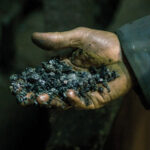
Reducing costs and maximizing efficiency are winning strategies for profitability
January 12, 2021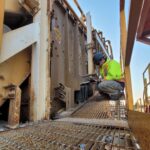
Screening Problems Solved and Frequently Asked Questions
January 12, 2021Learn the most important factors that you should take into account when selecting your screening equipment.
When it comes to manufacturing screen media for aggregate, energy and industrial, and mining use, making them pretty is the easy part. The hard part is selecting the best solution to deliver the greatest functionality in order to meet the customer’s needs. There’s an art and science that lies behind designing screen panels for superior form and function. That’s because there are so many variables at play. The most effective screen media selection will include a mix of apertures and surface configurations tailored to the needs of each screening application to enhance capacity, reduce costs, and minimize downtime.

Tip #1: Get Started by Looking at the Big Picture
The most important exercise when selecting screening equipment is taking stock of the entire screening circuit. This will help determine the best materials to be used, as this evaluation impacts many factors. Polyurethane and rubber are popular screening materials, but have significant differences. Polyurethane has higher abrasion, cut, and tear resistance and is used mostly in wet applications. It can be made in a higher hardness rating, and it has better load-bearing capacity than rubber. Rubber is favored in dry applications and offers excellent anti-blinding characteristics at a lower (softer) durometer. Both polyurethane and rubber are significantly less noisy to operate than steel screen media and modular screen panels offer the greatest control in meeting product specifications because of their ability to customize the deck surface in 1-foot increments.

Tip #2: Calculate Correctly
Open area of the screen media is a common measure of screening efficiency but must be properly calculated in order to avoid bottlenecks in the screening circuit. For example, on wire cloth installations, apertures can be blocked by bucker bars, crown rubber, side clamp rails, and center hold-downs, so failing to consider these factors can throw off calculations by as much as 40%. It’s important to calculate the total number of “usable” openings on the screen by looking at the percentage of open holes versus the area of the entire screen panel surface. Also, thinner bridges allow greater open area that can remove further incidences of bottlenecking, and result in a more efficient process. However, the downside of thinner bridges can be decreased wear life of the screen panel. Remember that precise data yields smart screen panel selection for maximum productivity.

Tip #3: Consider Other Factors
The screen panel support system can also impact the open area of the screen. One that features ½” wide attachment rails like Polydeck’s PIPETOP allows for maximum open area. Look at the panel support structure of the deck frame to evaluate how it might adversely affect the open area of the deck surface. Another important consideration — weather and environmental factors like high humidity, which can lead to blinding problems. Mitigate these factors with anti-blinding screen panels, which require less attention which helps to minimize downtime for maintenance.

Tip #4 : Ask Questions
Establishing an efficient screening solution requires one to be proactive rather than reactive. Some questions to consider before choosing your screen media include:
- Is the material wet or dry?
- Is blinding or pegging an issue?
- Is noise a concern?
- How abrasive is the material?
- How might weather or climate be an issue?
Screen media suppliers with a great number of screen panel options, fastening configurations, and surface features are best positioned to answer these questions in order to provide the most effective screening solution for you.
As a leading provider of screen media solutions, Polydeck’s screen panels are created using an injection molding process to ensure accurate openings and consistent construction — panel after panel. Don’t hesitate to contact us if you have any questions!