Producers often turn to what has always worked and what they are accustomed to when it comes to selecting their screen media. While wire cloth has its advantages, wire has met its match in Polydeck’s newest offering. Meet DMax, the latest in high performance, extreme open area synthetic modular screening.
At Polydeck, we’re known for relentlessly pursuing solutions to the challenges our customers face. When your operation depends upon the performance of your screen media, nothing less than the best solution is acceptable. DMax, Polydeck’s latest evolution in modular synthetic screen media provides so much throughput advantage, its open area rivals that of wire cloth while providing the durability and benefits often associated with modular synthetic screen media panels.
DMax is the result of Polydeck’s advanced material science technology that balances durability and high open area in screen media construction. This balance provides a better return on investment and a significant increase in throughput where DMax panels are used. Plant Manager Trulane Vanatta recalls the efficiency gained by using DMax panels at Morrison Quarry, “The increase in open area resulted in an 11% increase in the production of profitable 1-in. rock, and reduced fines by nearly 1%.” As any producer knows, even small reductions in fines paired with production increases is incredibly important to an operation’s profitability.
When producers initially began using synthetic screen media, it was in response to the durability the product offered them. DMax achieves the durability producers expect, along with a significant increase in available open area. DMax provides the perfect balance between wear life for uptime, and the health and safety benefits associated with reduced noise and fewer whole deck changeouts. Like all of Polydeck's modular synthetic media, Dmax can be changed out in small sections as screens wear, preventing dangerous and costly shutdowns for larger media changeouts, while preserving the benefits synthetics are known for.
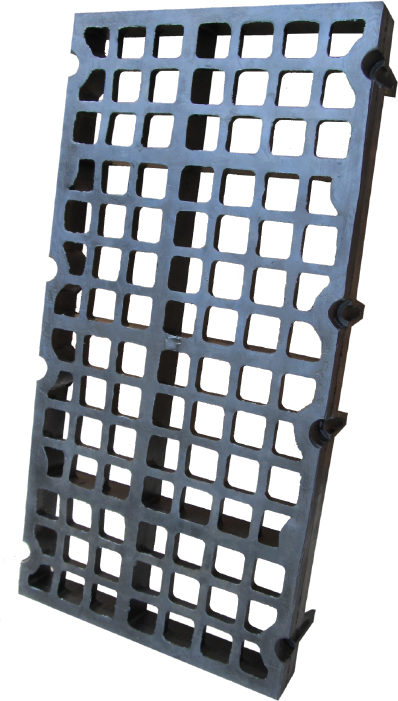
DMax panels are fully customizable, allowing Polydeck’s team of experts to create a solution that meets the unique needs of each operation. Common opening ranges can increase open area by 25-30% against standard synthetics, frequently exceeding wire's actual available open area, which is the open area actually available once bucker bars and other dead spots are accounted for. As every producer knows, open area is directly related to efficiency, thus more open area means a more efficient operation.
A Producer using cone crushers in a closed circuit could benefit significantly from using DMax. The extra open area on the screen preceding the cone crusher allows the product to reach the pile more quickly, instead of the cones. The result is extra capacity for the cone, less fines generated overall, and good salable product to pile sooner and in higher overall splits within the plant. The extra open area provided by DMax means less dust and fines and more clear stone production. This also helps decrease cone crusher wear and reduces overall power consumption since the system is being evacuated more quickly. Reduced power consumption translates to lower operational costs both in energy costs and wear on equipment.
Polydeck’s modular technology allows for easy and safe installation of DMax with other panels and use in zones where efficiency is key. DMax is ideal for use in conjunction with heavier duty panels in feed zones in order to maximize useful available open area.
DMax offers a significant weight reduction benefit over other synthetic screen media options, which reduces component wear on the screen and increases the effect of the vibrating mechanism’s stroke on particle separation. At the end of the day, it all translates to higher production levels with reduced costs.
While there are many applications where DMax can be used, producers win with DMax where there are overall blinding issues or overloaded decks leading to inefficient screening. DMax eliminates blinding and allows for more throughput. With DMax, the right size material goes through the screens, eliminating downstream bottlenecks and increasing tonnage through the plant. When durability, true open area, and reduced downtime come together, efficiency is the ultimate result. Consider DMax, the synthetic screen media that will have you rethinking your wire cloth.
Our new line of ceramic liners and panels is the latest example of how Polydeck brings groundbreaking solutions to the surface.
When you partner with Polydeck, you gain access to industry-leading products and services, backed up by unmatched support and a half-century of expertise. Our new line of ceramic liners is the latest example of how Polydeck brings groundbreaking solutions to the surface.
We didn’t make our name by simply conforming to industry standards; we made it by creating brand-new ones. INNOVATION is what Polydeck is known for, and it shows in the level of attention we give our ceramic liners and panels.
Ceramics may have been around for a while, but we combined our knowledge of materials and panel construction to create new, more valuable ceramic solutions that solve your costly problems. Polydeck’s ceramic liners are a versatile, bolt-in solution engineered for maximum performance in aggressive wear environments.
Our modular, lightweight ceramic liners are specially-designed for higher abrasion resistance and longer wear-life, as well as reduced noise levels and fewer change-outs—all of which can dramatically lower your maintenance costs and improve safety levels.

We synthesized our proprietary Armadex rubber compounds to work with ceramics, in order to provide the flexibility and high-wear tolerances that address any need. Our ceramic liners also feature unique panel designs that help eliminate blinding, meaning you put more saleable product on the ground.
Our experts can even custom-mold Armadex ceramic liners with different durometers to match your specific application, working with you to select the right combination of materials and apply the perfect solution.

We offer outstanding lead-times and incredible technical support for our ceramic liners and panels. Whether you need to cushion a loading issue, decrease wear at a transfer point, or eliminate blinding and high wear in your chutes, our highly-trained and experienced field support team can improve your current situation with a better ceramic solution.
In addition to our unmatched external support, Polydeck’s internal engineers are available by phone to discuss your needs and help you coordinate with our outside team. Our Applications Engineers review every order we receive and discuss the details with our field representatives to ensure that you receive the best service and solutions possible.

Our support services extend to the supply chain, as well. Polydeck can keep you fully-stocked by putting the ceramic liners or panels you need into regular inventory at one of our regional distribution centers, strategically located across the country. If you’re ever caught in rush and need help immediately, however, there’s no one in the industry who can respond as quickly as Polydeck’s manufacturing team.
When you place your order, we commit to the delivery schedule you require. For most suppliers, standard lead-time is typically 3–4 weeks to push out a rush order. Polydeck has accomplished rush orders overnight, ready for next day shipment. Even if you inadvertently run out of onsite stock or someone forgets to place an order, Polydeck’s manufacturing ability is there to back you up.
Finally, as with all our products, our ceramic liners and panels are backed by Polydeck’s industry-leading Performance Guarantee: If you’re not satisfied with the results, we will do everything possible to make it right, including replacing any unsatisfactory panels on a pro-rated basis.
It’s simple—We work hard to support all your needs, because supplying value through innovation and total service is what you expect from Polydeck.
Written by Frank Harris, Strategic Sales and New Product Development for Polydeck.
We’ve put together a list of must-have safety checks for you and your employees when it comes to your screen media systems – read more today.
Safety of employees is top-of-mind for many plant managers and executives out there, and rightly so. In our industry, there is a potential for many workplace injuries, with heavy machinery and lots of moving parts. With this in mind, we’ve put together a list of must-have safety checks for you and your employees when it comes to your screen media systems. Read on to learn how more about workplace safety, as well as how to maximize the use of your screen media systems (safely, that is!).
1) Lock, Tag & TRY
If you’re performing any work on your screens, lock them out, along with their feed and discharge conveyors. It’s key to try the start button after locking out, to make sure you’ve got the right units. If you’re not sure where to lock out, there’s usually a plant diagram in the electrical room, or someone happy to show you how well they know the plant to help!
2) Keep it Quiet
Forget about wire or punch plate on your screens, this stuff operates at around 105dB! Switching to synthetic will reduce this to around 95dB. You might be thinking that’s just a reduction of 10dB, but decibels are a logarithmic scale, meaning each increase of +1db is a x10 multiplier. In brief, the difference between 105dB and 95dB is about half of what the human ear perceives. This will contribute to screen media safety with less risk of hearing loss and much better perception/awareness of what else is going on around the plant.
3) Lighten Up
Changing punch plate or wire cloth can be quite the task. It’s large, heavy and unruly to handle. If you haven’t done it before, think of moving a 4’ x 8’ section of sharp, heavy, floppy metal inches from the edge of a machine while balancing on ½” wide rails with openings below (eeek!). Unless you’re a heavy-lifting ballerina, it’s truly no fun. Consider modular media for a minute, which comes in 1x1’ and 1x2’ sections, for example. One person can change a localized area, away from fall hazards, without creating large open spaces to fall through beneath.
4) Make it Last
It’s no secret, changing screens isn’t fun, so why do it any more frequently than necessary? One reason is for screen media safety! Make sure you’re using as long-lasting screen media as possible as your throughput will allow. Place heavy duty media in your impact zones, and lighter formats in your flow path. This will even out the longest lasting options along your media screen’s surface and drastically reduce your workload, and exposure to any maintenance hazards. No matter what screen media you use, there are options for heavy duty to light duty formats to balance wear with open area / throughput. That said, synthetic media lasts 12-20x longer than wire will.
5) Keep Cool
Fire hazards are very real around screens. Gum rubber chute liners and cast-in-place media/liners (like spray bar boots and most magnetic liners) are highly susceptible to starting a fire. While all synthetics will burn when continuously exposed to flames, there are many options out there that reduce the risk of a fire and ensure screen media safety. Injection molded media will frequently allow a piece of hot steel to simply drop through for example, whereas cast-in-place media or gum rubber liners tend to spread fire rapidly. Some aggregate producers have entirely banned cast-in-place synthetics and gum rubber liners! If you’re doing hot work around synthetics, make sure your fire watch includes someone who can see below the work, and not just the workers above who are likely focused on their immediate point of work.
6) Dust It Off
Keeping the dust down is important to the safety of site staff and neighbors. Dust can easily blind up your screens. There’s a multitude of wire and synthetic choices out there to handle wet, sticky material on your screens. Using the right screen media to deal with blinding from dust suppression ensures you’re not sending staff into screens for nasty clean up jobs as a result of trying to improve their screen media safety in the first place!
7) Make It Simple
Make your screens simple and easy to deal with. This will ensure that when it is time to work on them, it’s likely to get done quicker and more accurately. Simplifying your screens with modular media also allows you to focus on higher priority tasks like plant automation, optimization, and better mine planning. Stop changing cumbersome screens and move on to something more fun entirely!
Go ahead, put these screen media safety tips into practice! In the meantime, if you want to learn more about Polydeck screens or any of our other products, contact us today!
Written by Alex Caruana, Aggregate Territory Manager for Polydeck.
Read about why Polydeck uses injection molding to manufacture our screen media.
Screen media plays a crucial role in efficiently segregating or separating minerals. Without a high-performance, durable screen material, frequent screen changes and unplanned downtime are inevitable. High-quality screen media maximizes run time, operating efficiency and profits while minimizing downtime and maintenance costs.
The Beginnings of Injection Molding in Screen Media Manufacturing
Mining operations sacrifice thousands of dollars in lost revenues due to screen media maintenance issues and inefficient screening. One way to ensure the quality of the screen media is to evaluate the process by which it is made. Although used in manufacturing settings for years, it wasn’t until the late 1960’s that injection molding was first incorporated in the production of screen media. That’s when Manfred Freissle, the Father of Polydeck, engineered a modular synthetic screen media concept and chose injection molding as his manufacturing process of choice.
Advantages of Injection Molding
Modular screen media needs to be consistent in its construction throughout the panel in order to withstand the harsh forces generated in mining operations. At Polydeck, injection molding was chosen as the highest quality option. Other processes like casting produce inconsistent results and rely heavily on an operator monitoring the process. There are no means to effectively inspect the material for proper curing that is non-destructive once the casting process begins. For example, on rubber screen panels, under-vulcanization in the center or over-vulcanization of the outer skin reduces the performance of compression molded panels and therefore compromises screening efficiency. These irregularities led Peter Freissle, Manfred's son, to choose injection molding instead for its consistency, durability, and overall quality versus competitive processes.
Since the creation of the first prototype, Polydeck has continually been committed to research and development of products and methods that lower the overall cost per processed ton for its customers. This uncompromising approach has resulted in screen panels that produce consistent high-quality results every time.
Consistency is Key (and the Proof is in the Product)
Polydeck’s injection molding process involves heating the raw material of proprietary polyurethane or rubber blends into a liquid state and injecting it under extreme pressure into a cavity containing a wide range of mold geometries required to make each specific product. These components and geometries allow a myriad of combinations relating to the aperture size and shape, fastening type, and surface features, while producing panels that minimize any trapped air and/or voids inside the panel which compromise integrity. The entire process is carefully calibrated and computer controlled to monitor key process indicators from panel to panel, minimizing operator errors, and ensuring consistency.
As a privately-owned company focused solely on effective screen media solutions, Polydeck has the flexibility and a range of more than 1,500 screen panel design options to suit virtually any screening need. The injection molding process can produce panels in minutes, not hours, enabling the company to feature the shortest lead time in the industry on non-stock screen panels. By using superior materials during manufacturing, Polydeck is able to ensure consistency in construction and repeatability from panel to panel. This means more product can be screened, leading to higher payouts and an overall more efficient screening process.
Ultimately, when choosing screen media, producers should consider the quality and value of the media, and base their decision on the overall costs saved over the life of the screen panel. Compared to media options sold at a lower cost, Polydeck screen media offers a range of time and cost-saving benefits that no one else can offer.
To learn more about Polydeck’s injection molding processes and how you can save money and screen materials more efficiently, contact a Polydeck screen media expert today!
There’s an old saying that goes: “If it isn’t grown, it has to be mined.” That’s not entirely true, but it makes you wonder what items don’t fit into either of those categories. Keep reading to learn more.
Mining has been and always will be critical to our civilization. This is especially true in our technology-driven age, in which the mining of “Rare Earth Elements” has taken on special significance. You’ve likely read news stories about Rare Earth Elements in recent years; so, what are they and why are they so important?
Rare Earth Elements are instrumental to our modern world.
When people think of mining they typically think of coal, copper, or gold mining, but all sorts of raw materials are mined from the earth. Because the mining industry is so widespread, it is a hotly-debated topic among politicians, environmentalists, and communities around the world.
More recently, the attention focused on the mining of Rare Earth Elements has grown rapidly in global scale and impact. To start, there are 17 Rare Earth Minerals grouped together on the Periodic Table of Elements: cerium (Ce), dysprosium (Dy), erbium (Er), europium (Eu), gadolinium (Gd), holmium (Ho), lanthanum (La), lutetium (Lu), neodymium (Nd), praseodymium (Pr), promethium (Pm), samarium (Sm), scandium (Sc), terbium (Tb), thulium (Tm), ytterbium (Yb), and yttrium (Y). Despite their mysterious name, however, not all of them are truly “rare.”
What makes them so important, or as we call them, “rare,” is these materials are found in one form or another in virtually every technological device on the planet. Without them, the modern world as we know it could not exist.

Rare Earth Elements help us “Go Green.”
The big tech push right now is in “going green” through electric vehicles and sustainable energy sources. One Rare Earth Metal in particular—neodymium—is used to produce strong magnets for electric motors and turbine generators. Many rechargeable batteries are also made with Rare Earth Metals, such as lanthanum, cerium, promethium, and neodymium.
Rare Earth Elements are the future.
From cell phones and aircraft engines, to MRI machines that save lives every day, Rare Earth Elements are integral components to the evolution of technology and the future of innovation. To date, China is the largest producer of Rare Earth Elements, but that is beginning to change. With the price of metals from China increasing, and a growing recognition among world powers that Rare Earth Elements are strategic resources, many other nations are ramping up domestic production capacity, both to meet the skyrocketing demand and to ensure a stable supply.
Here in the US, Polydeck is currently helping a new mine in Nevada produce Rare Earth Metals. Australia, Brazil, and India have all recently ramped up production as well.
The future is bright for Rare Earth Elements and mining them is definitely a growth industry for the foreseeable future so long as we keep using cell phones, driving electric cars, and using the latest devices.
Written by Tod Eberle, Director of Aggregates for Polydeck.
Control the quality of aggregate being produced by using modular synthetic media.
Most operators already know there are huge benefits to synthetic media in terms of wear life and cycle cost, as well as better maintenance efficiency due to the ease and speed of changing out worn modular panels. They’re probably also aware that the panels are easier and safer for crews to work with on a deck.
What can often escape the conversation about modular synthetic media, however, is just how tightly the operator can control the quality of aggregate being produced—and what that reliable quality means to not only the aggregate’s producer, but also the end-users.
Consistency is king!
Talk to any end-user of aggregates—such as a concrete or asphalt plant—and its virtually certain that a key factor in their success isn’t simply spec product; it’s also consistency of product.
Sure, end-users can adapt to different gradations of aggregate by adjusting their blends, but this changes their product, too. If the aggregate gradation is consistent, then so is the product being made with it. This, in turn, provides reliable and predictable performance materials for whatever the application may be.So, why do synthetic modular panels ultimately produce a more predictable pavement, bridge, or foundation?
Roller coaster or train ride?
Take wire cloth, for example. Its cut size can change rapidly during production because when wire cloth wears, it tends to break sections open and contaminate the product with oversize aggregate. Along the way to failure, wire cloth’s shallow profile also means that it’s quite common for oversize pieces to filter into the pile through worn openings, creating inconsistency issues.
Because wire cloth creates such rapid trend changes in quality control, there remains a high potential for oversize failures unless aggregate producers are extremely vigilant and change large sections of the screen deck before it fails.
The quality trends produced by modular panels are smoother and more reliable, without the same dramatic shifts up and down. This is due to the vastly improved wear rates of synthetic panel modules, and their tendency to slowly coarsen aggregate rather than “blowing open” and contaminating the product like wire cloth can do.
Such consistent reliability allows modular panel users to effectively monitor their screen media’s condition through quality control reports, instead of just relying on visual or maintenance inspection.

Custom blends
A modular panel setup also allows an operator to produce custom products with drastically more control.
For example:
An aggregate plant deploys an 8-ft. by 20-ft. wire wash screen, comprised of five 4-ft. long sections. If a customer comes to them needing a modified product, then that plant can only make changes in increments of 4-ft. runs—or just 20% of the screen’s area—at a time. Ouch!
Often, this can have too much or too little of an effect. Modular panels allow these changes to be made to the exact degree necessary, in the appropriate portion of the screen, at increments of 0.625 percent!
Ultimately, with synthetic modular panels, an operator can stop worrying about quality control and start using it to their advantage, turning customer complaints and job site fines into customer satisfaction.
Written by Alex Caruana, Aggregate Territory Manager for Polydeck.
Addressing the top 5 most frequently asked questions about screening.
1. I think there’s something wrong with my screen, but I don’t know if it’s worth calling in a professional to diagnose it – what should I do?
There are some visual or field tests you can run to see if it’s worth investigating a screen further. Two easy tests are:
- Travel rate. Paint 2x oversize stones, drop them onto the top deck (loaded and running) simultaneously and observe. If they travel in parallel and come off the screen together, that is a good thing. Timing the travel is valuable to let you know if your screen is running too fast or slow, too.
- Stroke/Displacement. Take a magnetic stroke card measurement of your machine at the vibrator as well as in the corners – on both sides. You’re looking for consistency between sides primarily. Deviations of more than 5% indicate a problem you should investigate further.
You can also list the symptoms of your suspected issue and give us a call!

2. How do I make my Quality Control easier to manage from a Production point of view?
Firstly, communicate! Establish clear and open understanding with your QC staff, give them a plant tour, take a tour of their world too… it’s amazing what happens when you learn about each other’s processes. Secondly, make your screening circuit as stable as possible. Eliminate stop-gap or temporary solutions like patches and silicone on screen media.
3. How do I increase my production rate?
Diligence. Observe and even out feed points, use the right combination of screen media to only apply heavy-duty media in high wear zones and high open area media on other zones. Spend some time looking at bed depth on each deck and whether the stroke is appropriate for each application. Most of the time, some patience and trying one variable at a time to see the effect is highly rewarding.
4. My media is pegging, what do I do?
First, make sure your screen has enough stroke to clear the pegging particles. Remember, you need to manually clear the pegged particles before truly knowing if a change in stroke will prevent this. If this doesn’t work, there are highly successful self-cleaning types of media in all forms – wire, rubber, and polyurethane.
5. How do I set up my spray nozzles?
Set up spray nozzles pointing at 45 degrees against the flow of material. The resulting spray should form a continuous water curtain across the screen, such that material cannot sneak through any weak spots. Working with a screen expert can help determine how many spray bars, nozzles per bar, and spacing from the deck are required, along with volume and pressure balance. Once you see a proper nozzle setup, it's easy to apply throughout your screening circuit.

**These Frequently Asked Questions were collected from a presentation by Aggregate Territory Manager, Alex Caruana. If you'd like a more in-depth online training session for your operation, feel free to contact us.
Additionally, we have provided several resources below for your convenience.
Necessity is the mother of invention. In fact, that’s how Polydeck was born, when Manfred Freissle saw the necessity for something that functions better than wire cloth.
Fast forward to today, when Polydeck has well over 1,000 dies, numerous materials and surface features – and still, when there is a need to perform yet a new and different function, Polydeck will invent all over again. Keep reading to learn all about how our panels go from ideation to production!
1. The Challenge
The challenge shows itself. Quite simply, this is the ‘necessity’ part where an Aggregate, Energy and Industrial or Mining operation needs to do something differently. When Polydeck confirms this challenge requires a new panel as the solution, we get inventing!
2. Information is Gathered
Polydeck collects all sorts of information: What type of material is being processed? How is the material crushed, what are its challenging characteristics? Has a different panel been tried? All this information helps us to create the best possible solution for our screening partners.

3. Design. Design. Design.
Given the information collected in partnership with our customer, we get down to designing the new panel. Considerations like surface features (dams, restricted flow bars), fastening, amongst others, which may not be part of the initial necessity, ensure this new panel will be as modifiable as possible to offer the wonderful traits of modular media. The panel is drawn up and reviewed by multiple parties, which ensures no detail is missed.
4. Test the Panel
The proof is in the testing. The panel is developed and tested, eventually making it to our large offering of dies and corresponding panels. We also assign the new panel a color to make more easily differentiate it from similar panels.
5. Finished!
And then it’s here. While there’s no baby shower for it, we all celebrate the birth of a new panel, since it offers us yet a new set of functions to help our screening partners.
Written by Alex Caruana, Aggregate Territory Manager for Polydeck.
It’s easy to be complacent with screen media solutions that require downtime for cleaning and replacement. Improve your throughput, reduced downtime and increased production with the maximum open area and ease of use of Polydeck's Maxi Panels.
In an industry dating back tens of thousands of years, it’s easy to become complacent when considering success factors and efficiencies in your operation. However, it’s more than possible to design an operation that is efficient and advanced with the right screen media. Polydeck’s Maxi panel screen solutions increase an operation’s throughput and production efficiency in countless ways.
Throughput is, simply put, a production and success measure. In terms of material processing, it means your screen media is doing its job. Efficient screen media meets your machines where they are, allows for ease of cleaning and replacement, and provides maximum screening of material with as little downtime as possible. For many operations, efficiency is critical especially where resources are limited. Stopping to clear plugs and dealing with low open area is simply not an option when efficiency and sustainability are required of the site.
If screen media is not performing as it should, costly stoppages result, requiring workers to spend hours clearing plugging and getting screens to a place where they can begin production again. Polydeck customer Dufferin Aggregates Butler Pit, located in Cambridge, Ontario was experiencing significant downtime from pegging. With a constant focus on their efficiency and production goals, Dufferin did not waste their time seeking a better screen media solution. After the Polydeck team conducted an on-site screen performance analysis and presented their solutions with a guarantee that Dufferin would experience their desired throughput by making the switch, the choice was simple.

Maxi panels’ thin borders are specifically designed with throughput in mind, featuring relief angles to aid in proper screening. Once the panels were put on our customer’s screens, they provided maximum number of openings per square foot. Besides offering leading throughput rates, Maxi panels’ specially formulated polyurethanes combined with engineered panel geometry allowed the panels to flex and retain extended wear life. This innovative design coupled with Polydeck’s injection molding process ensured accurate, consistent open area which resulted in increased overall efficiency at Butler Pit.
Maxi panels also offer an advantage over wire cloth when considering the abrasion resistance of synthetic screen media and ease of use. Operations often default to wire cloth when production requirements are high but Maxi panels offer a significant cost benefit when you factor in downtime needed to change out wire cloth. Maxi panels’ modularity and snap fastenings make changeouts and swaps easy and quick. Less downtime means more productive hours on site. More production means more return from your site. In short, adding Polydeck’s Maxi panels to your operation means you’ll get more from your site than ever before.
The keys to success with screen media lie in today’s technology and the efficiency found in Polydeck’s Maxi panels. As seen at our customer’s site, Polydeck’s Maxi panels reduced downtime and increased production, two very critical elements for success in any operation.
Are you ready to increase the success of your operation?