, will likely be offset by other complications as the flow of raw materials work to normalize. Thankfully, Polydeck's strong relationships with suppliers have allowed us to foresee the current supply chain shortcomings and adjust our inventory positions in advance to prevent any such disruptions.
Q: What “shortages” if any are you (or the greater screening industry) seeing at the moment when it comes to screening equipment?
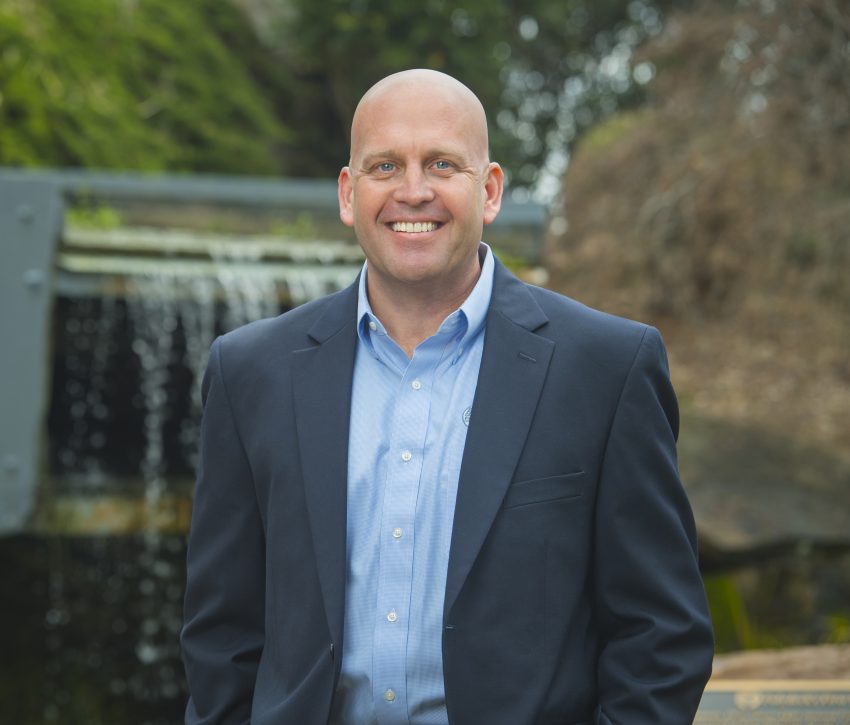
Kuehl: Steel, Polyurethane, and Rubber compounds are key materials that remain strained in the current environment. The resin and chemical industries have endured numerous impacts due to government restrictions, COVID-19 induced labor shortages, power interruptions at Gulf producer sites, and feedstock material shortages. Steel productivity is improving, with additional capacity coming online around the globe. A notable aspect of this current cycle has been the material disruptions and pricing inflation which has impacted multiple commodities and rippled across global markets. As a result, we have had to pass along some inflationary increases to our customers, but through our strong partnerships with suppliers and intentional efforts to maintain inventory levels we have been able to shield our customers from product disruptions.
Q: How are you advising customers to order for 2022?
Kuehl: With material and transportation impacts remaining front and center, customer collaboration and supply chain partnerships are a top priority. Today, in our customer conversations, we regularly emphasize the importance of communicating forecasts, growth plans, and development needs for 2022. Our operations team is preparing for growth and ensuring our ability to offer great lead times within the existing constraints. We look forward to continued customer conversations and value collaborative planning and communication so that we can do our best to hold lead times and offer our customers improved service during these difficult times. Our ability to meet our customers’ needs is only possible through the weekly input we receive from our suppliers to adjust raw materials levels, by leveraging our global manufacturing sites and suppliers and increasing our finished goods stock levels.
Q: Anything else you’d like to add?
Kuehl: This disruptive cycle has driven the need for an increased focus on supply chain efficiency and resiliency. The risk mitigation process and its effective deployment has become a critical part of supply chain management at Polydeck. As a customer to our raw material partners and a supplier to the mining industry, Polydeck has embraced a holistic approach to risk mitigation as a vital part of our business process allowing us to remain as dependable as ever.
*Article will also be available in Pit& Quarry January issue
In 2021, Polydeck set out to wow customers, improve profitable growth, create a winning work culture, and improve on our past successes. Together, we worked hard to achieve our goals and have succeeded.
Despite labor challenges, supply chain constraints, rising raw material costs, and the continued threat of COVID-19, we were still able to maintain the best lead times in the industry combined with a record year in product quality. Our record bookings and shipments coupled with our “Best Place to Work” certification proved to us just how strong our culture and teams are. The launch of our new product category- PROTEX- and Customer Satisfaction score of 93.34% (World Class status) is a primary indicator of our position as leaders in the industry.
As we continue to focus on continuous improvement especially in the areas of environmental, social responsibility, research and development, and the launch of new products, we still maintain that our employees—the Polydeck family—is our greatest strength.
One of the most rewarding projects that we worked on this year was leadership. Identified leaders at Polydeck underwent what we have called “The Leadership Commitment Training,” which is a 7-week cohort training series taught by Polydeck’s Senior Leadership Team.
I was honored to kick off the series and teach on one of Polydeck’s core business values--Leading people in a way that honors God. Some key highlights from my research included:
Leadership is:
- not power; it is a responsibility
- benefits all when done right
- daily effort; it is intentional
A word on each-
Leadership is not power, it is a responsibility
When we look at the key leaders in our lives, we realize that it isn’t their ability to make decisions that we value most about them, but the ability to make the BEST decisions. BEST decisions are made when each team member can contribute their thoughts and ideas toward reaching the common goal. A great leader brings out the best in their team, making sure all voices are heard, and decisions are made together for the betterment of all people--leadership is for people, not over people.
Leadership benefits all when done right
Good leadership inspires, challenges, anticipates problems, rewards, and uses mistakes as teaching tools--even people you disagree with, feel valued and led when leadership is done right.
Leadership is a daily effort; it is intentional
It is important to remember that leadership can be learned. In my experience, it is a daily effort, not just a class you attend or a certificate that you attain, or even a document you sign. It is also important to recognize that leadership is a process. Processes take time and growth cannot be done in isolation.
As we look forward to another successful year together, our hope is that we continually wow you, our customers, not only with our level of service but our commitment to leading well. We hope to serve you and continually conduct our business in a way that honors God. Thank you for partnering with us and have a wonderful rest of the year.
Written by Ronald D. Kuehl II, President of Polydeck
Polydeck presented a look into the future of screening at MINExpo. Below are a few highlights pulled from The Future of Screening presentation.
Q. What's next for screen media?
A. The biggest opportunity we see in the industry is through the digital monitoring of screen media health. Screen media has always been a key part of process reliability and efficiency through proactive management practices. As operators seek to deliver more production with fewer resources, our customers are challenged to maintain these proactive screen media practices. The trend towards digital monitoring of production processes across many industries has accelerated as organizations continue seeking increased productivity. The rise of the technologies and infrastructure associated with the Internet of Things (IoT) creates an opportunity to provide operators with timely, relevant information regarding the health condition of their screen media. We are focused on implementing sensors within screen media panels that will monitor a variety of health-related factors.
Q. Why smart panels?
A. Smart screen media panels will provide critical data for assessing screen panel status and performance. These data provide actionable insights for optimizing plant operations. We see these data focused on delivering two different types of critical information. The first type of information is based on tracking long-term usage and performance patterns of the screen media. Data used for this will include the age of the panel, the wear level, and the physical location. The goal is to use this data to build predictions of wear life, and in turn, recognize when maintenance might need to be performed or replacement parts need to be ordered. This information can be used to optimize maintenance planning, avoid stock-outs, and ensure the most efficient use of screen media.
The second type of information we are seeking to deliver relates to the detection of critical events that may require an urgent response. Events of this type might include the dislocation of a screen panel or an impact that breaks or punctures the screen media. Today, if a panel comes loose or fails catastrophically in some way, you often don’t know until it’s too late. By using these embedded sensors and connecting operators with the screen panels through digital technology, we will help users avoid costly downtime and repairs and reduce the chance for misplaced material within a circuit.
Q. So where will you start?
A. We know that smart panels aren’t going to happen overnight. This is a development journey that requires customized digital sensors connected to new networks and advanced software tools. We have a plan that will build out these solutions in phases. Each phase of development is driven by the critical needs of our customers.
Our first step in this process is creating and embed unique identification numbers in our screen panels. This is a building block for us and what we will spend time in 2022 perfecting this implementation. Creating embedded unique identification numbers will allow us to have individual traceability for every single panel. We are working to actively couple this traceability with wear level monitoring. Over time, we will be able to track the product from the day it is manufactured to whichever deck or machine it ends up on, determining how long it was in service and its wear rate. This will give us a more complete understanding of the overall cost of screening in an operation.
Q. Is there anything more you'd like to add?
A. At the end of the day, we want to create something that is going to reduce the complexity of screen media management for our customers and further optimize their screening operations. Based on the testing we have done to date and the input we’ve received, we believe this digital transformation will deliver on this objective. Our team is serious about this endeavor and are actively working to create, test, and implement the foundational technologies that will deliver on the promise of digital monitoring of screen media health.
FOR IMMEDIATE RELEASE
SPARTANBURG, South Carolina (August 1, 2021)
Polydeck Screen Corporation, the global leader in modular synthetic screen media and screening accessories for the Minerals and Mining, Aggregate, Energy, and Industrial Industries, announces a new product category of protective items called PROTEX, debuting at MINExpo 2021 in Las Vegas, Nevada in September.
PROTEX was developed to advance Polydeck’s mission of solving the customers biggest challenges by offering a line of complementary products that improve equipment life and increase production efficiencies.
The PROTEX line includes Liners, Frame Protectors, Side Wear Plates, and other in-demand items such as Ceramic and Magnetic Liners. True to the Polydeck reputation of customizable and easy-to-install products, PROTEX meets the unique needs of operations the company serves and is a natural extension of the brand.
“We are thrilled to expand our offering into protective products for our customers, who trust us with their modular screen media needs and seek out our products and the expertise of our people to help them solve the challenges they face in their operations,” stated Polydeck Vice President of Sales and Marketing, Joe Teague.
Items in the PROTEX line are designed to extend the wear life of processing equipment and increase the safety and reliability of operations.
“We are well known for our ability to assess our customers’ operations and recommend customized solutions to help them achieve their productivity goals. Now, with our line of PROTEX products, we can help them increase the reliability of their operations as well by extending the life of their equipment and reducing unplanned maintenance time,” added Frank Harris, Director of Sales, Mining.
The PROTEX Category includes the following product lines:
PROTEX C-
Fully Enclosed Seamless Coating and Rubber Lining for Frames/Steel structures
PROTEX L-
Chute Liners including Polyurethane, Rubber, Magnetic Polyurethane, and Ceramic
PROTEX SL-
Side Wear Plates including Polyurethane, Rubber and UHMW
PROTEX P-
Protop Stringer Protectors, Angle Protectors, Cross Member Protectors, Polyrail Channel Protectors
ABOUT POLYDECK
Polydeck Screen Corporation is a family-owned company headquartered in Spartanburg, South Carolina. Founded in 1978, the company is the leading provider of modular synthetic screen media products and accessories for the aggregate, energy and industrial, and mining industries. Polydeck employs more than 340 employees worldwide and serves customers in more than 40 countries.
Learn more at https://polydeck.com/.
Couer Wharf gold mine is an open pit, heap leach operation located in the northern Black Hills of western South Dakota, approximately four miles southwest of the city of Lead, South Dakota. The property consists of several deposits of adjoining gold mineralization, which have been mined as a series of open pits and covers almost 8,000 acres.
The mineral processing plant at Couer Wharf was experiencing heavy blinding and plugging issues on their vibratory screens, especially with wet material or frozen conditions, which can occur often during South Dakota winters. Screen blinding was a common occurrence, according to onsite Maintenance Manager Jasmine McCauley. Feed material would cover the screen media and blind over, which made it very difficult to achieve production targets. Couer Wharf leadership began to search for alternatives, knowing there had to be a way to solve the blinding and plugging problems and return the operation to target production levels.
Initially, Couer changed to competitor screen panels to increase the tonnage on their Tabor heavy duty incline screens, but it resulted in a decreased percentage of material passing through the deck. Gold recovery was negatively affected, as well. Wire-cloth screen media was installed, but the short lifespan of wire increased downtime; this, combined with employee safety risk exposure to change out the large, sharp wire sections, eliminated the wire option as a practical solution. According to McCauley, Couer had never worked with Polydeck before, but a Foreman on the site was familiar with the products and initiated contact.
Polydeck’s Mining Expert, Sam Durnavich, visited Couer Wharf to learn about the operation, production goals, and challenges the site was experiencing with its current screening set up. Upon completion of his research of the Couer mineral processing operation, the Polydeck Team worked on creating a custom solution to help the operation reach their goals and mitigate the costly plugging and blinding inefficiencies. Using a combination of Dmax, Maxi, and other specialized Polydeck panels, the team worked to maximize the production rate and screen media longevity. The Polydeck panels the team recommended were significantly more pliable than what Couer was previously using, causing a noticeable decrease in blinding along with a significant increase in saleable tonnage and throughput rates. By switching to Polydeck synthetic screen media, Couer also experienced longer changeout periods for each panel as compared to wire screens, and reduced the necessary downtime required for changeouts. In fact, with Polydeck synthetic modular screen media panels, Coeur could plan for changeouts and reduce employee labor and exposure to safety risks due to the ease of changing the individual modular panels as opposed to the danger and complexity involved with switching large wire-cloth sections. The final step in the process is for the Polydeck expert, Durnavich, to recommend a staged systematic changeout schedule, and Couer is now able to forecast and plan for each panel changeout. Planned downtime means Coeur is maximizing their screen media life, and their production rate is never affected by unplanned maintenance or downtime issues associated with screen media.
The plugging and blinding issues at Couer have been resolved thanks to the dedication of a Polydeck screening expert and his ability to select application-appropriate panels and setup a customized solution for their operation. According to McCauley, there was some initial trial and error, but Durnavich was by their side for the entire journey until they found success together. “You cannot put a price on our partnership with Sam. He is always willing to come to our site, listen to our issues, and make suggestions. When our first attempt didn’t solve our issue, he continued to work alongside us until it was. It’s so helpful having a vendor I can count on. Sam’s experience and ability to adapt Polydeck’s offering to our needs has been invaluable,” said McCauley.
After a few media iterations and with the dedication of a Polydeck expert, combined with the thousands of design options in the Polydeck screen media product line, the plugging and blinding concern at Couer Wharf is a thing of the past, and their production rate and throughput are consistently on target. With Polydeck screen media, Couer Wharf is realizing a 10% gain in recovery, improved safety, lower maintenance costs, and less downtime. Couer Wharf mines for gold, and they have struck gold in their operational targets with the help of Polydeck screen media and screening experts.
Polydeck is proud to be Certified™ by Great Place to Work®. The prestigious award is based entirely on what current employees say about their experience working at COMPANY. This year, 76% of employees said it’s a great place to work – 17 points higher than the average U.S. company.
Great Place to Work® is the global authority on workplace culture, employee experience, and the leadership behaviors proven to deliver market-leading revenue, employee retention and increased innovation.
“Great Place to Work Certification™ isn’t something that comes easily – it takes ongoing dedication to the employee experience,” said Sarah Lewis-Kulin, vice president of global recognition at Great Place to Work. “It’s the only official recognition determined by employees’ real-time reports of their company culture. Earning this designation means that Polydeck is one of the best companies to work for in the country.”
Sam Durnavich is Polydeck’s Global Mining Key Account and Product Manager, based in Denver, Colorado. Sam’s responsibilities with Polydeck have taken him from the Kazak flats to the ice capped mountains of Irian Jaya. He has traveled the world to crushing and screening plants, working to help operations find the best screen media and protective solutions to help them reduce costs and achieve their business goals. Durnavich’s experience helping commission, upgrade and operate multiple facilities has left him with what he considers a simple, holistic approach to helping mining operations combat wear and erosion, and in turn create more efficiency.
According to Sam, protective products are critical for efficiency. When used effectively, chosen correctly for your operation, and properly employed, Polydeck PROTEX - our new line of protective products - are a critical component for increasing mining operation efficiency.
How to use protective products effectively
Protective products can be game-changing for a mining operation but they must be chosen and used effectively for your specific operation’s needs. Consider standardizing size, shape and thickness to accomplish this. It no longer surprises me when I encounter an operation with a very complicated set up. Time and time again I have seen brand new plants with amazing engineering details with the most complicated wear liner packages. Some of the drawings for these chutes and transfer points require a PhD in mechanical engineering to read. They often include several different part numbers which do not match the other chutes and transfer points in the plant. This leads to a warehousing nightmare for planners but also lots of headaches for the maintenance personnel.
The best way to protect your chutes
As miners, we tend to think ‘bigger is better,’ but this is not the case with chute lining. I have found the most successful operations have standardized their chute liners to include only a few sizes, such as 1’ x 1’, 1’ x 2’ & 2’ x 2’. This reduces the quantity of part numbers stocked in the warehouse but also simplifies maintenance planning. For odd width and length surfaces to line, filler blocks can be utilized along the edges which typically don’t wear out nearly as quickly as the middle, high wear ‘hot spots’. Sometimes these ‘gaps’ can even be left unlined and material can simply fill in creating a ‘deadbed’. It’s also possible to design chutes that can accommodate basic sizes without gaps. When used in a standardized manner, equipment wear life increases and maintenance and changeout complications decrease. This all adds up to greater efficiency for the mining operation. Protecting your chutes with simpler standardized chute liners also leads to another win for your operation: increased safety.
Polydeck PROTEX products increase safety and efficiency
Safety in our facilities is always our number one priority. With some simple standard practices, we can easily engineer and eliminate hot work (cutting and welding) and handling of parts greater than 50 lbs while also reducing noise. Many large corporations now require cranes for handling of parts heavier than 50 lbs. While this mandate does improve safety, it greatly reduces productivity and adds many steps to a previously simple maintenance practice. Further, hot work creates a significant amount of extra work and hazard exposure for everyone involved. I often see hard facing in many parts of the plant which is tedious and exposes employees to hazardous welding gases unnecessarily. Having smaller, modular liners that simply bolt in completely eliminates these two hazards. Reduced maintenance, simpler changeouts, and reduced noise mean increased safety on your site.
Better wear materials mean better efficiency
We can view wear materials by seeing them as good, better, and best options for protecting our equipment. If you’ve been in Colorado’s high country doing any exploring, you certainly have seen old mining remains including loadout and transfer points for loading ore into rail cars. What’s obvious is that not only were miners good carpenters, but they also used wood as their wear and protective surface. I still encounter customers that insist on using oak wedges to keep screen side wear plates in place. These customers tell me oak is a much better choice for wear protection than pine. In my opinion, UHMW comes in a close second to wood, then polyurethane, steel & steel alloys, rubber, and finally ceramic embedded rubber. My wear material of choice? I almost always side with rubber. I have found rubber to be the best products to line chutes with. Using rubber liners not only reduces noise significantly (often as much as 10 decibels), but they also have excellent wear characteristics and are readily available in many sizes, thicknesses and fastening options.
Regardless of the challenges your mining operation faces, you can increase your efficiency by equipping your processing machinery with Polydeck PROTEX. Polydeck PROTEX are easily customizable, protect the wear life of your equipment, increase safety, and most importantly increase the efficiency of your mining operation.
Contact us today to speak with a Polydeck Expert like Sam who will assess your operation and make an individualized recommendation for the PROTEX protective products that are right for you.
Mining and aggregate operations that utilize Polydeck synthetic media experience many benefits, including a decrease in downtime with a modular system, increased media wear life, and the ability to add surface features. Polydeck surface features can either be integrated into the panel design or added onto the modular system as an auxiliary feature. This article will review molded surface features, which include dams, restricted flow bars, skid bars, and deflectors. Each can play a key role to increase efficiency when used correctly.
Dams can be molded on both POLYDEX® and RUBBERDEX® media and serve three primary roles: they slow the material flow, help build bed depth, and aid in material stratification. Injection-molded dams come in 1”, 2”, and 3” options. Dams are commonplace in many operations and may be useful to slow material on slurry-fed or incline decks, retain material under spray bars to maximize fines removal and passing of near-size material, or build bed depth in lightly loaded applications. They also stratify the material by agitating and redistributing the fines to the bottom of the material bed.
Pro Tip: For Flexi RUBBERDEX® panels with dams, Polydeck recommends installing dams oriented to the feed end for improved wear life.
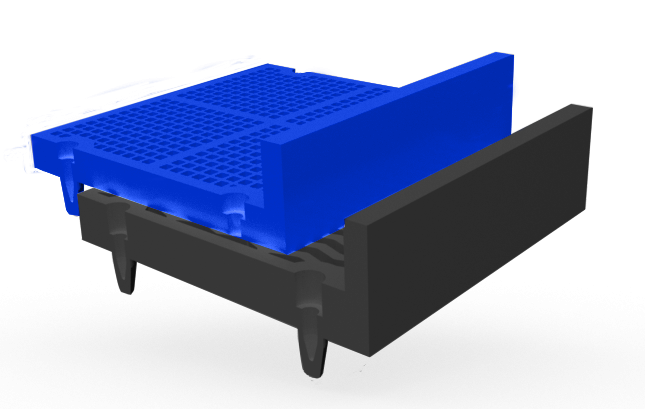
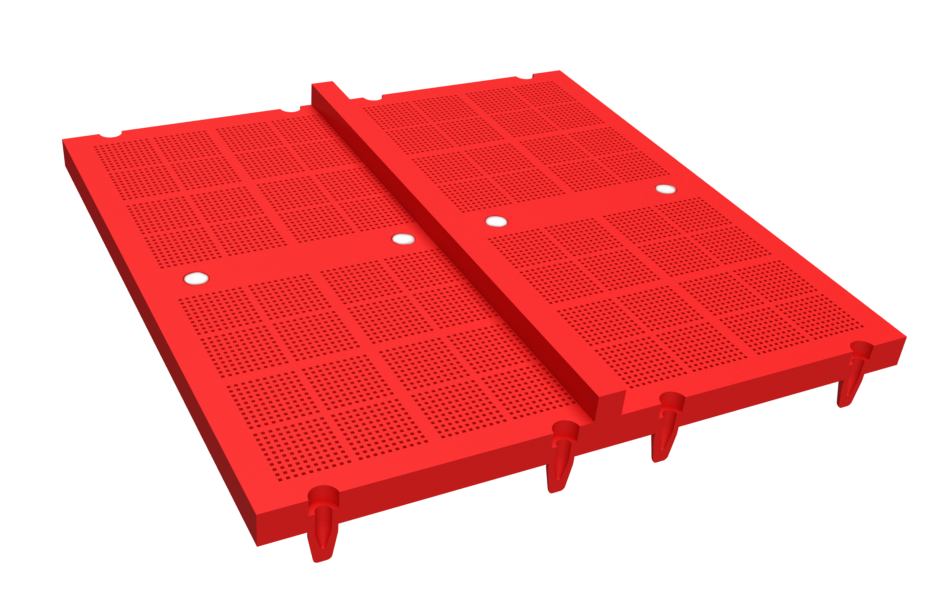
Restricted Flow Bars, or Restricted Flow Dams, consist of a multitude of low-profile dams along the surface of the panel; these are oriented across the flow of material and are available with many POLYDEX® panel designs. Similar to traditional dams, these may aid in slowing material across a deck, but they are especially effective in stratifying material.
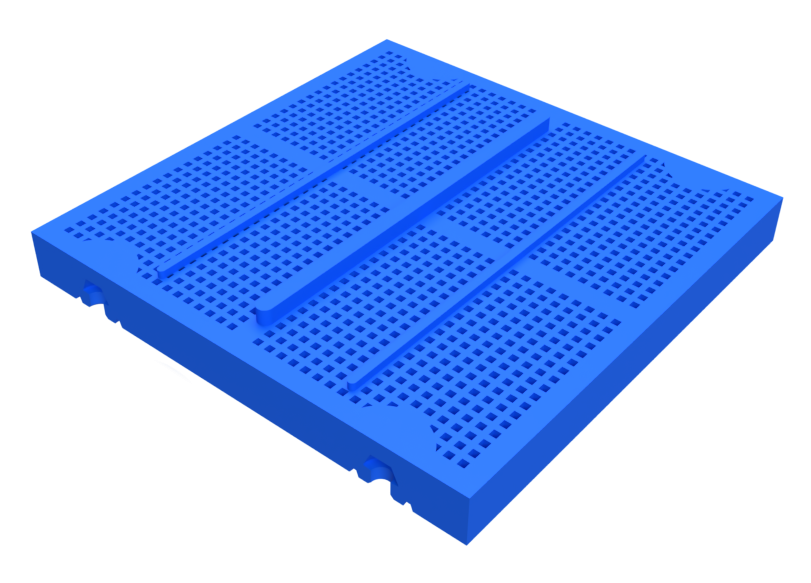
Skid Bars have similar structural form to the Restricted Flow Bars, but the orientation is with the flow of material. The main purpose for skid bar use is to increase wear life in heavily loaded or highly abrasive applications. These may be added to increase panel rigidity, as well, and are available on both POLYDEX® and RUBBERDEX® media.
Pro Tip: Use Skid Bars as stratification aids. Apertures prone to blockage by oversized material can be cleared by elevating the rocks via skid bars; this allows smaller material to pass through the panel.
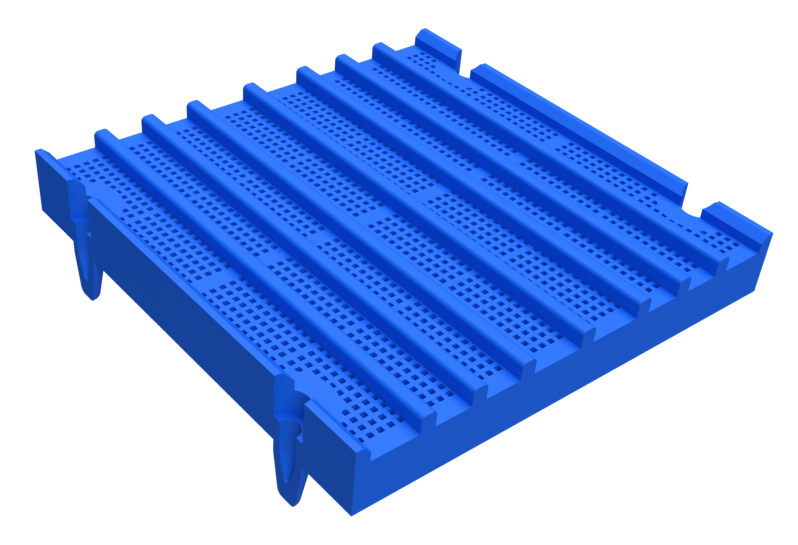
Deflectors are small protrusions intended to prevent material from channeling down the panel margins. As the name implies, these deflect the material from the margins to reroute the material over the apertured panel surface. These are highly effective on Polydeck Standard, Extended Open Area (EOP), and Polyrail panels, which carry wider lateral margins to protect channel and tube stringers.
Pro Tip: For many Standard and EOP applications, an alternative to deflector use is converting the deck support to Polydeck PIPETOP STRINGERS; this change significantly reduces the margin and increases open area with Polydeck MAXI and DMAX media.
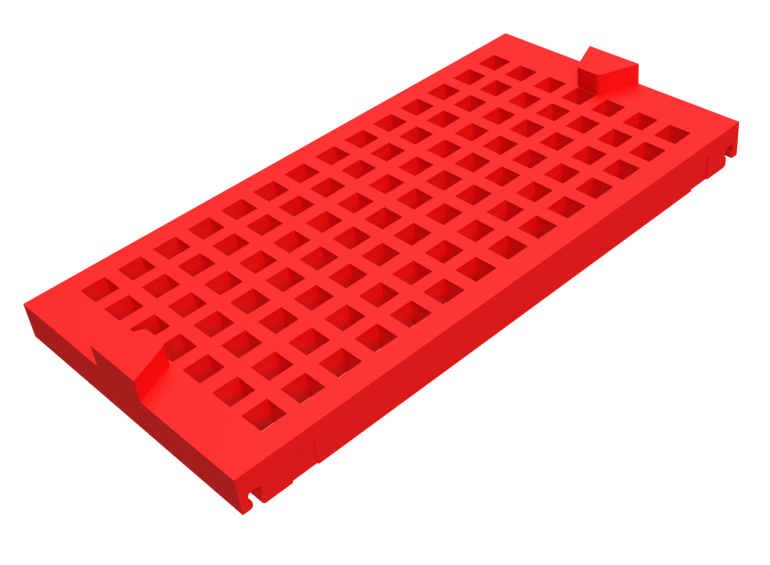
In conclusion, molded surface features are simple additions that can make notable impacts on the efficiency of many screening operations. The molded surface features smoothly integrate into most Polydeck modular media layouts and are an easy means to mitigate common screening challenges with the change of a panel.
Contact Polydeck for more information or a personalized recommendation on molded surface features and other process improvements.
Written by Jamie Mills, Product Development Application Engineer for Polydeck.