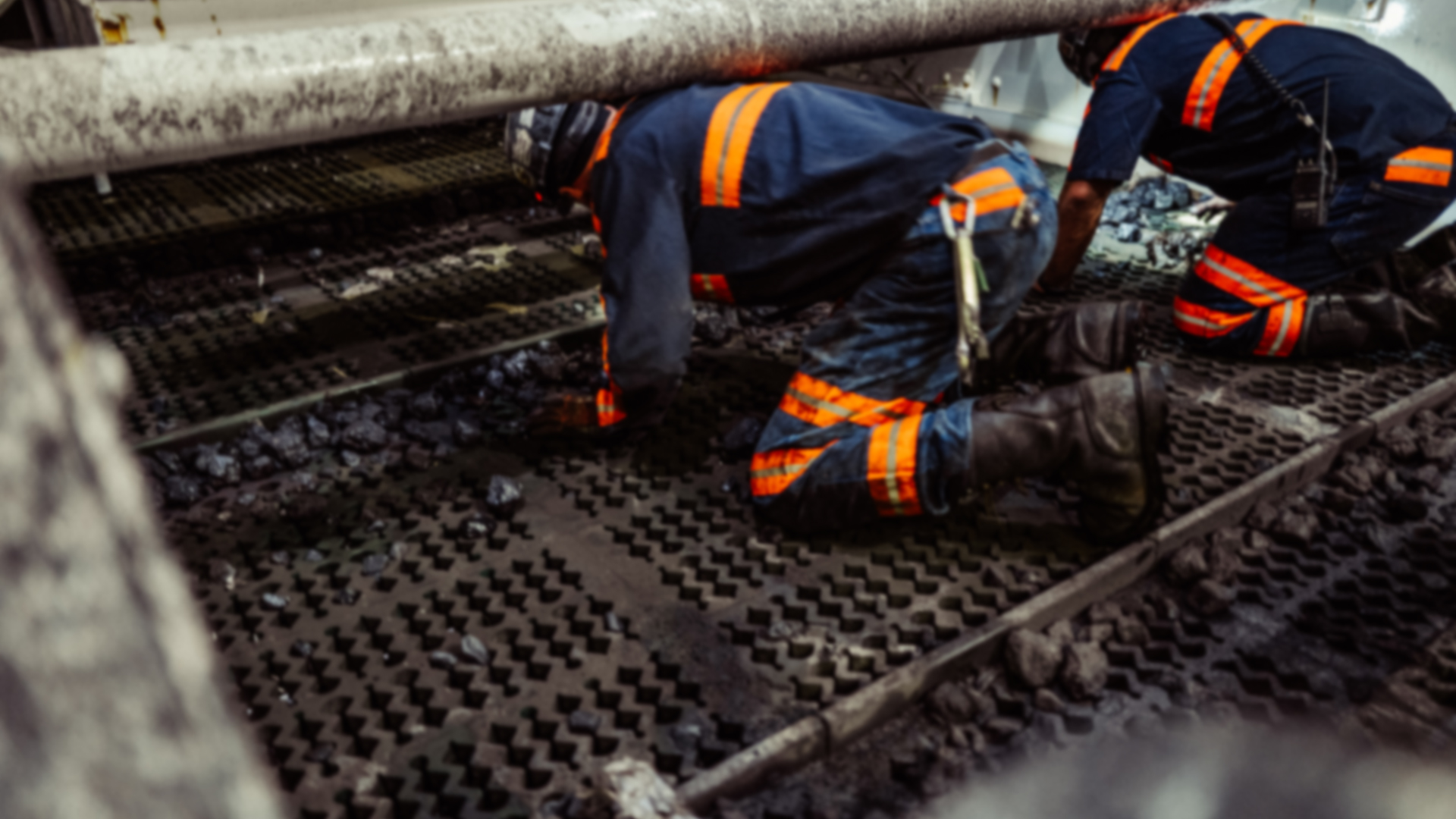
CASE STUDIES
REAL SOLUTIONS. REAL RESULTS.
Plugging Case Studies
Blinding Case Studies
Wear Life Case Studies
Polydeck's custom panel designs, proprietary material formulations, and injection-molded manufacturing process result in product designs that can increase the wear life of your machine as well as your media. Download the case studies below to learn more about the best products that extend wear life.
Throughput Case Studies
The percentage of surface area available for product to pass through a screen panel is directly correlated to the amount of product a plant can produce. Polydeck's screening, frame, and fastening systems increase open area, helping you achieve your production goals. Learn more about increasing throughput by downloading the case studies below.
MINING INDUSTRY
Barrick Golden Sunlight
Barrick Golden Sunlight was accustomed to their heavy gauge wire cloth on their secondary scalping screen producing minus 5-1/2” crushed gold ore. Upon further observation, the excessive travel rate and lack of bed depth were causing issues in their operation.
CASE STUDIES
REAL SOLUTIONS. REAL RESULTS.