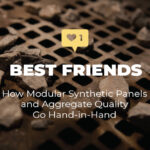
How Modular Synthetic Panels and Aggregate Quality Go Hand-In-Hand
January 12, 2021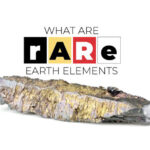
What are Rare Earth Elements?
January 12, 2021Part 2 covers extending the life of your equipment and maintaining operations by being proactive with maintenance and quality control.
In Part 1 of this two-part series, we reviewed some of the many decisions that must be made before selecting the right screening solution for your operation. Asking the right questions upfront can really pay off over the life of your equipment, once you’ve made the investment.
Part 2 below looks at how to extend the life of your equipment and maintain smooth operations over the long-haul by establishing a system of proactive maintenance and quality control. With such a system in place, you achieve greater visibility over your operational performance and can identify emerging issues before they develop into major problems.
Proactive Maintenance
A schedule of regular maintenance is the best way to ensure that your screening system operates reliably, with a longer wear life, consistent specification accuracy, minimal downtime, and maximum cost efficiency.
Whether you use wire cloth or a synthetic option, periodic visual inspections of your system are necessary to detect any extreme or unusual wear.
- Check synthetic screen decks for wear patterns possibly caused by a change in feed rate, uneven material distribution, or high-pressure water spray. Replace worn screens immediately to prevent out-of-spec material or damage to the fastening system or steel support structure.
- Make sure side-tensioned media screens are tensioned correctly upon installation, and be sure to support side-tensioned synthetic screen decks with high-quality bucker bar rubber. Check them on a regular basis, looking for loose clamp bars or blocked apertures that are plugged with material or blinded over, and re-tension the screens where needed.
- Examine side wear liners as they typically last longer than the actual screen surface, looking for wear and for loose bolts or clamping hardware. If all liners are not securely tightened, the screen panels can move, and potentially damage the side wear liners, the screen panels, or the modular support structure itself. Loose side wear liners can also allow screen panels to disengage, causing material to go out of spec.
When replacing modular synthetic media, ensure a secure attachment to the frame by cleaning sand or fines from the frame surfaces and the fastening cavities.
Regularly evaluate your screen equipment for unusual variations in operating parameters, such as acceleration, displacement, deflections, and critical frequency, all of which can hinder screen performance and even seriously damage the support structure.
It’s also important to work closely with your screen media manufacturer to perform a screen analysis on the machine itself, in order to isolate the possible cause of poor screening performance. Don’t forget that Polydeck offers screen performance evaluations and we’re ready to help.
Quality Control
Frequent quality control sampling to detect spec changes—either sudden or gradual—is an effective method to monitor the wear life and condition of your screen media.
With modular synthetic panels, the maintenance crew should always be looking for any wear before it becomes a contamination problem. If the quality control team detects gradation changes, however, they can also alert the crew to start gauging the screens and check for any unseen wear issues.
Replace affected modular synthetic media when a product gradation begins trending to the high or low end of the spec range. It takes just a few minutes to change out any worn screen panels and resume operation.

No matter what screen media you deploy, it will eventually succumb to the wear-and-tear of everyday use, not to mention the common operational hazards of the industry.
Selecting the right screen media for the job, and then performing proactive maintenance and quality control tasks, are the best strategies for maintaining optimal performance. By repairing or replacing worn components before they fail, operations can ensure the day-to-day reliability of valuable processing equipment while meeting or exceeding production goals at the same time.
To help you get the most out of your synthetic media, we’ve created a downloadable checklist for you. Click the link below to get your copy.