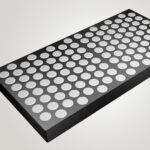
Ceramic Liners: Polydeck’s latest offering!
January 12, 2021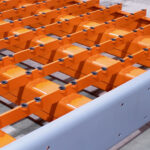
3 Advantages to Polydeck’s PIPETOP™: Increase efficiency while maintaining screen availability with PIPETOP
January 27, 2021Part 1 explains how to make the right decisions BEFORE investing in a screening solution for your operation.
Maximizing the performance and efficiency of synthetic screen media is a combination of art and science. Optimal screening efficiency is the result of a carefully targeted mix of apertures and surface configurations, tailored to each application’s unique needs.
This requires careful selection of the screen media upfront, making sure to use the right form and function for the job, and then performing regular maintenance and quality control during operations.
With the right screening selection and maintenance strategies, producers can boost capacities, maximize uptime, increase product quality, and reduce per-ton costs.
We’re going to take a deeper dive into some of these strategies in this two-part series. Part 1 below explains how to make the right decisions BEFORE investing in a screening solution for your operation.
Form and Function
When selecting screen media for optimal efficiency—given the specifics of the application—there are a number of factors you must consider:
First, take stock of the entire screening circuit to help pinpoint the best media for the job, keeping in mind that precise data yields the best screen panel selection for maximum productivity.
• Is the material wet or dry?
• Is blinding or pegging an issue?
• How does weather or climate affect processing?
• How abrasive is the material?
Next, consider that the best applications for polyurethane and rubber screen media are significantly different. Polyurethane has higher abrasion and sliding resistance, and is more often used in wet applications. Rubber is typically favored in dry applications, and special compounds and design options offer excellent anti-plugging and blinding characteristics.
Both polyurethane and rubber are effective in reducing noise, and because the modular screen panels’ deck surface is customized in one-foot increments, they provide greater control in meeting product specifications.
To help with the selection process, work with a screen media supplier that offers a variety of screen panel options, surface features, and fastening configurations. Rely on the company’s expertise to specify the optimal panel types and opening sizes to meet the given gradations.
Once you determine the right screen media material, the media must be correctly matched to the parameters of the vibrating screen to ensure the circuit keeps pace with the crushing side. Review all potential product mixes to identify any potential gradation inconsistencies and plant bottlenecks, and make necessary adjustments upfront.
If costly maintenance downtime and loss of saleable product due to sand and fines buildup is a concern, anti-blinding panels are highly effective in mitigating the threat. When an operation runs all week without blinding—regardless of the rain or moisture content—it doesn’t take long to get the payback from a new deck surface.
Similarly, to avoid bottlenecks in the screening circuit, you must correctly calculate the open area—the total number of “usable” openings on the screen as a percentage of open holes over the area of the entire screen panel surface. Thinner bridges create greater open area and a more efficient process, although they can potentially decrease a screen panel’s wear life. The open area of the screen deck can also be impacted by the panel support structure.
_______________________________________
In Part 2 (published at the end of August), we’ll look at how a system of regular maintenance and quality control tasks can extend the life of your equipment and deliver the strongest return on your investment. We will also provide you with a downloadable checklist to help your audit.
Contact us for your Screen Performance Evaluation today!