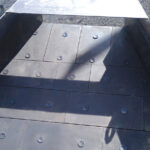
Beyond the Screen: Wear Protection with PROTEX
June 17, 2021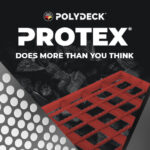
Protect for Efficiency. Polydeck PROTEX Does More Than You may Think
July 15, 2021Mining and aggregate operations that utilize Polydeck synthetic media experience many benefits, including a decrease in downtime with a modular system, increased media wear life, and the ability to add surface features. Polydeck surface features can either be integrated into the panel design or added onto the modular system as an auxiliary feature. This article will review molded surface features, which include dams, restricted flow bars, skid bars, and deflectors. Each can play a key role to increase efficiency when used correctly.
Dams can be molded on both POLYDEX® and RUBBERDEX® media and serve three primary roles: they slow the material flow, help build bed depth, and aid in material stratification. Injection-molded dams come in 1”, 2”, and 3” options. Dams are commonplace in many operations and may be useful to slow material on slurry-fed or incline decks, retain material under spray bars to maximize fines removal and passing of near-size material, or build bed depth in lightly loaded applications. They also stratify the material by agitating and redistributing the fines to the bottom of the material bed.
Pro Tip: For Flexi RUBBERDEX® panels with dams, Polydeck recommends installing dams oriented to the feed end for improved wear life.
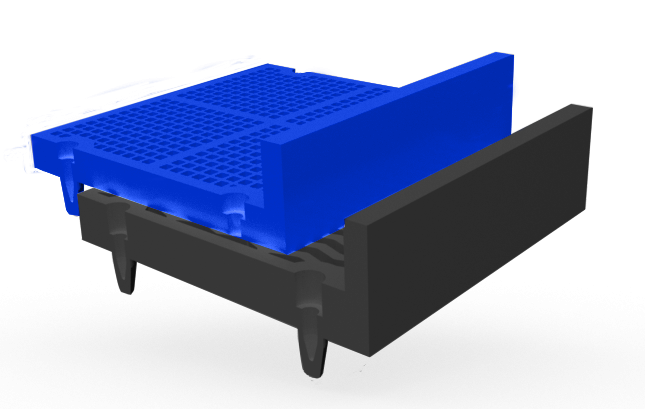
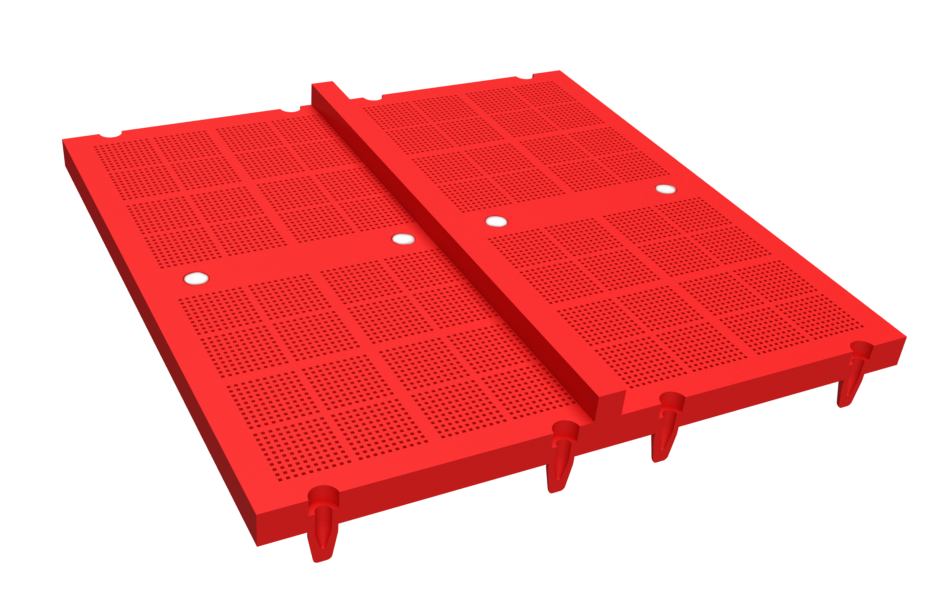
Restricted Flow Bars, or Restricted Flow Dams, consist of a multitude of low-profile dams along the surface of the panel; these are oriented across the flow of material and are available with many POLYDEX® panel designs. Similar to traditional dams, these may aid in slowing material across a deck, but they are especially effective in stratifying material.
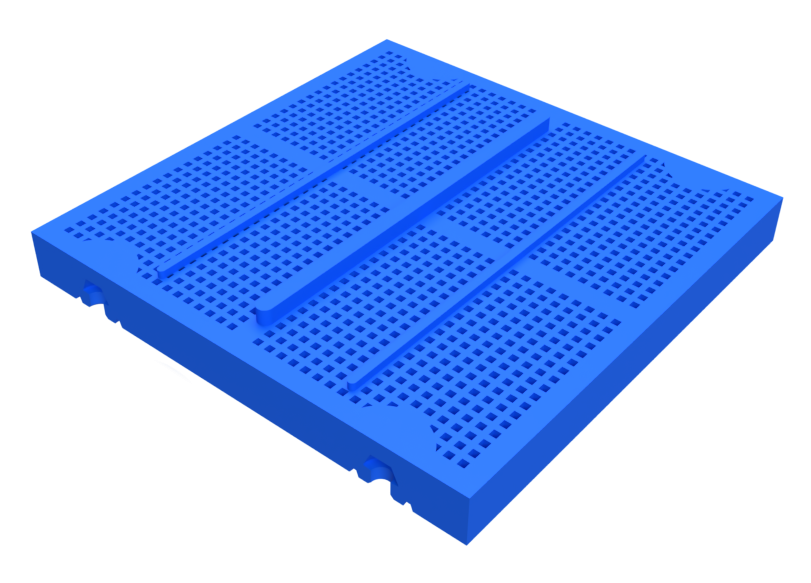
Skid Bars have similar structural form to the Restricted Flow Bars, but the orientation is with the flow of material. The main purpose for skid bar use is to increase wear life in heavily loaded or highly abrasive applications. These may be added to increase panel rigidity, as well, and are available on both POLYDEX® and RUBBERDEX® media.
Pro Tip: Use Skid Bars as stratification aids. Apertures prone to blockage by oversized material can be cleared by elevating the rocks via skid bars; this allows smaller material to pass through the panel.
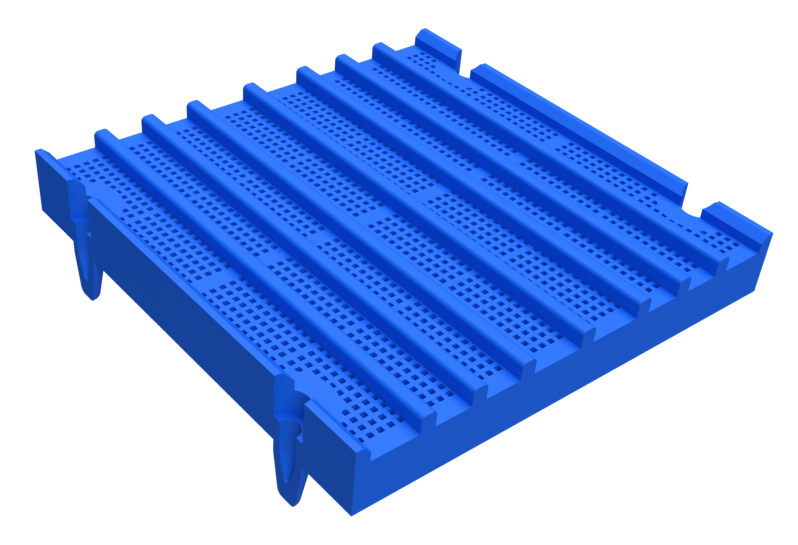
Deflectors are small protrusions intended to prevent material from channeling down the panel margins. As the name implies, these deflect the material from the margins to reroute the material over the apertured panel surface. These are highly effective on Polydeck Standard, Extended Open Area (EOP), and Polyrail panels, which carry wider lateral margins to protect channel and tube stringers.
Pro Tip: For many Standard and EOP applications, an alternative to deflector use is converting the deck support to Polydeck PIPETOP STRINGERS; this change significantly reduces the margin and increases open area with Polydeck MAXI and DMAX media.
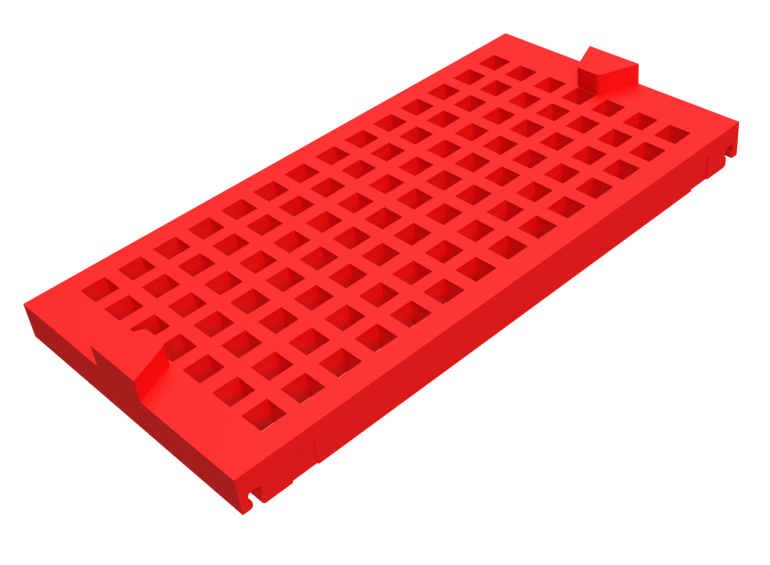
In conclusion, molded surface features are simple additions that can make notable impacts on the efficiency of many screening operations. The molded surface features smoothly integrate into most Polydeck modular media layouts and are an easy means to mitigate common screening challenges with the change of a panel.
Contact Polydeck for more information or a personalized recommendation on molded surface features and other process improvements.
Written by Jamie Mills, Product Development Application Engineer for Polydeck.