Producers often turn to what has always worked and what they are accustomed to when it comes to selecting their screen media. While wire cloth has its advantages, wire has met its match in Polydeck’s newest offering. Meet DMax, the latest in high performance, extreme open area synthetic modular screening.
At Polydeck, we’re known for relentlessly pursuing solutions to the challenges our customers face. When your operation depends upon the performance of your screen media, nothing less than the best solution is acceptable. DMax, Polydeck’s latest evolution in modular synthetic screen media provides so much throughput advantage, its open area rivals that of wire cloth while providing the durability and benefits often associated with modular synthetic screen media panels.
DMax is the result of Polydeck’s advanced material science technology that balances durability and high open area in screen media construction. This balance provides a better return on investment and a significant increase in throughput where DMax panels are used. Plant Manager Trulane Vanatta recalls the efficiency gained by using DMax panels at Morrison Quarry, “The increase in open area resulted in an 11% increase in the production of profitable 1-in. rock, and reduced fines by nearly 1%.” As any producer knows, even small reductions in fines paired with production increases is incredibly important to an operation’s profitability.
When producers initially began using synthetic screen media, it was in response to the durability the product offered them. DMax achieves the durability producers expect, along with a significant increase in available open area. DMax provides the perfect balance between wear life for uptime, and the health and safety benefits associated with reduced noise and fewer whole deck changeouts. Like all of Polydeck's modular synthetic media, Dmax can be changed out in small sections as screens wear, preventing dangerous and costly shutdowns for larger media changeouts, while preserving the benefits synthetics are known for.
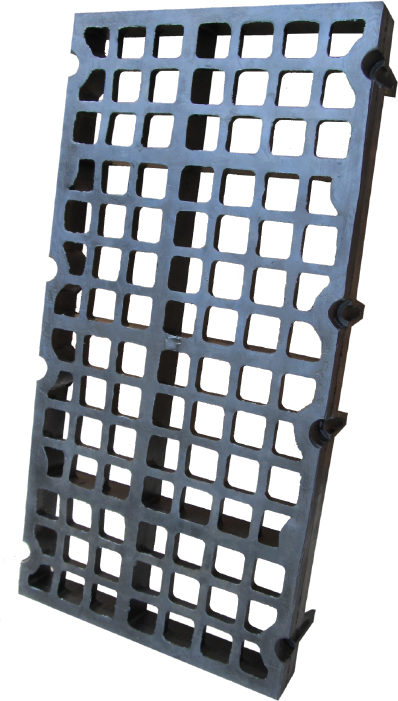
DMax panels are fully customizable, allowing Polydeck’s team of experts to create a solution that meets the unique needs of each operation. Common opening ranges can increase open area by 25-30% against standard synthetics, frequently exceeding wire's actual available open area, which is the open area actually available once bucker bars and other dead spots are accounted for. As every producer knows, open area is directly related to efficiency, thus more open area means a more efficient operation.
A Producer using cone crushers in a closed circuit could benefit significantly from using DMax. The extra open area on the screen preceding the cone crusher allows the product to reach the pile more quickly, instead of the cones. The result is extra capacity for the cone, less fines generated overall, and good salable product to pile sooner and in higher overall splits within the plant. The extra open area provided by DMax means less dust and fines and more clear stone production. This also helps decrease cone crusher wear and reduces overall power consumption since the system is being evacuated more quickly. Reduced power consumption translates to lower operational costs both in energy costs and wear on equipment.
Polydeck’s modular technology allows for easy and safe installation of DMax with other panels and use in zones where efficiency is key. DMax is ideal for use in conjunction with heavier duty panels in feed zones in order to maximize useful available open area.
DMax offers a significant weight reduction benefit over other synthetic screen media options, which reduces component wear on the screen and increases the effect of the vibrating mechanism’s stroke on particle separation. At the end of the day, it all translates to higher production levels with reduced costs.
While there are many applications where DMax can be used, producers win with DMax where there are overall blinding issues or overloaded decks leading to inefficient screening. DMax eliminates blinding and allows for more throughput. With DMax, the right size material goes through the screens, eliminating downstream bottlenecks and increasing tonnage through the plant. When durability, true open area, and reduced downtime come together, efficiency is the ultimate result. Consider DMax, the synthetic screen media that will have you rethinking your wire cloth.
Addressing the top 5 most frequently asked questions about screening.
1. I think there’s something wrong with my screen, but I don’t know if it’s worth calling in a professional to diagnose it – what should I do?
There are some visual or field tests you can run to see if it’s worth investigating a screen further. Two easy tests are:
- Travel rate. Paint 2x oversize stones, drop them onto the top deck (loaded and running) simultaneously and observe. If they travel in parallel and come off the screen together, that is a good thing. Timing the travel is valuable to let you know if your screen is running too fast or slow, too.
- Stroke/Displacement. Take a magnetic stroke card measurement of your machine at the vibrator as well as in the corners – on both sides. You’re looking for consistency between sides primarily. Deviations of more than 5% indicate a problem you should investigate further.
You can also list the symptoms of your suspected issue and give us a call!

2. How do I make my Quality Control easier to manage from a Production point of view?
Firstly, communicate! Establish clear and open understanding with your QC staff, give them a plant tour, take a tour of their world too… it’s amazing what happens when you learn about each other’s processes. Secondly, make your screening circuit as stable as possible. Eliminate stop-gap or temporary solutions like patches and silicone on screen media.
3. How do I increase my production rate?
Diligence. Observe and even out feed points, use the right combination of screen media to only apply heavy-duty media in high wear zones and high open area media on other zones. Spend some time looking at bed depth on each deck and whether the stroke is appropriate for each application. Most of the time, some patience and trying one variable at a time to see the effect is highly rewarding.
4. My media is pegging, what do I do?
First, make sure your screen has enough stroke to clear the pegging particles. Remember, you need to manually clear the pegged particles before truly knowing if a change in stroke will prevent this. If this doesn’t work, there are highly successful self-cleaning types of media in all forms – wire, rubber, and polyurethane.
5. How do I set up my spray nozzles?
Set up spray nozzles pointing at 45 degrees against the flow of material. The resulting spray should form a continuous water curtain across the screen, such that material cannot sneak through any weak spots. Working with a screen expert can help determine how many spray bars, nozzles per bar, and spacing from the deck are required, along with volume and pressure balance. Once you see a proper nozzle setup, it's easy to apply throughout your screening circuit.

**These Frequently Asked Questions were collected from a presentation by Aggregate Territory Manager, Alex Caruana. If you'd like a more in-depth online training session for your operation, feel free to contact us.
Additionally, we have provided several resources below for your convenience.
The future (and fate) of the coal industry hinges on constant innovation and the adoption of smarter, more efficient ways of doing business. Industry Expert, Ron Bennett, talks about the most effective measures needed to adapt to coming changes.
Ron Bennett has spent most of his life around coal. After working in the magnetite industry for 25 years he joined Polydeck 17 years ago in a sales position. Today, he is a Senior Industry Expert with the company, where he puts his depth of knowledge and years of experience to use as the lead application advisor for their entire coal division.
In addition to overseeing fleet and safety responsibilities, Ron works closely with Polydeck’s customers in the energy and industrial industry to help develop groundbreaking solutions to their production challenges. His advice is critical in helping both Polydeck and its customers decide on the most effective courses of action to take in response to new trends and shifts in the industry.
Lately, he’s been keeping his eye on the plummeting price of coal and thinking about what it might mean for the future of energy production in the US—particularly the costs of doing business for coal processors.
“Demand is at a near all-time low,” Ron notes grimly, “The price has bounced back a bit from the record warm winter we saw last year, but there’s still lots of stockpile on the ground and parts of the country saw a mild winter again this year. The price is currently around $40 a ton for steam coal and $85 a ton for metallurgical coal—and that’s not good. We’ve already had two major coal companies go bankrupt as a result, so the domestic industry today faces a huge challenge.”
Despite the downward trends, Ron sees opportunity for processing plants to shift their cost burden in a positive direction by making operational changes that reduce their processing costs. These costs include a variety of production factors, such as planned or unplanned downtime, screen efficiency, proper sizing, magnetite recovery, and maintenance. Every point of improvement has some effect on an operator’s overall costs; collectively, however, they can have a tremendous impact on the bottom-line.
The energy and industrial team at Polydeck has over 150 years of industry experience and they understand the difficulties operators face in bringing production costs under control. As Ron puts it, “If someone has a coal issue, you can be sure we’ve dealt with it before.”
Polydeck relies on the team’s combined knowledge and their strong relationships with its customers to help the company design and manufacture innovative products that drive those costs down.
Reducing Costs on the Scalping Screen
Raw coal scalping can be a problem when there is a high presence of clay in the run, which makes the coal “sticky.” As the coal passes through the screen deck, the clay adheres to the screen and clogs up the apertures, slowing the production flow and creating inefficiency. Eventually, the run has to be paused while a crew clears the screen deck of clay—a costly work stoppage by any measure.
“I’ve seen an operator have to shut down three times in a single shift to clean their deck,” Ron recalls, “That makes the run really expensive to clean, process, and put in a car. These days, that just won’t cut it.”
To address these types of applications, Polydeck developed specialty rubber products. Because the rubber panels are extremely flexible, they shed the clay and maintain the screen’s efficiency. Not only does the pass-through volume stay consistent, but by not having to shut down the screen to clean off the clay, the operator also saves a lot of downtime and labor costs.
Polydeck’s polyurethane products for raw energy and industrial applications similarly reduce maintenance and downtime costs by providing superior wear life and fast, easy change out. These products are a direct result of Ron and his team working closely with customers to understand what they need their equipment to do.
Reducing Costs in Drain-and-Rinse Applications
Drain-and-rinse applications wash magnetite off coal and allow operators to recover the material, which is important because magnetite prices are at an all-time high. Just a few years ago, magnetite sold for around $90 per ton. Now, because magnetite is no longer domestically produced, the import and shipping costs—along with a lack of competition—have driven up the price to over $300 per ton.
This makes magnetite recovery a profitable task, but it also presents a completely different challenge for processors. In this case, particularly, getting the correct size distribution on the screens is critical to ensuring that the maximum amount of magnetite product is recovered.
To ensure proper sizing and drain rates, Ron advises clients to adopt a solution that incorporates Polydeck VR panels on the top deck with continuous slot panels or profile wire panels on the bottom decks: “The easy change out can dramatically lower an operator’s maintenance costs and decrease their downtime.”
Reducing Costs in Recovery Applications
Consistency is key in any business, but it’s of extreme importance in the fine coal circuit, where recovery can come down to a mere .02 mm difference in size. Ensuring consistency gives the operator the confidence that they’re putting 100 percent of their product on the ground and not throwing away valuable product due to inefficiency.
“Producing consistently sized panels is one of Polydeck’s core competencies, and it’s a strong selling point for our products” Ron explains, “All of our rubber and urethane panels are manufactured with an injection-molding process that produces a consistent aperture size from panel to panel. We even back it up with a product performance guarantee: If our panels are ever not to the customer’s spec, we’ll replace them at no cost.”
Reducing Costs in the Supply Chain
An often overlooked area in which an operator can reduce their operational costs is in the ordering and fulfillment phase of supply inventory. An operator who partners with a supplier that has sufficient warehousing and logistics can keep less stock on site and instead rely on rapid delivery of replacement stock to maintain profitable production levels.
Again, Ron points to Polydeck as a good example of the type of partner an operator can leverage to help reduce their costs: “[Polydeck’s] products are manufactured in Spartanburg, SC and stored in three distribution centers strategically-located in the eastern US coal fields—in Morgantown, WV; Chapmanville, WV; and Ridgeway, IL. Additionally, Polydeck has strategic partners in Eastern and Western Canada who store product for customers so that they are on hand when needed. This means that we can guarantee availability of product and fast delivery to the customer—usually by the next day. It also means the customer can save more money by reducing their stocked product levels.”
The Future of Cost-Savings
Ron regularly sees the benefits of greater efficiency when dealing with customers. “The maintenance savings alone with a modular deck is substantial,” he explains, “I was working with a processing operation to help them transition to a new modular Polydeck screen. While I was there, the supervisor and I watched his crew change out their old metal screen. It took four guys with torches and impact tools several hours to do the work.”
This kind of downtime and labor-intensive maintenance was killing the client, but with a new Polydeck screen, it would only take a single team member a few minutes to swap out a 1x1 panel. After installing the Polydeck screen, the customer saw a dramatic improvement in the entire plant.
“When I went back,” Ron says proudly, “the supervisor told me to walk the plant and report back what I found. The facility was the cleanest I had ever seen, and the entire production was running smoothly. When I told him so, he said, ‘That’s exactly what I wanted you to see; my guys have more time to take care of other things instead of constantly replacing screens.’”
This is the sort of opportunity for change and improvement that Ron sees taking place for operators across the country. “The industry is going through a sea of change as the world transitions from traditional fossil fuels to other forms of power generation. Just last year, coal dropped below 50% of all forms of power generation for the first time.”
He remains positive about the future, however. “Look, everyone needs to remember that coal still keeps the lights on. Despite all the changes around us, coal isn’t going anywhere for the time being.”
Coal processors know that they have to make changes to adapt to the new realities in order to remain profitable. The easiest way to do that is to examine their operation from top-to-bottom, find those areas where improvements can be made, and then partner with vendors who can help them implement those improvements.
Without the capacity to overcome production bottlenecks and inefficiencies, increase the productivity value of their work force, and maximize the quality and consistency of the product throughput, processing operations could be forced to shutter if the cost of coal continues to drop.
The good news for operators is that they aren’t alone. Companies like Polydeck, and experts like Ron Bennet and his team, work hard to come up with solutions to the production challenges facing coal processors. They know that the future (and fate) of the industry hinges on constant innovation and the adoption of smarter, more efficient ways of doing business.
Necessity is the mother of invention. In fact, that’s how Polydeck was born, when Manfred Freissle saw the necessity for something that functions better than wire cloth.
Fast forward to today, when Polydeck has well over 1,000 dies, numerous materials and surface features – and still, when there is a need to perform yet a new and different function, Polydeck will invent all over again. Keep reading to learn all about how our panels go from ideation to production!
1. The Challenge
The challenge shows itself. Quite simply, this is the ‘necessity’ part where an Aggregate, Energy and Industrial or Mining operation needs to do something differently. When Polydeck confirms this challenge requires a new panel as the solution, we get inventing!
2. Information is Gathered
Polydeck collects all sorts of information: What type of material is being processed? How is the material crushed, what are its challenging characteristics? Has a different panel been tried? All this information helps us to create the best possible solution for our screening partners.

3. Design. Design. Design.
Given the information collected in partnership with our customer, we get down to designing the new panel. Considerations like surface features (dams, restricted flow bars), fastening, amongst others, which may not be part of the initial necessity, ensure this new panel will be as modifiable as possible to offer the wonderful traits of modular media. The panel is drawn up and reviewed by multiple parties, which ensures no detail is missed.
4. Test the Panel
The proof is in the testing. The panel is developed and tested, eventually making it to our large offering of dies and corresponding panels. We also assign the new panel a color to make more easily differentiate it from similar panels.
5. Finished!
And then it’s here. While there’s no baby shower for it, we all celebrate the birth of a new panel, since it offers us yet a new set of functions to help our screening partners.
Written by Alex Caruana, Aggregate Territory Manager for Polydeck.
When you eliminate top-deck bottlenecks, you increase production capacity and put more saleable product on the ground. Read about how Polydeck assisted with a higher level of efficiency in a cost-effective way.
If you’re running an aggregate plant, then you know that the efficiency of your top-deck screens is critical to your operation’s overall performance. It’s a simple formula: When you eliminate top-deck bottlenecks, you increase production capacity and put more saleable product on the ground. But how can operators achieve that level of efficiency in a cost-effective way?
Polydeck’s answer to this question is a screen media equation that combines modular welded-wire screen panels with synthetic media panels. Each modular panel type is strategically-located on the top deck to deliver maximum open area and superior wear life. For operators, the result is greater throughput and reduced maintenance downtime = more profit and fewer expenses.
Polydeck partner, Alleyton Resources, is an aggregates and ready-mix concrete producer headquartered in Houston, TX. Their operations include 11 RMC sites and eight aggregate processing locations, and they provide material transportation, ready mix concrete delivery, concrete pumping, and stabilized sand and slurry to their customers.
Brandon Genzer (Plant Manager at Alleyton’s Vox Plant in Garwood, TX, at the time) was dealing with coarse deposits at the site as well as difficulties vacating the top deck of their wet secondary, inclined finish screen, which was fitted with polyurethane media.
“The screen is being fed 2-1/2-in.-minus material,” he explains, “We had a lot of carryover of 1-1/2-in. material, which created unnecessary recirculating loads going back to the crusher.”
This was a huge problem for their operation because recirculating loads significantly increase both crusher wear and per-ton operating costs. It was sapping the facility’s profit margins by sending finished product back to the crusher instead of to the saleable product stockpile.

To eliminate this costly carryover issue, Genzer consulted with Polydeck’s manager for the South Texas region at the time, Kent Ropp. “I work closely with each producer in my area to analyze their application and create modular screen panel configurations that deliver the desired specifications.”
Ropp worked with Genzer to specify the new media by conducting several hours of run time for each sample of material. “We would plug in different media to dial in our FM [fineness modulus] to just where we needed it,” Genzer recalls.
Ropp ultimately recommended a combination of Polydeck’s high-performance products. For greater open area and throughput, Polydeck’s METALDEX™ modular steel screen media panels were installed on the discharge end of the facility’s 6-ft. x 16-ft. screen. To absorb the impact on the feed end of the screen, RUBBERDEX® synthetic rubber panels were installed for maximum top-deck wear life. The middle and bottom decks were outfitted with POLYDEX® modular polyurethane screen panels.

The METALDEX™ panels offer open area that equals or exceeds traditional wire cloth of the same aperture and wire diameter. In addition to greater open area, the modularity of the panels allows operations to apply them at the feed end or, more importantly, at the discharge end where increased open area is critical in eliminating recirculating loads.
Tests conducted by Ropp at the Vox Plant determined that the addition of Metaldex panels to the discharge end boosted screen performance to 55.9% open area over the 33.4% rating they achieved with the previous synthetic rubber panels.

“We’re getting good wear life on the panels as well,” Genzer reports, “Even under extended 12- to 16-hour shifts, the first set lasted more than four months. When we extend hours, we check the screens at the end of every shift. If need be, the crew can change out panels in a matter of minutes, and we’re back up and running.”
According to Ropp, the key to METALDEX’s greater wear life is that: “It’s comprised of abrasion-resistant AR 500 Brinell steel, which extends wear life in most applications against that of standard wire cloth. Welded wire simply delivers a higher degree of performance in strength and corrosion resistance.”
Another bonus for the Vox plant is that METALDEX™ panels scrub the material better, removing the clay content. “We’re getting the best of both worlds now—cleaner rock at a higher throughput,” says Genzer, adding that the plant averages 550-tons per hour, a significant increase since the screening circuit was fine-tuned. Alleyton has since implemented a METALDEX™ screen at another operation to help break up and eliminate the clay content in their material.
Because processing flexibility is important at the Vox facility—which primarily produces 1-1/2-in.-minus material, 3/8-in.-minus material, and concrete sand—the modularity of the screen panels enables them to easily change out panels or fine-tune configurations to accommodate varying material feeds or processing requirements. The borders of each 1-ft x 2-ft welded wire panel are encased in polyurethane, as well, making them much easier to handle than large wire cloth sections.
“METALDEX™ is another groundbreaking screen panel design from Polydeck that enhances the range of screen media solutions and help our customers beat their production goals,” says Ropp. “It offers the extended wear life of abrasion-resistant steel with the open area of wire cloth, and the modular engineering allows for easy handling and simple attachment to Polydeck’s stringer frame system.”
Eliminating screening bottlenecks is essential to maximizing throughput on top-deck screening, which is, in turn, critical to optimal plant performance. At Alleyton Resources’ Vox Plant, Polydeck’s innovative combination of welded wire and synthetic media panels was the precise formula to solve their screening problems.

In 2020, Polydeck launched a new product offering- METALDEX™ VR. Polydeck’s new modular wire screen solution integrates with our PIPETOP™ stringer system. Perfect for dry-sizing applications where more open area and efficiency is required, METALDEX™ VR is ideally installed on the discharge end, where it provides longer wear life and better throughput, and its unique, diamond-shaped pattern eliminates blinding and plugging.