It’s easy to be complacent with screen media solutions that require downtime for cleaning and replacement. Improve your throughput, reduced downtime and increased production with the maximum open area and ease of use of Polydeck's Maxi Panels.
In an industry dating back tens of thousands of years, it’s easy to become complacent when considering success factors and efficiencies in your operation. However, it’s more than possible to design an operation that is efficient and advanced with the right screen media. Polydeck’s Maxi panel screen solutions increase an operation’s throughput and production efficiency in countless ways.
Throughput is, simply put, a production and success measure. In terms of material processing, it means your screen media is doing its job. Efficient screen media meets your machines where they are, allows for ease of cleaning and replacement, and provides maximum screening of material with as little downtime as possible. For many operations, efficiency is critical especially where resources are limited. Stopping to clear plugs and dealing with low open area is simply not an option when efficiency and sustainability are required of the site.
If screen media is not performing as it should, costly stoppages result, requiring workers to spend hours clearing plugging and getting screens to a place where they can begin production again. Polydeck customer Dufferin Aggregates Butler Pit, located in Cambridge, Ontario was experiencing significant downtime from pegging. With a constant focus on their efficiency and production goals, Dufferin did not waste their time seeking a better screen media solution. After the Polydeck team conducted an on-site screen performance analysis and presented their solutions with a guarantee that Dufferin would experience their desired throughput by making the switch, the choice was simple.

Maxi panels’ thin borders are specifically designed with throughput in mind, featuring relief angles to aid in proper screening. Once the panels were put on our customer’s screens, they provided maximum number of openings per square foot. Besides offering leading throughput rates, Maxi panels’ specially formulated polyurethanes combined with engineered panel geometry allowed the panels to flex and retain extended wear life. This innovative design coupled with Polydeck’s injection molding process ensured accurate, consistent open area which resulted in increased overall efficiency at Butler Pit.
Maxi panels also offer an advantage over wire cloth when considering the abrasion resistance of synthetic screen media and ease of use. Operations often default to wire cloth when production requirements are high but Maxi panels offer a significant cost benefit when you factor in downtime needed to change out wire cloth. Maxi panels’ modularity and snap fastenings make changeouts and swaps easy and quick. Less downtime means more productive hours on site. More production means more return from your site. In short, adding Polydeck’s Maxi panels to your operation means you’ll get more from your site than ever before.
The keys to success with screen media lie in today’s technology and the efficiency found in Polydeck’s Maxi panels. As seen at our customer’s site, Polydeck’s Maxi panels reduced downtime and increased production, two very critical elements for success in any operation.
Are you ready to increase the success of your operation?
When you eliminate top-deck bottlenecks, you increase production capacity and put more saleable product on the ground. Read about how Polydeck assisted with a higher level of efficiency in a cost-effective way.
If you’re running an aggregate plant, then you know that the efficiency of your top-deck screens is critical to your operation’s overall performance. It’s a simple formula: When you eliminate top-deck bottlenecks, you increase production capacity and put more saleable product on the ground. But how can operators achieve that level of efficiency in a cost-effective way?
Polydeck’s answer to this question is a screen media equation that combines modular welded-wire screen panels with synthetic media panels. Each modular panel type is strategically-located on the top deck to deliver maximum open area and superior wear life. For operators, the result is greater throughput and reduced maintenance downtime = more profit and fewer expenses.
Polydeck partner, Alleyton Resources, is an aggregates and ready-mix concrete producer headquartered in Houston, TX. Their operations include 11 RMC sites and eight aggregate processing locations, and they provide material transportation, ready mix concrete delivery, concrete pumping, and stabilized sand and slurry to their customers.
Brandon Genzer (Plant Manager at Alleyton’s Vox Plant in Garwood, TX, at the time) was dealing with coarse deposits at the site as well as difficulties vacating the top deck of their wet secondary, inclined finish screen, which was fitted with polyurethane media.
“The screen is being fed 2-1/2-in.-minus material,” he explains, “We had a lot of carryover of 1-1/2-in. material, which created unnecessary recirculating loads going back to the crusher.”
This was a huge problem for their operation because recirculating loads significantly increase both crusher wear and per-ton operating costs. It was sapping the facility’s profit margins by sending finished product back to the crusher instead of to the saleable product stockpile.

To eliminate this costly carryover issue, Genzer consulted with Polydeck’s manager for the South Texas region at the time, Kent Ropp. “I work closely with each producer in my area to analyze their application and create modular screen panel configurations that deliver the desired specifications.”
Ropp worked with Genzer to specify the new media by conducting several hours of run time for each sample of material. “We would plug in different media to dial in our FM [fineness modulus] to just where we needed it,” Genzer recalls.
Ropp ultimately recommended a combination of Polydeck’s high-performance products. For greater open area and throughput, Polydeck’s METALDEX™ modular steel screen media panels were installed on the discharge end of the facility’s 6-ft. x 16-ft. screen. To absorb the impact on the feed end of the screen, RUBBERDEX® synthetic rubber panels were installed for maximum top-deck wear life. The middle and bottom decks were outfitted with POLYDEX® modular polyurethane screen panels.

The METALDEX™ panels offer open area that equals or exceeds traditional wire cloth of the same aperture and wire diameter. In addition to greater open area, the modularity of the panels allows operations to apply them at the feed end or, more importantly, at the discharge end where increased open area is critical in eliminating recirculating loads.
Tests conducted by Ropp at the Vox Plant determined that the addition of Metaldex panels to the discharge end boosted screen performance to 55.9% open area over the 33.4% rating they achieved with the previous synthetic rubber panels.

“We’re getting good wear life on the panels as well,” Genzer reports, “Even under extended 12- to 16-hour shifts, the first set lasted more than four months. When we extend hours, we check the screens at the end of every shift. If need be, the crew can change out panels in a matter of minutes, and we’re back up and running.”
According to Ropp, the key to METALDEX’s greater wear life is that: “It’s comprised of abrasion-resistant AR 500 Brinell steel, which extends wear life in most applications against that of standard wire cloth. Welded wire simply delivers a higher degree of performance in strength and corrosion resistance.”
Another bonus for the Vox plant is that METALDEX™ panels scrub the material better, removing the clay content. “We’re getting the best of both worlds now—cleaner rock at a higher throughput,” says Genzer, adding that the plant averages 550-tons per hour, a significant increase since the screening circuit was fine-tuned. Alleyton has since implemented a METALDEX™ screen at another operation to help break up and eliminate the clay content in their material.
Because processing flexibility is important at the Vox facility—which primarily produces 1-1/2-in.-minus material, 3/8-in.-minus material, and concrete sand—the modularity of the screen panels enables them to easily change out panels or fine-tune configurations to accommodate varying material feeds or processing requirements. The borders of each 1-ft x 2-ft welded wire panel are encased in polyurethane, as well, making them much easier to handle than large wire cloth sections.
“METALDEX™ is another groundbreaking screen panel design from Polydeck that enhances the range of screen media solutions and help our customers beat their production goals,” says Ropp. “It offers the extended wear life of abrasion-resistant steel with the open area of wire cloth, and the modular engineering allows for easy handling and simple attachment to Polydeck’s stringer frame system.”
Eliminating screening bottlenecks is essential to maximizing throughput on top-deck screening, which is, in turn, critical to optimal plant performance. At Alleyton Resources’ Vox Plant, Polydeck’s innovative combination of welded wire and synthetic media panels was the precise formula to solve their screening problems.

In 2020, Polydeck launched a new product offering- METALDEX™ VR. Polydeck’s new modular wire screen solution integrates with our PIPETOP™ stringer system. Perfect for dry-sizing applications where more open area and efficiency is required, METALDEX™ VR is ideally installed on the discharge end, where it provides longer wear life and better throughput, and its unique, diamond-shaped pattern eliminates blinding and plugging.
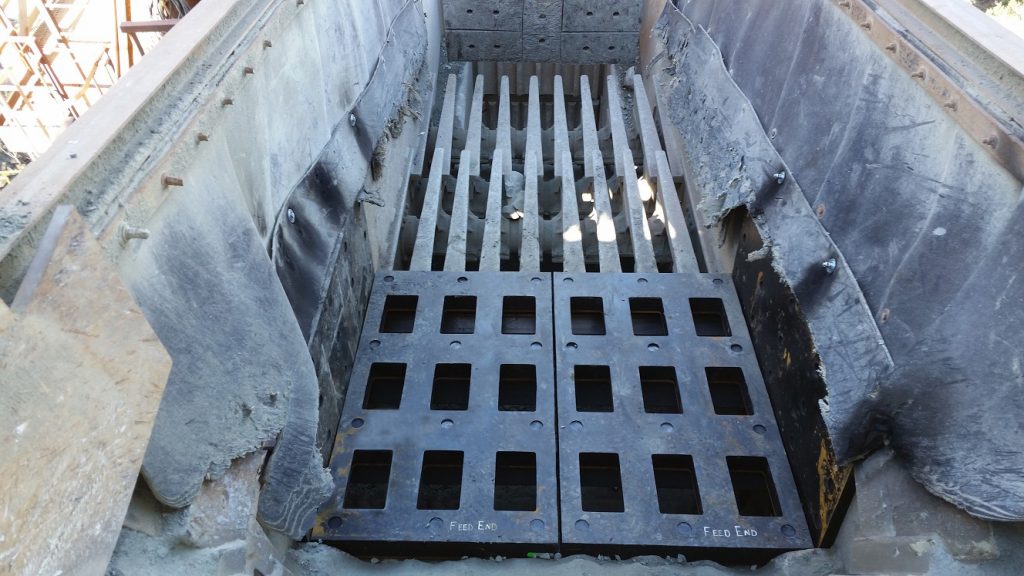
Efficient scalping is essential to the optimum performance of primary and secondary crushing circuits. To increase scalping efficiency, the Hanson operation installed ARMADEX custom rubber sections to the second step - with the third step soon to follow.
Quite simply, production capacity and wear life increase when fines are removed from the primary jaw feed; when overs are fed to the jaw; and when material sized below jaw crusher settings pass through the grizzly bars for further crushing and sizing.
However, in extremely abrasive, high-impact, high-wear applications, achieving the optimum scalping efficiency can be challenging.
Problem-Solution
To lower operating costs per ton while meeting market demand for high-quality asphalt and concrete aggregate, Lehigh Hanson's California-based Clayton Quarry sought to eliminate any existing or potential bottlenecks throughout its plant. Serving the San Francisco Bay region, the Clayton Quarry is one of 200 aggregate production sites and distribution terminals owned by Hanson, which produces aggregate, asphalt, ready-mix concrete and other building materials throughout North America.
“Our pit is a drill-and-blast hard rock quarry that was started in 1956,” says Marc McNeil, plant manager of the Clayton Quarry. “Since the late 1990s, our focus has gradually shifted from base rock production to crushed stone and manufactured sand, and our aging plant required some upgrades from initial feed to product finishing.”
Marc McNeil, plant manager at Lehigh Hanson’s Clayton Quarry, oversees current plant upgrades, from initial feed to product finishing.
The improvements began by tackling scalping and sizing challenges. The Clayton Quarry’s tough, high-impact shot rock scalping application involved extreme wear, as well as excessive maintenance costs and labor to replace and repair worn grizzly bars.
Ultimately, the Clayton Quarry chose a customized scalping solution designed and manufactured by Polydeck. ARMADEX is a custom rubber screening product that was applied in bolt-down sections to the first step (5 ft.) of the plant’s vibrating grizzly feeder.
“Since installing ARMADEX, we’ve significantly cut maintenance downtime and wear costs – to the point where we eventually applied ARMADEX to the second step of the grizzly, with plans for installation on the third step currently underway,” McNeil says.
High-Impact Scalping Challenges
The Clayton Quarry mines a diabase rock that is hauled down to the primary crushing plant and loaded into a 150-ton hopper.
To cut maintenance downtime and wear costs, a custom rubber screening product, ARMADEX, was applied in bolt-down sections to the first step of the grizzly.
A pan feeder takes the 24-in.-minus topsize material from the hopper and feeds it to the vibrating step grizzly. The grizzly is highly impacted, as material drops 12 ft. before hitting the grizzly bars. The impact on steel media generated considerable noise while also causing the feed end of the grizzly to wear excessively.
In addition, the fine feed from the pit often caused the first set of grizzly bars to bridge over.
“The bars are bolted to a support bar, but with the bridging and the excessive wear, the bars would start to move and open up, allowing larger rock through,” McNeil says. “When that oversize rock gets through to the secondary circuit, the cone crusher becomes less effective.”
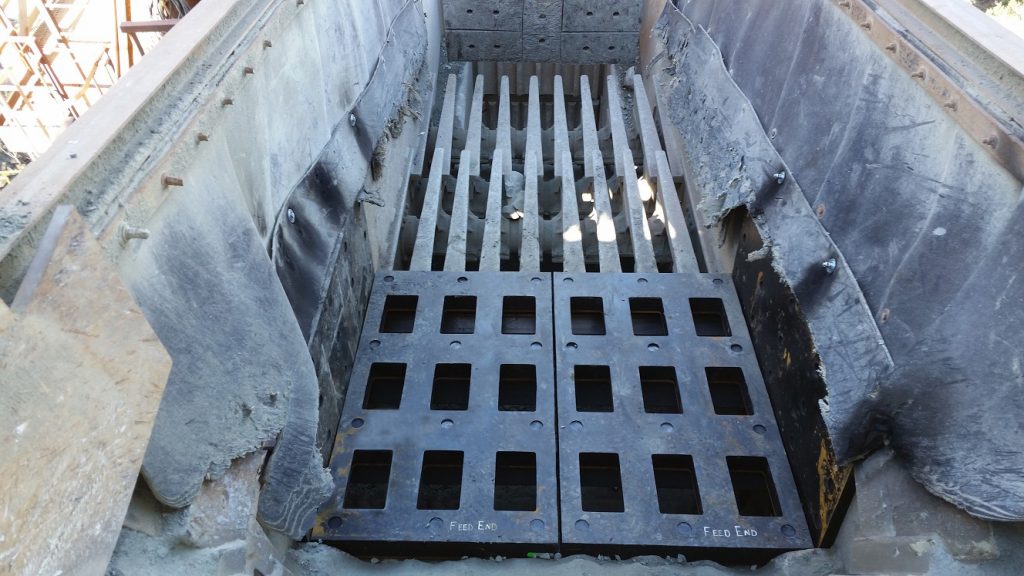
Most important, additional maintenance downtime and labor costs came into play. The movement of the grizzly bars required up to 20 hours per week of welding to secure them into place, McNeil says.
“For safety, working on a grizzly requires being harnessed,” he adds. “So if a worker is welding bars on a regular basis, it becomes quite challenging. We tried replacing the entire set of bars and it was very costly. There had to be another way.”
Customized Scalping Solutions
Throughout its finishing plant, on both wet and dry screens, the Clayton Quarry uses Polydeck modular synthetic polyurethane and rubber screen media panels.
The Clayton Quarry utilizes modular synthetic polyurethane and rubber screen media panels throughout its finishing plant on both wet and dry screens.
“We’ve had good results with their screen media products, so we asked Polydeck application engineers to assess our scalping circuit to see what could be done,” McNeil says. “They proposed using ARMADEX, a media highly suitable for tough, abrasive top-deck scalping applications. We decided to try it out on the first step of the grizzly – and we saw immediate benefits in reduced maintenance downtime and wear costs.”
As Polydeck’s Peter Babinski stresses, aggregate producers want maximum uptime, minimal maintenance, increased wear life and noise reduction – particularly in abrasive grizzly feeder applications. Producers often look to synthetic media solutions for those benefits, he says.
As Babinski explains, ARMADEX rubber screen media uses high-pressure injection-molding technology, a Polydeck manufacturing method that produces 10 times the pressure normally used to produce compression-molded rubber.
“Combining this technology with our premium gum rubber compound and HSLA steel plate backing produces unprecedented strength in a media product that delivers far longer wear life at lower costs per ton,” says Babinski, who serves Polydeck as West Coast/Mountain States aggregate territory manager.
“With grizzly bars, operations can’t adjust them unless they completely change them out or weld on them to change the apertures,” Babinski says. “ARMADEX bolt-in sections give us the flexibility to access smaller or larger apertures to fine-tune performance in a given application.”
To install ARMADEX sections on the grizzly feeder at the Clayton Quarry, Polydeck engineered a custom frame that bolts to the side panels of the grizzly. The ARMADEX sections are easily bolted onto that frame.
“It was a simple, drop-in replacement for us with very little downtime, due to Polydeck’s attention to detail regarding the customization to our application,” McNeil says.
Scalping and Sizing Efficiency
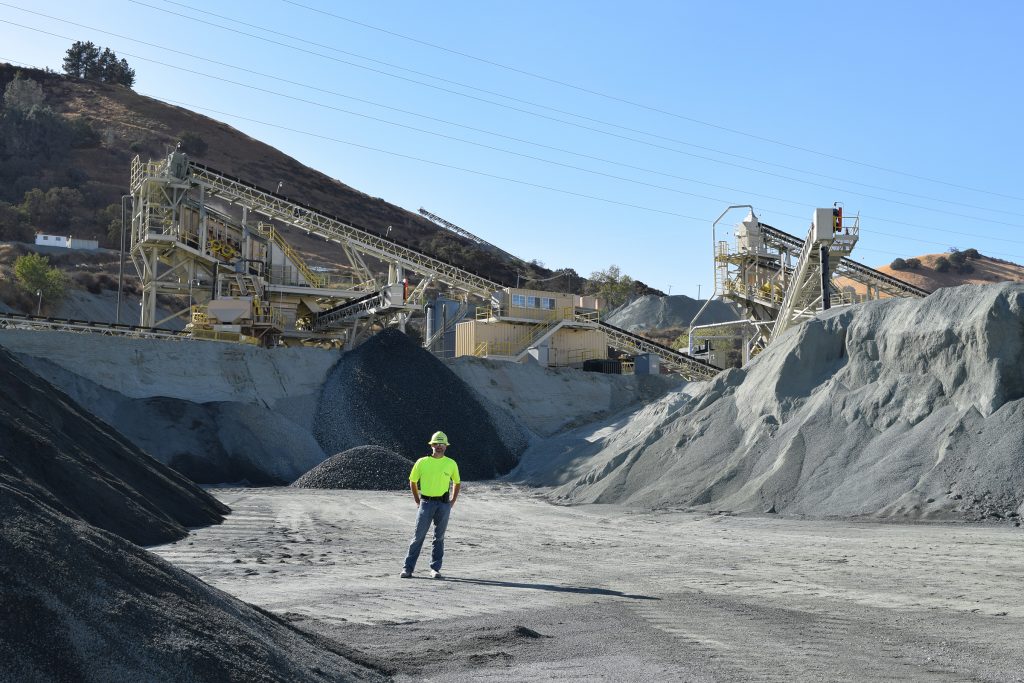
According to McNeil, the operation has greatly improved day-to-day scalping and sizing efficiencies by using ARMADEX media sections. By preventing oversize material from passing through to the cone crusher, the operation boosted crushing performance while reducing downtime.
“We’ve drastically cut maintenance costs, as we have yet to change out an ARMADEX section since their installation – and they require no weekly welding,” says McNeil, adding that the media sections on the first step of the grizzly have processed a material throughput of nearly 3 million tons over three production seasons.
The Clayton Quarry continues to work with Polydeck to further fine-tune performance. The scalping circuit will employ round apertures in the ARMADEX sections used on the third step of the grizzly feeder, increasing throughput of angular rock that may become wedged in square or rectangular openings.
By tweaking scalping circuits at the top of the chain, those that follow see less wear and tear, higher production capacities and more saleable products through to the stockpiles.
Written by Carol Wasson, veteran freelance writer for the aggregate and construction equipment industries.
LafargeHolcim, a global leader in building materials and solutions, is an active producer in the Cement, Aggregates, Ready-Mix Concrete and Solutions & Products business segments of the industries the Company serves. As a company whose business is centered on the use of natural materials, LafargeHolcim is acutely aware of their responsibilities from a sustainability perspective. Recently, the company’s Leadership Team made it evident that sustainability is a key component of their business strategy and something they are actively evaluating at each site with their annual reporting. Considering the environmental and sustainability impact of each of their operations and sites is critical to their success as a company that relies upon natural materials.
LafargeHolcim’s Woodstock, ON, Canada quarry experienced quite the breakthrough in sustainability for the operation and ultimate usable material throughput thanks to Polydeck’s industry-leading spray nozzle technology. The Woodstock quarry was previously heavily involved in extracting and processing limestone deposit, a key building material. The operation historically focused on the blasting, extracting, crushing, and screening of limestone. As a feeder plant for a nearby cement plant, the quarry’s operation viability was clear. However, when the market for limestone changed, the operation found it critical to adapt to the changing market demands.
The market change resulted in the supplying of more stone for asphalt and concrete purposes. As the operation began focusing on these materials, it began generating fines. In fact, the Woodstock quarry team noticed they were producing mountains of fines. Since the company culture had evolved to consider the impact of each operation and to innovate with regards to sustainability, the lightbulb started to illuminate in Woodstock--resulting fines could be processed into a proprietary, usable material. While the end goal seemed clear, there was still some adaptation and creativity that would be needed. That’s where the Polydeck team came in to help the plant figure out their new approach.
LafargeHolcim knew that the reprocessed fines would be highly marketable, and they were right. It became obvious that Polydeck’s spray nozzles, designed to handle heavy-duty washing, was the answer to adapting the decks to create a marketable product.
While a spray nozzle seems like a simple product, the devil is truly in the details. When the quarry started searching for a washing solution, they knew they needed the most efficient and durable product in the market. Ideally spray nozzles would have the capability to supply water at just the right pressure and geometry to produce a washing effect resulting in proper material separation and throughput. Polydeck’s spray nozzles, fitted to LafargeHolcim’s on site Simplicity 8x20 Triple Deck horizontal machine, did just that. When a spray nozzle functions properly, sized and distributed unwanted materials are freed and isolated as usable material.
The Woodstock quarry began testing a washing process to extract the fines using wire cloth, which is a common product in a washing operation. However, the maintenance and hands-on time of wire cloth soon proved highly inefficient for the operation. Time spent changing out wire cloth was time not spent producing sellable material.
After realizing wire cloth was an inefficient solution, LafargeHolcim turned to Polydeck once again and decided to design a plant for producing the proprietary material. Polydeck outfitted all three of LafargeHolcim’s decks with synthetic media as well as spray nozzles. The results were astounding. Adapting to a situation presenting an extremely narrow clearance challenge, Polydeck’s spray nozzles not only fit, but they also executed the job with certainty. Material that was previously resulting in waste was now being separated due to the efficient wash results produced by the combination of Polydeck spray nozzles and screen media. Polydeck spray nozzles feature a self-cleaning feature that eliminated significant man-hours and their ease of replacement and maintenance ensured the Woodstock quarry wouldn’t experience significant downtime should a part or nozzle need adjustment, replacement or cleaning.
LafargeHolcim learned first-hand how adapting their washing operation with Polydeck spray nozzles at their Woodstock operation increased their efficiency, throughput, and sustainability. Previous byproduct with very limited applications is transformed into a highly marketable product within tight specifications. Maintenance is reduced and simplified. The “money-deck,” as many call it, is free to produce material that results in a profit for the operation. When results and sustainability matter, Polydeck’s self-cleaning, heavy-duty, high-efficiency spray nozzles are second to none.
Vicdom Sand & Gravel knows full well that producing and washing aggregate is tough on equipment. The family-owned, third-generation company has been producing stone, sand, and gravel for more than 40 years in Uxbridge, Ontario, Canada, a 30-minute drive northeast of Toronto.
Vicdom’s management also knows that unnecessary downtime comes at a high cost. Until recently, the company had been encountering periodic wear issues with the 5’ x 7’ wire screen media on its two-deck, 5’ x 14’ Dillon wash screens. The screens were being used to produce +5/8" over the top deck, 9/16"-1/4" over the bottom deck, and 1/4" chip through the bottom deck. Although the screens had decent wear life and met production requirements when in operation, once they became damaged, they had to be completely replaced.
“We’d get one hole in the feed zone and have to change the whole screen, even though 75 percent of the screen is still in good shape,” says Victor Giordano, assistant manager at Vicdom, and grandson of late Vicdom co-founder Vic Giordano. “A $500 screen was now garbage.”
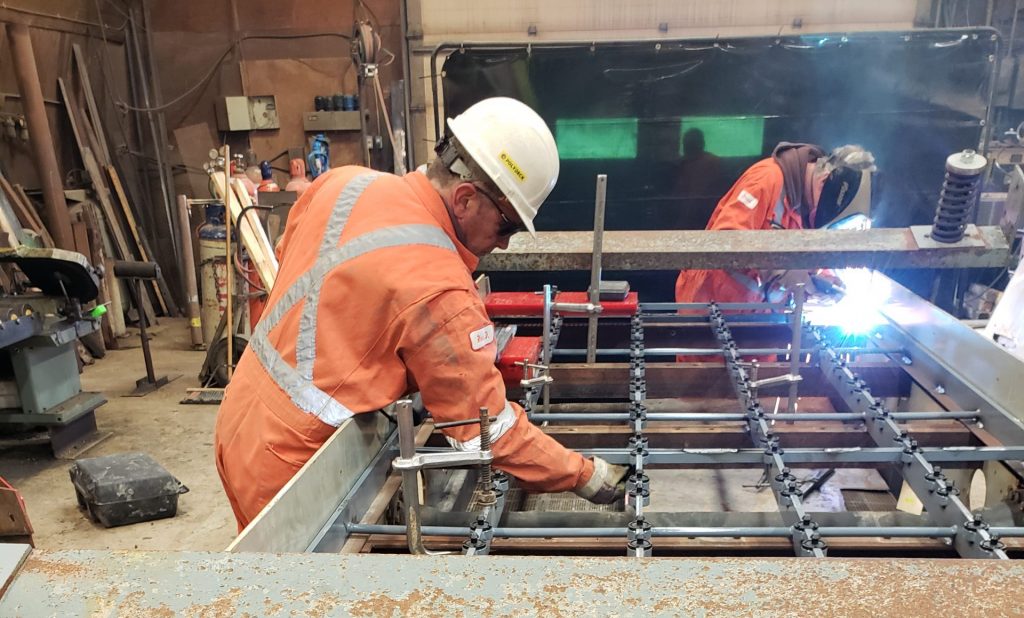
The larger cost stemming from the screen replacements was the downtime that came with switching out the 5’ x 7’ screen media, which Giordano says cost his operation between one and three hours of downtime each time they needed to be replaced. So, when Alex Caruana, Polydeck territory manager for Central and Atlantic Canada, explained that the company could save money and reduce downtime in its operation by retrofitting its wash screens with a modular snap-in system, Giordano wanted to learn more.
“Alex brought a diagram and did a good job in explaining what we had before with wire mesh and what we could have with Polydeck,” Giordano says. “The biggest knock on rubber and polyurethane is that it doesn’t have enough open area like wire mesh, but he showed that you didn’t lose any open area.”
Caruana showed Giordano he wouldn’t lose any open area by using a very simple, but effective method.
“What I typically do for a plant when they're considering one or more decks is very simple. I lockout, jump on the screen or take a picture, and just count the openings. I know how big the openings are, because I’ve measured them, and that also allows me to take into account any obstructions like bucker bars, side clamp rails, any diverters, any bolts and other things of this sort. That allows me to show the customer that with their current wire cloth, they have ‘X’ open area, whatever ‘X’ may be”, Caruana explains. “And then, I am able to show them that in their application, using our media, your open area would now be “X+,” and that's their new open area number.”
In many cases, this comparison is a big eye-opener for producers.
“Even with wire cloth, they may not have had all the open area they thought they did,” Caruana explains. “Just imagine a piece of mesh screen in front of you. It's unobstructed, and its cataloged open area, or book value, might be 65%. It looks very attractive. But when you actually put it in place, there are machine parts underneath it. So, you don't really have 65%, it might be 48%. Whereas, synthetic media is not the same. When synthetic media is giving an open area, that is the gross and net number. When installed, it still has that open area. If somebody tells you that you've got 48%, then that's the number in place. So, by me doing that comparison for people like Victor at Vicdom, they have that information available to them and they can make a more educated selection.”
Vicdom decided to change over one of its wash decks with a modular snap system using 1’ x 1’ Polydeck polyurethane panels with 1/2” square openings on the top deck and roughly 1/4” openings on the bottom deck. Giordano was impressed with the results.
“This year we changed two panels, total, on the conversion,” he says. “We would have normally changed five or six entire screens. Instead, we changed two panels that cost $90 Canadian each for $180 in a year. The efficiencies are good, capacity is good, and downtime is amazing,”
Vicdom has now outfitted all four decks on its two wash screens with Polydeck’s modular snap-in system using 1’ x 1’ polyurethane panels. The second wash screen has 5/8” openings on the top deck and roughly 1/4” openings on the bottom deck.
The reduction in downtime with screen media change-outs isn’t the only reason Vicdom enjoys working with Polydeck. Giordano says that Caruana’s level of professionalism has been a big selling point, always making himself available to assist with any issues that occur on-site.
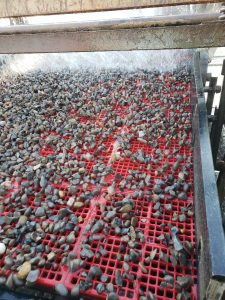
The company had a processing issue last year with the first conversion, so they called Caruana to discuss the issue.
“He asked, ‘Are you sure your eccentrics are running downhill?’” Giordano recalls.
So, Giordano checked with his maintenance crew and it turns out they had done some work previously that day and accidentally re-wired the motor backwards on the screen causing the eccentrics to run uphill.
“We fixed the wiring, popped the stone out and it was working again. With his knowledge we were able to fix that issue right away,” Giordano says, adding that he has a great appreciation for the technical knowledge Caruana brings with him to the job site. “I don’t see a sales guy. I see a guy with a lot of pit experience now in sales, and that helps.”
Thinking about a conversion?
Polydeck has a team of professionals and more than 40 years of experience to help you optimize your screening performance while minimizing downtime.
“You Lose Open Area When You Switch from Wire Cloth to Synthetic Media.”
Lots of facility operators still believe that if you switch from wire cloth to modular synthetic media screens, you will lose open area on your deck. As more producers try synthetic media, however, they enjoy greater throughput and uptime with maximum open area and extended wear life, proving this idea to be a myth.
Case in Point
Winter Brothers Material Company is a family-owned sand and gravel operation supplying the aggregate needs of the St. Louis area for 70 years. The two founding brothers, George “Pete” Winter and Robert A. Winter led river trips in the region during the 1930s, and after serving in World War II, they returned to the area and established the company in 1946.
Located on the Meramec River, a tributary of the Mississippi, Winter Brothers mines an alluvial deposit with unique particle shape, uniformity, and purity. “Our region is blessed with the availability of the consistent-grade gravel and the lignite-free sand deposited by nature in this river valley,” says Ryan Winter, a member of the Winter Brothers management team.
More than 70-percent of the company’s products are used in the ready-mix industry and perform well in a variety of Portland cement mixes. Products are also targeted to the roofing, masonry, asphalt, landscaping, septic systems, and extraction well industries.
The Challenge
At its Hagemann Plant, the facility’s main screening circuits produce six different sizes of coarse aggregates along with two sizes of sand products. “Since opening the plant, we had always used wire cloth on all the decks of each screening circuit,” says Winter, who admits that his management team had long resisted the use of synthetic media due to concerns over loss of open area and diminished production capacity.
Something they had not taken into account was the amount of open area they were losing due to material pegging and blinding. The wire cloth panels they used were advertised as having “maximum” open area, but as Winter tells it, “They would blind up within the first couple of weeks, and we would lose a significant percentage of throughput.”
Further issues arose with downtime due to screen maintenance during busy periods, when the plant beefs up production. Each of their decks utilized five 4-ft. by 8-ft. sheets of wire cloth, so Winter recalls that this was a critical issue for him.
“When one of those screens would blow out, we’d have to shut everything down, pull workers off of other jobs, bring in a crane, switch out the screens—all of that would take several hours out of the production day each time it happened.” Additionally, whenever a wire cloth screen suddenly blew a hole, oversize material would fall through and contaminate the product stockpiles.
So Winter, along with Plant Superintendent Steve Klahs—a 30-year industry veteran—began to take a hard look at synthetic media because they wanted to better understand the benefits and pitfalls of switching. Fortunately, they called Polydeck for advice.
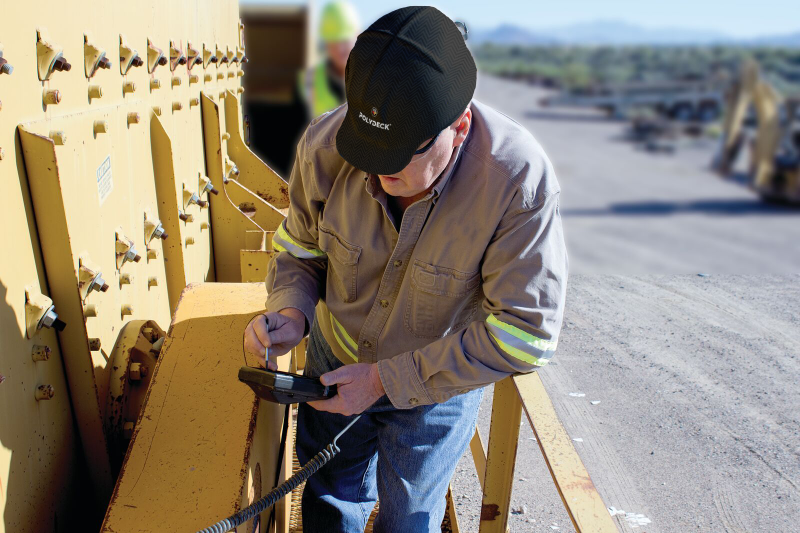
The Assessment
After talking with several synthetic media manufacturers, Winter says that he chose Polydeck due to our expertise and professionalism, and because of his strong relationship with local Polydeck dealer, CT Fike Co.
“Dan Fike was very proactive,” Winter explains, “He brought in key members of the Polydeck team to closely examine our processes so that they could specify the right panel types for our applications and gradations.”
Joe Teague, Vice President of Sales, but at the time served as Polydeck’s Regional Sales Manager, worked closely with the Winter Brothers management team. He demonstrated to them that their concern about loss of open area lies in how “open area” is typically defined and calculated.
“Published open area percentages result in miscalculations in the specification of the screen area and vibrating screen size required for a given application,” Teague explains. “Many wire cloth catalogs list percentages of open area which figure in all the openings in a section of screen. Upon installation, however, a portion of those openings are blocked by bucker bars, crown rubber, clamp rails, and center hold-downs. This means that the open area is significantly smaller, causing calculations to be off by up to 40-percent or more.”
In the case of many synthetic media brands, the open area is often calculated by simply ignoring the border. “The traditional panel has a large border or “dead” area around the perimeter that often is not taken into account,” says Teague, “So again, that means the open area percentage is overstated for these products.”
Teague showed Winter Brothers management that when engineering firms and end-users use these inaccurate open area calculations in their plant flow analysis software, the plant may be designed with undersized or oversized vibrating screens.
Teague’s advice to them was a revelation: Open area should be calculated by taking the total number of openings in the screen panel, and determining the percentage of actual open holes versus the complete surface of the panel itself. He suggested that Winter Brothers take a very basic approach to comparing the open area between two manufacturers by simply counting the number of holes on each screen panel.
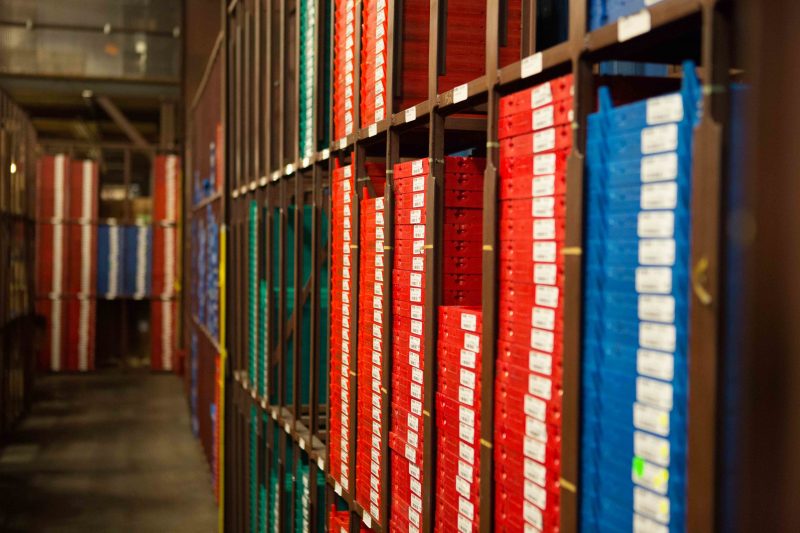
The Solution
The goal was to make sure that the circuit kept pace with the crushing side, so Polydeck’s approach began by correctly matching the media to the vibrating screen parameters, selecting from our library of more than 1,500 screen panel design options.
We reviewed all the product mixes to identify any potential gradation inconsistencies and plant bottlenecks, and make any upfront adjustments. After capturing the critical processing statistics, we ran “what-if” scenarios to optimize the media specifications to Winter Brothers’ applications, and determine how any changing variables within the screening operations would affect overall efficiency.
According to Winter, “Polydeck guaranteed us that their panel configurations would allow us meet the required specifications. If not, then they would make any necessary changeouts at their cost. That gave us a lot of confidence when switching so many decks to synthetic media.”
At the end of the assessment, Winter Brothers made the decision to install Polydeck’s modular polyurethane media panels.
The Results Speak for Themselves
Since installing the synthetic media, Winter Brothers has consistently met industry specifications.
“Since we switched out, we have only had to replace a few panels on the impact areas. We’re very happy with polyurethane’s increased wear life because, when we were using wire cloth on those decks, we were changing out a screen or two on a weekly basis,” says Klahs.
While Klahs once thought switching from wire screens would inhibit production, he now acknowledges that the use of synthetic media is saving their operation time and money. “We’re seeing an unbelievable increase in production—nearly double— particularly on the fine sand,” he says. “In addition, the open area on the polyurethane panels gives us excellent throughput. We are particularly impressed by the open area we get on our masonry sand processing.”
For Ryan Winter, the durability and resulting labor cost savings of using polyurethane panels is the chief selling point. “Our material is very hard,” he explains, “While typical limestone is a 3 to 4 on the MOHS scale of hardness, our sand and gravel is a 7 to 8. So, while throughput and open area are important, durability is critical.”
“We’re very pleased with the years of wear life we’re getting from these panels, and the maintenance crew can catch any wear issues before they become a downtime or contamination problem. If QC samplings are slightly off, the maintenance crew knows to check for wear. If they need to replace a panel, it only takes one individual a few minutes to pop out the worn screen and put a new one in.”
“Sometimes businesses stay with the same old methods because that’s the way they’ve always done things,” Winter admits. “That’s why we stayed with wire cloth for so long. But we eventually made the switch to Polydeck’s synthetic media and we’re glad we did.”
Myth…busted!
Polydeck’s new screen media solution maximizes throughput and product mix.
Aggregate Industries (AIUS) became one of the largest construction and building material companies in the US by stressing strategic sustainability, environmental stewardship, and long-term customer relationships. The company’s Morrison Quarry—a 3-million-ton-per-year granite operation located in Jefferson County, Colorado—perfectly illustrates their mission.
Jefferson County is one of three counties in the six-county Denver region within AIUS’ West Central Region that offers available sources of crushed stone. Because many of the potential aggregate resources in the Denver area are not accessible for extraction, the Morrison Quarry plays a key role in meeting the region’s demand for high-quality aggregate materials.
Morrison Plant Manager, Trulane Vanatta operates a “sold-out” plant, meaning everything processed on a given day is sold the next. For him, he bluntly explains, “Throughput is everything.”
As a result, the facility maintains a constant focus on boosting processing efficiency and production capacity. To eliminate bottlenecks at the screening circuits, the Morrison management team engaged with the engineering experts at Polydeck.
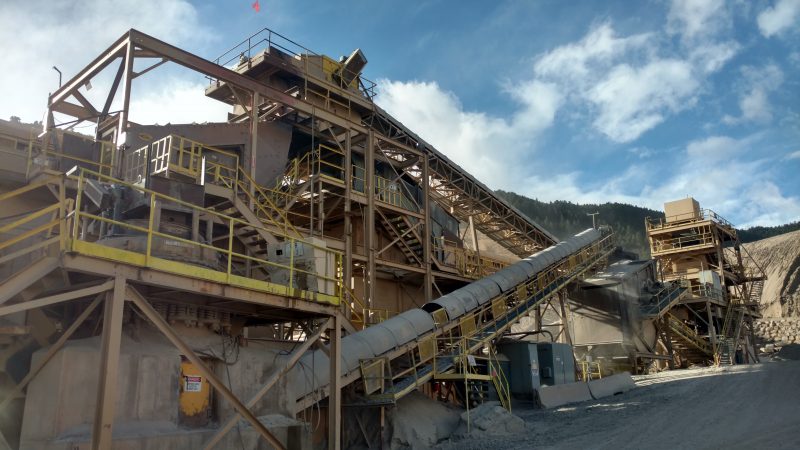
Reducing Recirculating Loads and Fines
Vanatta’s team identified a problem in the tertiary circuit of the nine-screen plant. Their belt samples indicated a high bed depth on the middle decks of the circuit’s three screens. Each of the 8-ft. by 20-ft. triple-deck screens are key to the production of Morrison’s #57/#67 (1-in.) material.
“That’s our money maker; and we have to maximize its production volume,” says Vanatta.
His team found a “troubling” 51% carryover, a bottleneck that was causing recirculating loads and producing excessive fines—a common production issue. “The first thing we thought of was replacing the middle decks on two of the tertiary screens with wire cloth to achieve more open area,” recalls Vanatta.
As it turns out, however, Polydeck’s Regional Manager, Sam Durnavich, was the assistant plant manager at the Morrison Quarry more than a decade ago, before joining the Polydeck organization. With his knowledge of the operation, Sam consulted with Morrison’s management and worked closely with Polydeck’s engineering team to create a media solution that would more effectively address their carryover challenge.
After a thorough analysis of Morrison’s operation, Polydeck’s production team designed and installed a brand-new product: DMAX™ screen panels, an ultra-high-open-area synthetic screen media system that significantly boosts throughput, and allows the quarry to increase the production of its highest-value products.
Polydeck’s new DMAX screen panels are intended for use where open area and throughput are the most important considerations. It’s a modular synthetic screen panel solution that matches or even exceeds the open area of wire cloth, while delivering greater wear life and easier installation. The DMAX screen panel system can also be formulated with either rubber or polyurethane depending upon the application.
Exceeding Production Goals
Since installing the first DMAX screen panels on two of the middle decks in October, 2015, the operation has met and frequently exceeds their production goals. They’ve also achieved far greater screening efficiency, according to Vanatta—nearly 54% open area on their middle decks, compared to the 42% open area delivered by their previous screen deck. That’s a dramatic 28.5% increase in open area. Morrison subsequently installed DMAX panels on a third middle deck in mid-2016.
“For us,” says Vanatta, “The increase in open area resulted in an 11% increase in the production of profitable 1-in. rock, and reduced fines by nearly 1%. The only downside to the open area is that the panels wear a little faster—but that’s essentially irrelevant as the profit from the tonnage increase pays for the screen media investment more than ten times over.”
The Morrison quarry also employs Polydeck’s Rubberdex® modular screen panels on the top and bottom decks of their 8-ft. by 20-ft. tertiary screens.
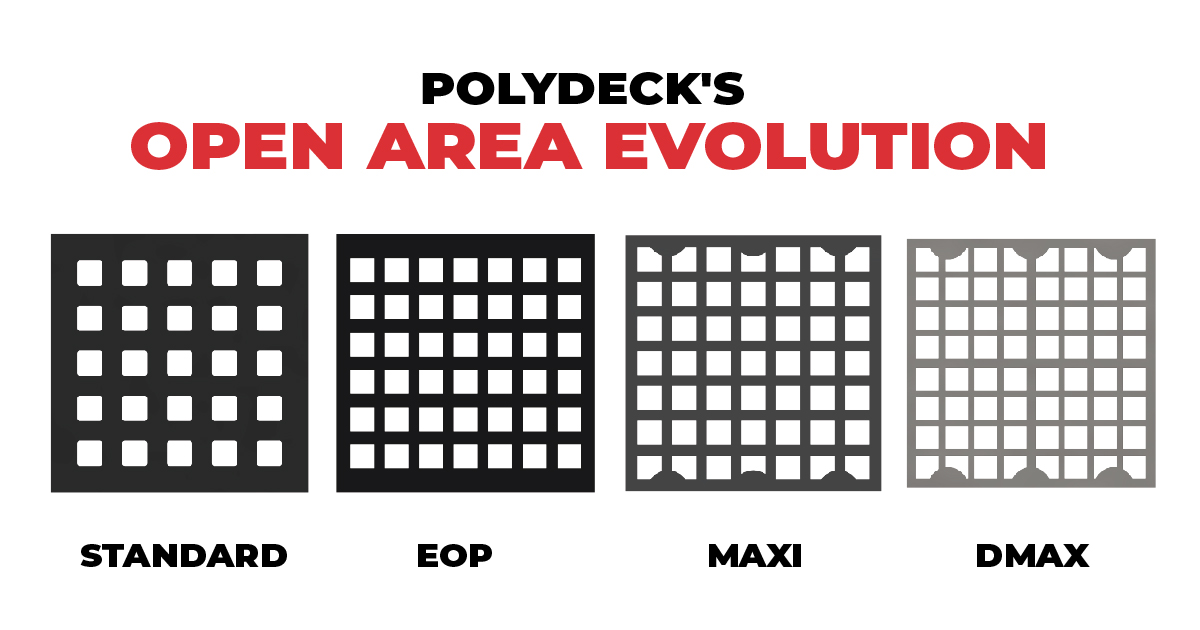
Engineering Expertise
Explains Polydeck’s Sam Durnavich, “We made the DMax panels with bridges that are half the width of those on our standard maxi panel, but much deeper. That’s important, because reducing the bridge width between apertures allows more openings in the screen panel surface, which translates to increased product pass-through.”
“Contributing to additional open area is the fact that DMax panels are designed to fit on existing Polydeck PipeTop II stringer systems,” continues Durnavich. “This framework system features unique half-inch-wide attachment rails instead of the mounting styles on conventional frame systems with up to 3 in. of dead space where fines build up. Furthermore, our in-house tooling capabilities allows us to provide many more options in these frame systems—from varying fastening options, material options, and stringer styles and types.”
“The increase in open area does come with a reduction in screen panel wear life,” Durnavich admits, “But when compared to standard-duty screen panels, the DMax panels are running at only 20–25% less wear life, which still exceeds that of wire cloth.”
“Our use of injection molding is a big factor in the ability to create extreme open-area synthetic panels,” adds Durnavich. “Injection molding ensures that every screen panel has accurate opening sizes and shapes, and is thoroughly cured throughout.”
“Our actual field results in several applications have demonstrated production increases all the way up to 50%, and screening efficiency increases of more than 25%,” says Durnavich with a smile.
Polydeck continues to expand the range of available apertures in the DMax series, with square openings from 12.5mm up to 32mm, as well as slotted openings from 3x20mm up to 25x74mm.
It’s often said: If there’s a bottleneck at a plant, it’s probably at the screening circuit. Throughput is everything at the Morrison Quarry, so continually increasing screening efficiency is essential to their ongoing profitability and product quality. Working together, the Morrison Quarry and Polydeck solved an immediate problem and created a long-term solution.
KWIKDECK is a simple and cost-effective way to try modular media.
Screen media is a critical component for the aggregate, energy and industrial, and mining industries. For decades, wire cloth has been the industries’ go-to media, but they are cumbersome to install and not as versatile as modular media. If you use wire cloth, you’re probably accustomed to changing them out every few weeks, a time-consuming and sometimes dangerous task.
What if you only had to replace your screen media twice a year?
Polydeck’s KWIKDECK system offers a better solution: A frame conversion that lets you try synthetic screen media virtually risk-free, with minimal set-up costs and easy installation.
KWIKDECK helps you cut operational costs, reduces downtime while improving safety, and keeps your equipment running at peak performance.
What makes KWIKDECK such an ideal solution?
- It’s Simple to Install – KWIKDECK takes about 45 minutes to change out a 4-ft. by 6-ft. section. It reuses the existing side clamp rails, and doesn’t require altering the existing desk’s frame.
- It’s Adaptable – KWIKDECK works with crowned decks, and can be modified to fit the dimensions and configurations of most vibrating machines.
- It’s Cost-Effective — KWIKDECK enables you to use synthetic screen media, which lasts at least ten times longer than wire screens,[1] and requires less maintenance and fewer changeouts than wire.
KWIKDECK is also perfect for portable screening operations that need to alternate between wire cloth and synthetic media. Operators can easily switch between different media types to maximize production requirements.
KWIKDECK provides an opportunity for traditional wire cloth users to try synthetic media with minimal cost or risk. Install it at the feed end of your vibrating screen, and see for yourself what a difference it makes.
Learn more about KWIKDECK, another innovative product from your partners at Polydeck—and just one more example of how we’re together strong.
[1] http://www.pitandquarry.com/pq-university-lesson-8-screening/